Опилкобетон. Опилки и состав.Плюсы и минусы.В домашних условиях
Опилкобетон – это легкий бетон, состоящий из смеси воды, цемента, извести, глины, песка и опилок. Он применяется для производства строительных блоков и возведения монолитных зданий. По своему составу материал похож на арболит, но содержит более мелкий древесный наполнитель. Применение опилкобетона экологически целесообразно, поскольку он является полностью безопасным, отвечает санитарно-гигиеническим требованиям, кроме этого отличается повышенной теплоизоляцией и звукоизоляцией.
Где используется опилкобетон
Материал широко применяется в сфере строительства малоэтажных жилых и нежилых зданий. Чаще всего его используют при возведении загородных домов, гаражей, хозяйственных построек, фасады которых планируется штукатурить, закрывать сайдингом, вагонкой.
Несущие характеристики материала исключают возможность его использования для возведения многоэтажных зданий. Из опилкобетона можно строить короба высотой до 2-х этажей. Для его применения при кладке более высоких построек требуется проведение точных инженерных расчетов, а также заливка железобетонного армопояса по всему контуру.
Из опилкобетона нередко делается черновая стяжка пола. Для этого используется материал малых марок М5 и М10. Сверху стяжки могут укладываться лаги дощатого пола, ламинат, паркет и т.д. Стяжка совместима с системой водяного и электрического теплого пола.
Преимущества опилкобетона
Главным достоинством материала является применение при его производстве вторсырья. При этом опилки в бетоне не подвергаются горению и гниению, поэтому лишены своих основных недостатков. Их применение при производстве опилкобетона делает его дешевым и доступным.
Кроме пользы рационального применения отходов лесопилок, выбор для строительства опилкобетона имеет и другие положительные стороны:
- Высокие теплозащитные качества.
- Хорошая звукоизоляция.
- Малый вес построенных конструкций.
- Высокая устойчивость к растяжению.
- Огнеупорность несколько часов при температуре пламени 1200°С.
- Простой распил.
Это практически идеальный строительный материал соответствующий современным санитарно-гигиеническим нормам. Хотя в его составе и находятся волокна древесины, но в цементной среде они не могут выступить субстратом для разведения плесени, грибка, конечно при отсутствии чрезмерной влажности. Отдельного внимания заслуживают теплоизоляционные качества материала. Стена из опилкобетона толщиной всего 30 см сопоставима по теплозащитным свойствам с кирпичной кладкой шириной 1 м. Дома из опилкобетона теплые, их содержание на отопление и кондиционирование обходится дешевле.
В сравнении с классическим бетоном опилкобетон на порядок легче. Его применение в строительстве позволяет заливать более легкий фундамент, что существенно снижает общую смету строительства. Кроме этого, стены из опилкобетона способны переносить удары, воздействие на растяжение и изгиб. На них гораздо реже появляются трещины, чем на кладке из кирпича, шлакоблока, газоблока, пенобетона.
Стены из опилкобетона не горят. Хотя они содержат в себе древесину, но способны как минимум несколько часов переносить прямое воздействие пламени температурой 1200°С. При этом поверхность просто обугливается, выделяя небольшое количество дыма. При обугливании стена постепенно истончается, что происходит крайне медленно.
Положительным моментом является и удобство работы с опилкобетонными блоками, панелями. При необходимости они достаточно просто распиливаются ножовкой, бензопилой. Это очень важно для соблюдения шага укладки. В дальнейшем стена из такого материала отлично удерживает саморезы без дюбелей. На них можно без опаски навешивать кондиционер, кухонные шкафчики, полки.
Недостатки опилкобетона
Главным и единственным недостатком опилкобетона выступает уровень его влагопоглощения. В зависимости от плотности материала, впитываемость может составлять от 8 до 12%. Даже при добавлении в раствор опилкобетона специальных водоотталкивающих составов, уровень поглощения влаги может снизиться лишь на 2%. Именно поэтому здания из такого бетона должны иметь кровлю с широкими скатами, что исключает возможность намокания фасадов.
Сильное поглощение влаги также создает определенные трудности при строительстве. Кладка нуждается в качественном укрывании пленкой на время осадков. Также не рекомендуется проводить строительство хранимым под открытым небом материалом, не защищенным даже навесом. Он намного тяжелее, не имеет максимальной марочной прочности.
Требования к опилкам для производства опилкобетона
Для изготовления опилкобетона могут использоваться любые просеянные опилки, но от их качества зависят дальнейшие эксплуатационные характеристики раствора. Наиболее удачным решением считается применение опилок с фракцией частиц 1-5 мм из хвойных деревьев. Самым долговечным является опилкобетон на основе еловых опилок. Используемый наполнитель должен быть просеянным. Присутствие древесной пыли снижает связующие качества.
Состав и фракция опилок влияет на скорость отвердевания материала. Древесина содержит сахар, влияющий на рабочие характеристики цемента. От его концентрации зависит, как быстро изделие из опилкобетона станет достаточно прочным для применения. При использовании опилок из елки, поверхность затвердеет за 10 часов. При применении соснового вторсырья за 15 часов, а при добавлении опилок лиственных пород бетон застывает не менее чем за 4 суток.
Для снижения влияния опилок на цемент, их можно предварительно обработать. Для этого применяются специализированные химические составы или обычное выдерживание на открытом воздухе. Опилки хвойных пород могут окисляться на солнце за 3 месяца, после чего приобретают необходимые качества для производства твердого прочного опилкобетона. Ускорить данный процесс можно выдержав их в воде, а потом полностью высушив под естественными солнечными лучами.
Замачивание и сушка применяются только при кустарном домашнем производстве опилкобетона для собственных нужд. При его изготовлении в промышленных масштабах используется обработка жидким стеклом и хлористым кальцием. Добавление жидкого стекла способствует затвердению опилок, а включение хлористого кальция увеличивает их прочность. Промышленные производители могут также использовать хлористый алюминий, сернокислый натрий или аммиачную селитру. Такие решения делают производство более дорогим, поскольку химикаты используются в пропорции 1 к 40 частям опилок.
Опилкобетон в домашних условиях
Подавляющее большинство присутствующих в продаже блоков из опилкобеотона являются продуктом кустарного производства. Практически нет крупных предприятий производящих данный материал в полном соответствии с действующими требованиями ГОСТ. Продаваемый на рынке материал в своем большинстве совершенно не отвечает заявленным характеристикам и минимальным требованиям, необходимым для строительства.
Дешевизна производства опилкобетона делать его применение в строительстве выгодным, поэтому нередко его изготовляют в нужном количестве сами, непосредственно на стройплощадке. В таком случае опилкобетон заливается в опалубку поэтапно. Он размещается слоями. По мере высыхания опалубка постепенно поднимается вверх, в результате чего получаются несущие стены и перегородки здания. Это достаточно продолжительный и кропотливый процесс. Материал набирает окончательную марочную прочность только через 3 месяца, несмотря на то, что сам цемент достигает максимальных связующих качеств уже спустя 28 дней.
Прочность материала увеличивается по мере его высушивания. В связи с этим монолитное строительство из такого бетона должно проводиться только летом в самые жаркие и засушливые месяцы. Нельзя заливать массу большими слоями, поскольку нижний недосушенный слой склонен к деформации.
При изготовлении блоков из опилкобетона его оставляют в формах как минимум 1 сутки. Если их вытащить раньше, то блок может перекоситься, что приведет к нарушению геометрии.
Пропорции для приготовления опилкобетона
Опилкобетон производится различных марок прочности – М5-М25. Слабый бетон марок М5 и М10 применяется в качестве утеплителя. Его заливают вместо теплоизоляционного материала между кирпичной кладкой стен, применяют для утепления чердаков. Марки М15-М25 подходят для производства несущих стен, при условии отсутствия тяжелого бетонного межэтажного перекрытия.
Для приготовления 1 ведра опилкобетона марки М25 необходимо:
- Стружка – 2 кг.
- Цемент М500 – 3 кг.
- Песок – 6,7 кг.
- Вода.
Также возможно приготовление опилкобетона этой же марки с использованием глины и извести. В таком случае снижается концентрация цемента, что удешевляет производство.
Для замешивания ведра раствора обычно применяется соотношение компонентов:
- Цемент М400-М500 – 2 кг.
- Песок – 5 кг.
- Известь 0,5 кг.
- Глина – 1 кг.
- Опилки – 2 кг.
Очередность смешивания компонентов
Чтобы приготовить опилкобетон с оптимальной однородной консистенцией, важно проводить смешивание компонентов правильно. В первую очередь перемешиваются вяжущие составляющие и песок. После этого добавляются опилки, и только после этого вводится вода. Ее количество определяется визуально, поскольку данный показатель зависит от влажности древесины и песка. Раствор не должен быть жидким. Чем выше его густота, тем меньше дальнейшая усадка при высыхании.
Похожие темы:
пропорции объема ведрами, состав, приготовление
Дата: 21 августа 2017
Просмотров: 4917
Коментариев: 1


Специалистами строительной отрасли ведется постоянный поиск новых материалов. Одной из разновидностей легкого бетона, в котором используются опилки древесины, является опилкобетон. Он характеризуется повышенными теплозащитными характеристиками, огнестойкостью, соответствует санитарно-гигиеническим нормам. Смешивая бетон с опилками несложно приготовить своими руками готовые блоки для постройки коттеджей, домов, а также строений хозяйственного назначения. Важно соблюдать пропорции и технологию изготовления. Рассмотрим детально технологические нюансы, разберемся с различными вариантами рецептуры.


Готовые блоки используют для строительства малоэтажных зданий
Изготовление опилкобетона своими руками
Самостоятельное изготовление легкого бетонного композита осуществляется по следующему алгоритму:
- Выполняется подготовка необходимых материалов. Составляющие нет необходимости приобретать предварительно. Все компоненты можно заготовить непосредственно перед изготовлением, посетив магазины или склады стройматериалов, а также воспользовавшись отходами производства деревообрабатывающих предприятий.
- Смешиваются ингредиенты согласно пропорции. Перемешивание компонентов может осуществляться механическим способом с применением бетоносмесителя или ручным путем с использованием лопат. Автоматизация технологического процесса путем применения бетономешалки повышает производительность, улучшает интенсивность смешивания, положительно влияет на качество продукции.
- Производится формовка. Преимущественно используется групповой процесс формовки, когда предварительно перемешанный состав заливается в несколько десятков форм. Применяются единичные и групповые формы разборной конструкции, изготовленные из древесины толщиной 2 см и обитые металлом или пластиком. Применение полиэтиленовой пленки облегчает извлечение готовых изделий.
- Осуществляется сушка готовой продукции естественным путем. Снятие форм производится через 4–5 суток после заливки путем ослабления затяжки барашковых гаек, извлечения резьбовых шпилек и разборки формовочного ящика. Длится процесс естественной сушки в зависимости от пород древесины до трех месяцев, в течение которых значительно снижается концентрация влаги, и изделие приобретает эксплуатационную прочность.


Стандартный состав бетона с опилками: цементно-песочная смесь, деревянная стружка, известь (по необходимости)
Бетон с опилками – состав и соотношение компонентов
Опилкобетон производится на основе ингредиентов, полученных промышленным путем и составляющих природного происхождения:
- портландцемента марки М300;
- просеянного песка размером до 1,8 мм;
- извести;
- древесных опилок;
- воды.
Опилка следующих видов деревьев обеспечивает необходимое качество продукции:
- сосны;
- ели;
- березы;
- тополя;
- ясеня;
- дуба;
- лиственницы.
Период твердения блоков из различных видов древесины значительно отличается. По скорости набора прочности лидирует сосна, у которой процесс твердения завершается через полтора месяца после заливки. На последней позиции находится лиственница, блоки из которой можно использовать через 3,5 месяца после заливки.


Каждая марка арболита готовится по определенным пропорциям
Концентрация наполнителя и песка влияет на плотность материала. При уменьшении его концентрации удельный вес блоков снижается, что улучшает теплотехнические характеристики, однако уменьшает прочность. Увеличение объема вяжущих ингредиентов и песка повышает водонепроницаемость, а также устойчивость к воздействию отрицательных температур.
Рекомендуемое соотношение компонентов для приготовления состава средней плотности из 100 кг древесной стружки, составляет:
- цемент – 75 кг;
- известь – 50 кг;
- песок – 175 кг.
Пропорции и состав опилкобетона в ведрах
Для приготовления опилкобетона добавлять компоненты ведрами достаточно удобно.
Состав опилкобетона в ведрах регламентируется следующими пропорциями:
- Для марки опилкобетонных блоков М10 соотношение цемента, песка, тырсы и извести составляет 1:2,2:6,5:1,5.
- Опилкобетон, маркируемый М15, включает указанные выше ингредиенты в соотношении 1,2:3:7,8:0,8.
- Блоки с маркировкой М25 содержат портландцемент, просеянный песок, древесную стружку и известь в пропорции 1:2,8:6,4:0,8.


Важно не занижать количества вяжущего материала
На примере материала с маркировкой М10 рассмотрим пропорции ингредиентов при введении ведрами. Смесь включает:
- портландцемент – 1 ведро;
- песок – 2 ведра с горкой;
- опилки – 6 с половиной ведер;
- известь – полтора ведра.
Соблюдая указанные пропорции несложно своими руками подготовить раствор для изготовления блоков различных марок.
[testimonial_view id=”17″]
Опилкобетон – приготовление смеси
Технологический процесс приготовления смеси можно осуществлять следующим образом:
- подготовить цементный раствор путем разведения портландцемента водой с последующим добавлением просеянного песка, извести, древесной стружки;
- осуществить смешивание извести с тырсой, затем ввести портландцемент с песком, развести перемешанные ингредиенты водой.
Независимо от выбранного метода приготовления, необходимо обеспечить однородность смеси. Важным моментом технологии является предварительная сушка стружки, уменьшающая концентрацию влаги. Правильно приготовленная смесь начинает твердеть через пару часов. Именно поэтому важно готовить раствор в объеме, соответствующем количеству имеющихся форм. При укладке бетонной смеси следует тщательно уплотнить состав с целью недопущения образования воздушных пор.


Следует знать, что известь повышает взаимные адгезионные способности компонентов песко-цементного композита
Растворы для различных марок
В зависимости от концентрации ингредиентов опилкобетонные блоки делятся на следующие марки:
- М5. Характеризуется пониженной до 0,6 т/м3 плотностью, уменьшенным коэффициентом теплопроводности, равным 0,18. На один 50-килограммовый мешок цемента необходимо взять по 0,2 тонны опилок и извести, а также 20 кг присеянного песка;
- М10. Коэффициент теплопроводности составляет 0,21, а удельный вес возрастает до 0,8 т/м3. Для приготовления мешок портландцемента необходимо перемешать со 100 кг стружки и 100 кг песка, а также добавить 80 кг извести;
- М15. Плотность и коэффициент теплопроводности увеличиваются и составляют, соответственно, 0,8 т/м3 и 0,24. Для приготовления на 50 кг цемента вводится 70 кг тырсы, 30 кг извести и 115 кг песка;
- М20. Удельная плотность достигает величины 0,95 т/м3, а величина коэффициента теплопроводности увеличивается до 0,3. Опилкобетон готовится путем смешивания по 50 кг цемента и опилок с добавлением 130 килограмм песка и 15 кг извести.
С увеличением марки опилкобетона возрастает коэффициент теплопроводности, увеличивается плотность. Блоки высоких марок позволяют возводить увеличенные помещения, в которых из-за высокого коэффициента теплопроводности сложно поддерживать комфортный температурный режим. Введение специальных добавок, вымачивание древесного сырья в жидком стекле и известковом молоке позволяет использовать сырье с увеличенной влажностью и повышает огнестойкость блоков.


Марка М10 требует такие количества: полведра вяжущего сырья, ведро с горкой очищенного песка и немногим больше трех ведер со стружкой
Готовность перемешанных компонентов определяется путем сжатия подготовленной смеси ладонью. Пластичный и готовый к формовке материал сохраняет следы пальцев, что свидетельствует о готовности раствора к заливке.
Введение в раствор глины вместо извести
В состав материала допускается вводить вместо извести глину, что не сказывается на качестве изделий. Технология использования глины предусматривает следующие этапы:
- смешивание древесного сырья с портландцементом и песчаной массой;
- введение в смесь глиняного теста, тщательное перемешивание;
- добавление воды небольшими дозами;
- перемешивание состава до рабочей консистенции.
Предусмотренные рецептурой пропорции известкового и глиняного теста остаются неизменными.
Раствор на основе гипсового вяжущего вещества
Допускается в качестве вяжущего вещества использовать строительный гипс вместо портландцемента. Может возникнуть вопрос, как замедлить интенсивность твердение гипса при смешивании с водой? Проблема довольно просто решается введением в воду моющего средства, которое способствует замедленному твердению гипса.


Для обеспечения высокой скорости твердения в М5 добавляют гипс
Особенности применения строительного гипса:
- увеличение по сравнению с цементом скорости твердения блоков в 5 раз;
- незначительное увеличение затрат на изготовление опилкобетонной продукции.
Среди специалистов по строительству ведется полемика о возможности применения опилкобетонных блоков на основе гипса для возведения наружных стен зданий. Надежная защита опилкобетона от отрицательного влияния атмосферных факторов позволяет решить проблему поглощения материалом влаги.
Размер опилок
Несмотря на то что в ряде источников отмечается необходимость просеивания опилок на сите с квадратной ячейкой размером 1 см, размер используемой стружки не имеет принципиального значения.
Важно обратить внимание на следующие моменты:
- следует вводить древесное сырье, являющееся вяжущим веществом, в требуемом количестве;
- проблематично получить однородный состав при использовании опилок, крупность которых отличается в сотни раз;
- древесная стружка с калибровочных станков и оцилиндровочного оборудования не используется при изготовлении опилкобетона;
- целесообразно применять опилки с пилорамы, оснащенной ленточной пилой или дисковым рабочим органом.
Жирные растворы, содержащие вяжущее вещество в избыточном количестве, менее восприимчивы к крупности опилок по сравнению с тощими составами.
Итоги
Руководствуясь пропорциями, приведенными в материале статьи, несложно своими руками подготовить качественную смесь для изготовления опилкобетона необходимой марки. Самостоятельно изготовленные с соблюдением технологии опилкобетонные блоки отличаются прочностью, морозостойкостью, доступной ценой. Освоив технологию изготовления, можно оценить достоинства экологически чистого и простого в изготовлении материала.


На сайте: Автор и редактор статей на сайте pobetony.ru
Образование и опыт работы: Высшее техническое образование. Опыт работы на различных производствах и стройках – 12 лет, из них 8 лет – за рубежом.
Другие умения и навыки: Имеет 4-ю группу допуска по электробезопасности. Выполнение расчетов с использованием больших массивов данных.
Текущая занятость: Последние 4 года выступает в роли независимого консультанта в ряде строительных компаний.
отзывы строителей, технология производства, состав и свойства :: SYL.ru
Одной из разновидностей легких бетонов является опилкобетон, который производится с использованием древесных опилок и отличается пониженной плотностью. Материал был разработан в Советском Союзе, еще в 60-х годах прошло века. Позже он прошел все качественные и технические испытания и был стандартизирован. Массовое применение опилкобетона в домостроении началось лишь в середине 90-х. С тех пор, благодаря своим уникальным свойствам, он стал пользоваться большой популярностью среди строителей. Сегодня мы с вами узнаем, что собой представляет опилкобетон, как он производится и какие отзывы оставляют о нем строители.
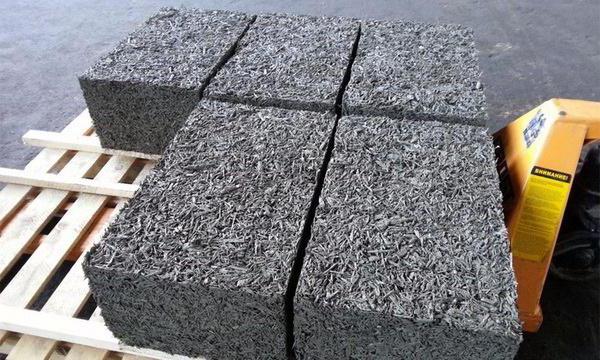
Область применения
Данный материал отличается такими качествами: экологичность, огнестойкость, прочность, паропроницаемость, морозостойкость и доступность. Он широко используется при строительстве домов и хозяйственных построек небольшой этажности. Кроме того, как показывают отзывы строителей, опилкобетон отлично подходит для работ по утеплению и ремонту зданий. Реконструкция с использованием этого материала позволяет не усиливать фундамент.
При строительстве дома из опилкобетона можно пользоваться проектом, разработанным под любой другой материал. При этом затраты на строительство будут существенно ниже. Стены из опилкобетона мало весят, поэтому используя этот материал, совсем необязательно закладывать слишком сложный фундамент.
Состав
Как можно понять из названия, определяющим элементом этого материала являются древесные опилки. Кроме того, в состав опилкобетона входят песок, цемент, а также глина или известь. Благодаря благоприятным санитарно-гигиеническим показателям материал оптимален для возведения стен жилых помещений.
Плотность строительного материала зависит от соотношения опилок и песка. Чем больше в опилкобетоне песка и вяжущих материалов, тем больше его плотность. В таком случае материал обладает высокими прочностными, но низкими теплотехническими характеристиками. С увеличением количества опилок прочность понижается. Вместе с ней снижается морозостойкость материала и его водонепроницаемость, что, в свою очередь, негативно сказывается на коррозионной стойкости стальной арматуры. Арматура используется при укладке стен. Из вышесказанного можно сделать вывод, что прежде чем начать возводить дом из опилкобетона, необходимо изучить особенности влияния состава материала на его свойства. Выбирая тот или иной состав, стоит принимать во внимание толщину стен, этажность здания и назначение стен (внутренняя, наружная или же несущая).
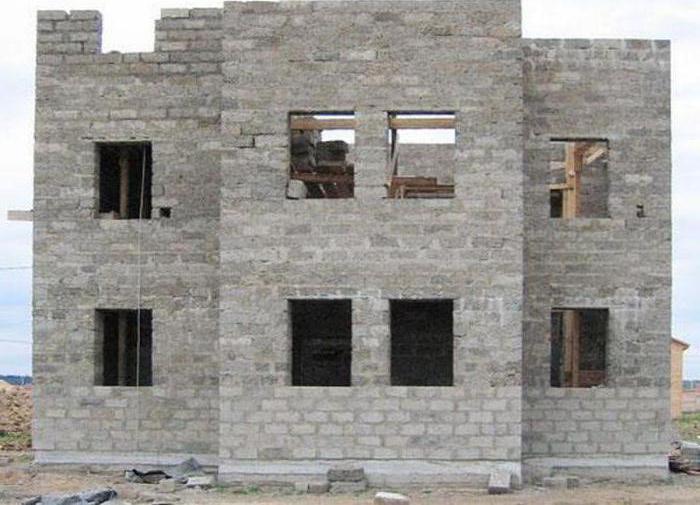
Марки опилкобетона
Пропорции, по которым смешивают компоненты, могут быть разными. Обычно выделяют четыре марки опилкобетона:
- М5. На 100 кг опилок приходится 25 кг цемента, 25 кг песка, 100 кг извести или глины. Плотность такого материала равна 500кг/м3.
- М10. На 100 кг опилок приходится 50 кг цемента, 100 кг песка и 75 кг извести или глины. Плотность этой марки составляет уже 650 кг/м3.
- М15. На 100 кг опилок приходится 75 кг цемента, 175 кг песка, 50 кг извести или глины. Плотность этой марки равна 800 кг/м3.
- М20. На 100 кг опилок приходится 100 кг цемента, 250 кг песка, 25 кг извести или глины. Это самый плотный материал – 950 кг/м3.
Стеновые блоки первых двух марок применяются для возведения, утепления и реконструкции подвалов, так как они имеют прекрасные теплоизоляционные характеристики. Третья и четвертая марка отлично подходит для строительства внутренних и наружных стен зданий.
Теперь поэтапно рассмотрим процесс изготовления опилкобетона своими руками.
Заготовка материалов
Технология производства опилкобетона проста, поэтому многим не составит труда освоить ее в домашних условиях. Компоненты, из которых изготавливается материал, хороши тем, что нет необходимости в их предварительной заготовке. Все составляющие без проблем можно купить в строительном магазине или на рынке, прямо в день изготовления. Итак, для самостоятельно производства опилкобетона необходимо приобрести такие материалы: опилки, песок, цемент, глина или известь.
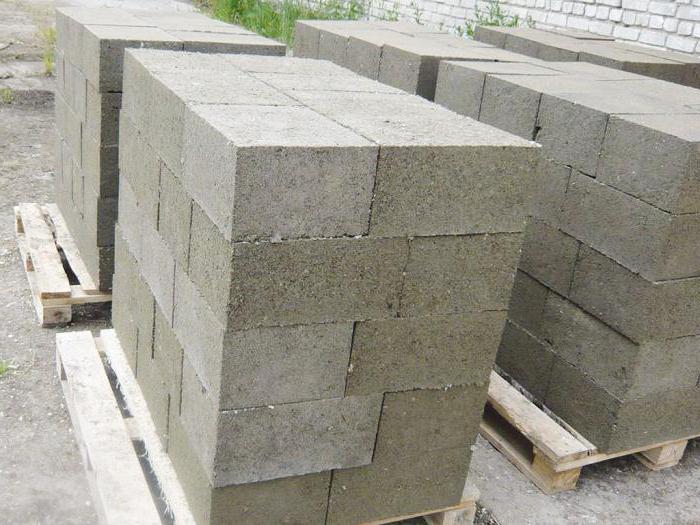
Смешивание
Одной из наиболее трудоемких стадий в производстве опилкобетона (своими руками изготовить блоки может даже начинающий строитель) является перемешивание, поэтому рекомендуется использовать бетономешалку или хотя бы растворосмеситель. Это позволит сделать процедуру смешивания не только более комфортной, но и более качественной. Прежде чем засыпать высушенные опилки в бетономешалку, их нужно просеять через сито со стороной ячейки 1 см. Затем можно смешать опилки с цементом. Лишь после этого в смесь добавляют глиняное или известковое тесто, заготовленное заранее. Все компоненты нужно тщательно перемешать и развести водой. Воду нужно добавлять малыми порциями. После каждого долива необходимо перемешивать смесь опилкобетона. Пропорции компонентов устанавливаются индивидуально, в зависимости от назначения конечного изделия. Чем больше нагрузки будет приходиться на блоки, тем выше их марка.
Если замес опилкобетона произведен надлежащим образом, то при сжатии в кулаке смесь будет образовать пластичный комок, на котором при отсутствии капель воды будут просматриваться вмятины от пальцев. Это считается основным показателям правильно приготовленной смеси.
Формирование блоков
Когда смесь готова, ее нужно тщательно утрамбовать в заготовленные заранее формы. В этом деле ни в коем случае нельзя медлить, так как через полтора-два часа смесь быстро начинает затвердевать. В формах блоки остаются на 3-5 дней. Затем каркас убирается, а изделия продолжают сушиться на протяжении месяца. По прошествии этого времени с блоками можно начинать работать, однако полное высушивание происходит лишь после 3 месяцев, поэтому с облицовкой торопиться не стоит. Подробнее о том, сколько сохнет опилкобетон, поговорим немного ниже.
Форма для отливки
Опилкобетон можно использовать в монолитном строительстве с применением опалубок. Однако чаще всего строители предпочитают не монолитный опилкобетон, а блочный. Формы для отливки блоков изготавливаются в первую очередь, т. к. после замешивания смеси они должны быть полностью готовы. Поскольку процесс высыхания блоков довольно продолжителен, рекомендуется сделать сразу 10-20 форм.
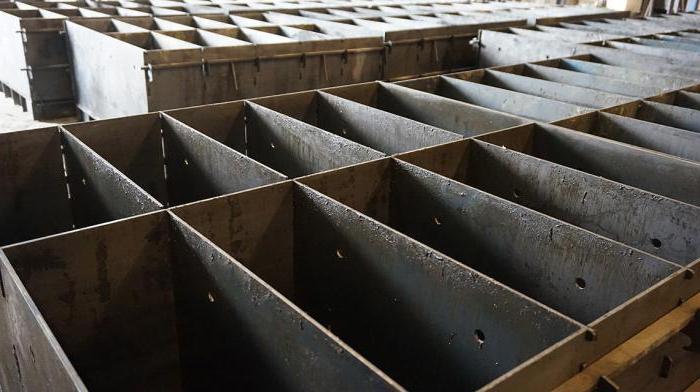
Для крупных блоков изготавливаются разборные двойные или даже одинарные формы. По сути, они представляют собой сбитые из досок ящики разъемной конструкции. Для этих целей обычно используют доски толщиной 2 см. Отдельные части конструкции скрепляются между собой Г-образными стальными стержням, с резьбой М8 под барашковую гайку.
Для небольших блоков изготавливают «остовые» каркасы из тех же 20-миллиметровых досок. В основном форму делают сразу на 9 ячеек. По желанию количество ячеек можно варьировать как в большую, так и в меньшую сторону. Внутренние доски конструкции крепятся друг к другу с помощью задвижных пазов, а наружные – с помощью Г-образных стержней.
Чтобы доски, из которых изготовлена форма для отливки, не впитывали влагу, внутренние стенки конструкции обивают пластиком или кровельной сталью, или же попросту прокладывают полиэтиленом. Это не только позволяет обезопасить дерево от влаги, но и облегчает процедуру вынимания застывших блоков.
Размер блоков
Размер опилкобетоновых блоков стандартами не установлен. Он может зависеть от ряда показателей: толщина стен, ширина проемов и простенков, расстояние между проемами и углами здания и способа укладки. Для более удобного возведения здания длины участков стен устанавливаются таким образом, чтобы они были кратны размерам блоков.
Для простоты подсчетов и унификации проекта толщина блока обычно равняется 140 мм – две толщины кирпича (красного), с учетом уложенного между ними раствора. Такой подход очень практичен, учитывая, что в процессе укладки часто дополнительно используется красный кирпич. Чтобы блоки быстрее высыхали и имели лучшие теплозащитные свойства, в них делается 2-3 отверстия.
Учитывая, что при высыхании блоков происходит их усушка, внутренние размеры форм для литья должны быть примерно на 10 % больше предполагаемых размеров блоков. Так, к примеру, для блока габаритами 120 х 250 х 140 мм необходима ячейка размерами 132 х 275 х 154 мм.
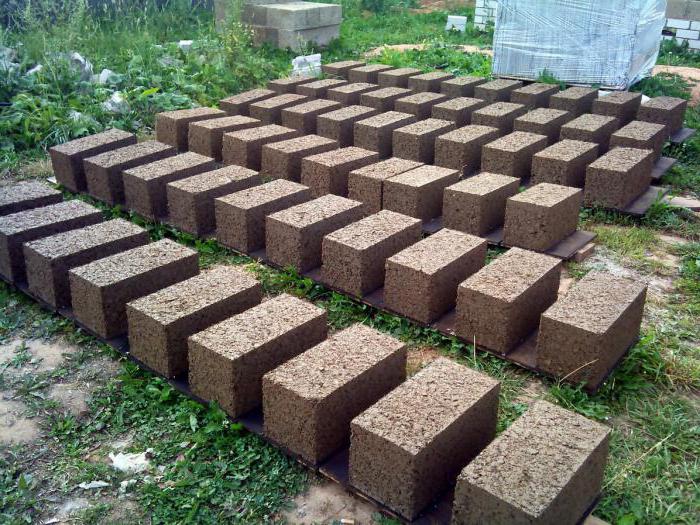
Нюансы
Прежде чем заполнить деревянные формы опилкобетонной смесью, их устанавливают на ровные пластиковые или стальные поддоны, посыпанные тонким слоем опилок. Затем внутри ячеек устанавливают деревянные пробки, обернутые толем, которые необходимы для получения отверстия в блоках.
Когда смесь уложена в форму, ее трамбуют специальной трамбовкой. На протяжении последующих 3-5 дней материал приобретает от 30 до 40 процентов марочной прочности. По истечении этого срока форму для литья разбирают, а пробки извлекают из блоков. Готовые, но еще не высушенные изделия оставляют на этом же месте на 3-4 дня. За это время их прочность возрастает уже до 60-70 процентов.
Окончательная сушка
Последней стадией изготовления опилкобетона является сушка. Для окончательной сушки блоки необходимо перенести под навес или накрыть полиэтиленом. Желательно, чтобы они находились на сквозняке. Укладывая блоки, необходимо оставлять между ними зазоры для вентиляции. Как правило, укладку производят в виде столбов. Для начала на два обожженных кирпича кладут пару стеновых блоков, затем поперек них еще пару и так далее. Спустя месяц блоки затвердеют, высохнут и достигнут 90 % прочности. Чтобы они получились максимально прочными, рекомендуется подождать еще три месяца, прежде чем начать строительство. Пренебрегать этим правилом или нет – решать вам, все зависит от типа здания, для которого заготавливается материал. К примеру, для возведения бани из опилкобетона вовсе не обязательно ждать, пока изделия высохнут на 100 %. Полностью готовые блоки должны быть твердыми, прочными и не иметь трещин. При падении с метровой высоты они не должны разбиваться.
Опилкобетон: отзывы строителей
Опираясь на отзывы опытных строителей, перечислим основные достоинства и недостатки данного материала. Как несложно догадаться, опилкобетон подкупает прежде всего своей экологической чистотой и теплозащитными характеристиками. Благодаря последней особенности в процессе возведения здания нет необходимости в дополнительной теплоизоляции стен, что позволяет существенно сэкономить. Многолетний опыт использования опилкобетона показал, что он в разы превосходит другие материалы с точки зрения изоляции тепла. Так, 30-сантимтеровая стена из таких блоков сохраняет тепло также же, как метровая стена из кирпича.
Кроме того, из-за малого веса материала существенно снижается нагрузка на фундамент. Следовательно, возведение фундамента для дома из опилкобетона получается куда менее затратным.
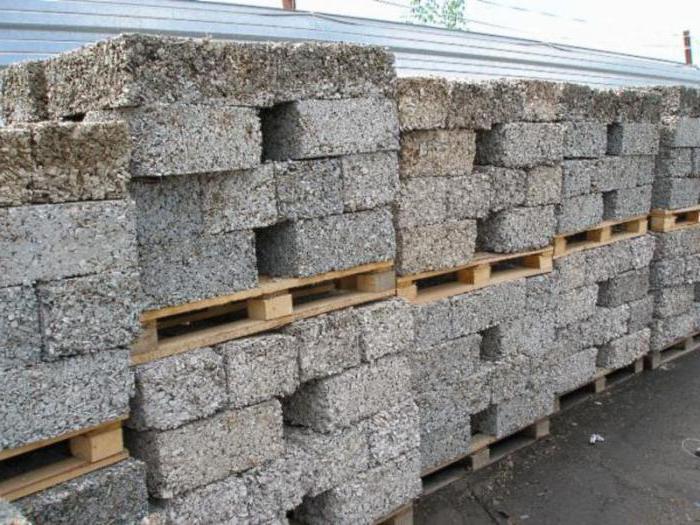
Еще одним достоинством материала является его долговечность. Как показывают отзывы строителей, опилкобетон стоек к деформациям и ударным нагрузкам. Несмотря на наличие в составе большого количества древесных опилок, материал, в силу содержания в нем песка и цемента, является довольно огнестойким. При температуре 1200 °С он на протяжении двух часов не воспламеняется.
В работе опилкобетон довольно податлив – его без проблем можно пилить, сверлить и фрезеровать. Материал устойчив к морозу, плесени и грибку, а также не подвержен гниению. Со штукатурной и бетонными составами он сцепляется хорошо, ровно, как и с лакокрасочными и клеящими средствами.
Конечно же, без недостатков тоже не бывает. Как показывают отзывы строителей, опилкобетон имеет лишь одну слабую сторону – водопоглощение. Чем выше этот показатель, тем ниже качество материала. В зависимости от марки опилкобетона его влагопоглощение может составлять от 8 до 12 %. Его можно снизить на 2-4 % путем обработки блоков водоотталкивающими составами.
Для сравнения приведем показатели влагопоглощения для других распространенных материалов:
- Глиняный кирпич – 2-4 %.
- Керамзитобетон – 8 %.
- Газо- и пенобетон – 8-10 %.
- Железобетон – 3 %.
- Газо- и пеносиликат – 8-10 %.
- Полистиролбетон – 8 %.
Таким образом, если опилкобетон и уступает по влагопоглощению некоторым материалам, то не столь существенно, чтобы отказываться от его преимуществ. А если учесть, что при использовании специальных составов можно довести этот показатель до вполне приемлемых значений, то данный материал и вовсе будет лидировать по сравнению с некоторыми аналогами.
Выбор и обработка опилок
Для изготовления качественных блоков рекомендуется использовать опилки хвойных пород древесины размером до 5 мм. Благодаря однородному гранулированному строению они имеют хорошую текучесть, которая крайне важна в процессе прессования опилкобетонной смеси в формы. Кроме того, эти опилки менее подвержены процессам биологического разложения. Чаще всего применяют еловые опилки, так как они имеют наиболее благоприятные характеристики, важнейшей из которых является содержание водорастворимые веществ – 1,12 %. Для сравнения познакомимся с содержанием водорастворимых веществ в опилках других пород: тополиные – 1,12 %, березовые – 1,3-1,45 %; сосновые – 2,2-6,2 %; дубовые – 2,5-7,3 %; ясеневые – 2,2-5,8 %; лиственничные – от 10,6 %.
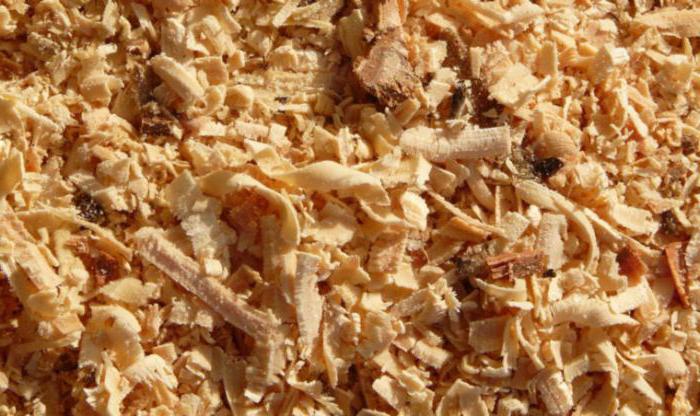
Время, необходимое на схватывание цементно-опилочной смеси, также зависит от породы дерева. Так, смесь, содержащая опилки ели, полноценно схватывается за 10-12 часов. При использовании опилок лиственничных пород этот показатель составляет уже 90 часов. С целью уменьшения влияния органических водорастворимых веществ на цемент, опилки обрабатывают химическим или физическим путем. Самый простой способ обработки – окисление органических элементов на воздухе, желательно под солнечными лучами. При нахождении опилок на теплом воздухе одна часть веществ окисляется сразу, а другая – сначала бродит, затем частично окисляется, остекляется или кристаллизуется, приобретая нерастворимую форму. Недостатком этого метода обработки является его длительность. Чтобы хвойные опилки окислись на воздухе, понадобится 2-3 месяца, для лиственных этот показатель возрастает в два раза.
Второй способ избавления стружки от водорастворимых соединений – обработка водой. Для этого опилки или выставляют на длительное время под дождь, или вымачивают. По времени это способ также продолжителен, так как материал долго сохнет.
Третий и самый распространенный способ – обработка раствором жидкого стекла или хлористого кальция. Здесь есть два нюанса. С одной стороны, при обработке жидким стеклом материал менее прочен, а с другой – для успешной обработки хлористым кальцием понадобится хорошо выдержанная хвойная древесина.
Арболит
Часто опилкобетон путают с другим строительным материалом – арболитом, что совершенно неверно. Согласно ГОСТу, арболит определяется как бетон на цементном вяжущем, химических добавках и органических растворителях. Однако в классическом варианте арболитобетон предполагает использование древесной щепы. Именно она и определяет его уникальные свойства.
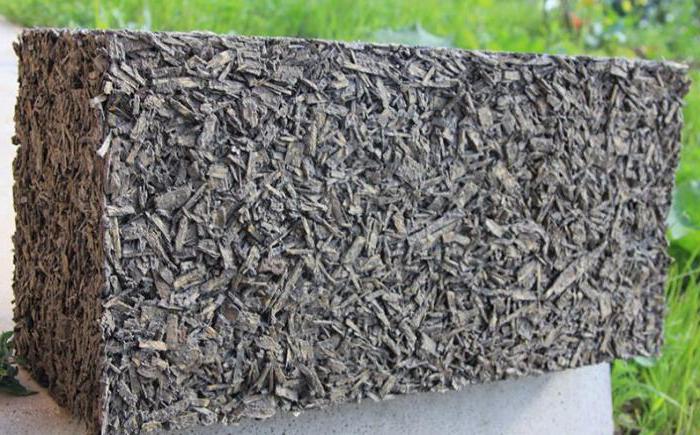
Ровно, как и опилкобетон, арболит является экологически благоприятным стеновым материалом, отличающимся высокими показателями огнестойкости и теплоизоляции. Тем не менее эти два материала, несмотря на схожесть структуры, имеют принципиальное отличие. Дело в том, что в производстве арболита вместо мелких древесных опилок, которые не могут обладать достаточными прочностными свойствами сами по себе, используют специальную древесную щепу, размер которой строго нормируется. Опилки, в отличие от щепы, не могут в достаточной мере армировать (усиливать) стеновой блок и давать ему «пластичность». Таким образом, арболитобетон прочнее опилкобетона с точки зрения прочности на изгиб и способности к временной деформации без полного разрушения. Справедливости ради стоит отметить, что опилкобетон по этому показателю превосходит остальные виды легких бетонов.
Для упрочнения блоков, заполнения пустот и уменьшения усадки в состав опилкобетона добавляют много песка, а для экономии вяжущего материала – также немало извести или глины. Использование большого количества песка негативно сказывается на огнестойкости рассматриваемого нами материала – при температуре +573 °С опилкобетон изменяется в объеме, что может привести к растрескиванию. Кроме того, из-за весомого содержания песка снижаются конструкционные характеристики блоков. Так, чтобы опилкобетон достиг прочности марки М25, его плотность должна составлять 950кг/м3. Из-за высокой плотности стоимость материала и его доставки повышается, а проведение строительных работ – усложняется.
У арболита аналогичной марки плотность составляет от 500 до 700 кг/м3. Учитывая, что с повышением удельного веса теплосберегающие свойства падают, теплопроводность опилкобетона и арболита отличается более чем в два раза в пользу последнего. Такая разница обусловлена невысоким количеством древесины в опилкобетоне по сравнению с арболитом: примерно 50 % против 80-90 % щепы. Это негативно сказывается на таком свойстве, как обеспечение пассивной вентиляции помещения. Здесь, опять же, стоит отметить, что по этому параметру опилкобетон значительно превосходит большую часть стеновых материалов. Он отлично подходит для строительства зданий малой этажности и уступает лишь своему «сопернику».
Таким образом, называть опилкобетон арболитом крайне некорректно, так как это совершенно разные материалы. Единственное сходство между ними – наличие древесного компонента в составе.
пропорции, состав, как готовить раствор
Отличные характеристики и состав опилкобетона позволяют применять его в строительстве монолита и мелких стеновых блоков малоэтажных зданий. Опилки — продукт органических отходов, поэтому теплоотдача нового строительного материала больше, чем обычного бетона. Поскольку на строительном рынке такого материала нет, строители изготавливают его сами. Однако к опилкобетонным блокам применяют требования ГОСТа 6133–99, как и к другим бетонным камням. Поэтому нужно знать технологию изготовления и придерживаться указанных пропорций.
Посмотреть «ГОСТ 6133-99» или cкачать в PDF (2.4 MB)
Состав и марки
Компонентами этого строительного материала являются:
- Цемент, выполняющий роль вяжущего вещества, который должен в соответствии с ГОСТом 10178−85 не ниже М400.
- Крупный и средний песок, отвечающего ГОСТу 8736—93.
- Опилки всех пород деревьев, преимущественно хвойных, поддающихся меньшему гниению.
- Добавки: известь, глина, сульфат аммония, жидкое натриевое стекло. Но наиболее подходит требованиям ГОСТ присоединение кальция хлорида.
- Вода незагрязненная — ГОСТ 23732–79.
Посмотреть «ГОСТ 10178-85» или cкачать в PDF (181.6 KB)
Посмотреть «ГОСТ 8736-93» или cкачать в PDF (557.4 KB)
Посмотреть «ГОСТ 23732-79» или cкачать в PDF (117.1 KB)
Плотность опилкобетона зависит от количества, в первую очередь, песка, который вместе с другими добавками повышает качественные показатели материала.
Название | Плотность, т/м3 | Коэффициент теплопроводности |
М5 | 0,6 | 0,18 |
М10 | до 0,8 | 0,21 |
М15 | 0,8 | 0,24 |
М20 | 0,95 | 0,3 |
Плюсы и минусы
Бетон с опилками обладает уникальными качествами по сравнению с другими строительными материалами:
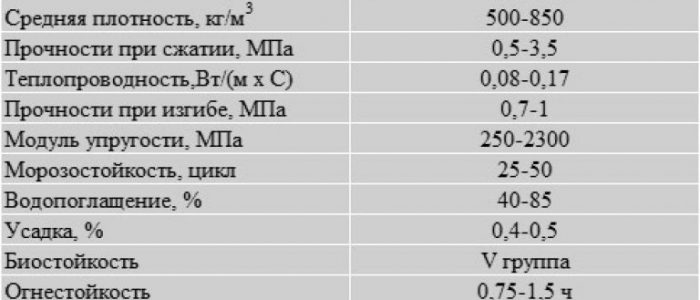
- экологическая безопасность применения;
- легкий вес;
- необходимые показатели удержания тепла;
- простая обработка при строительстве;
- стойкость на прочность растяжения и изгиба;
- народный (доступный) состав.
Однако присутствуют и недостатки:
- Достаточная степень впитывания влаги, требующая проведения работ во избежание этого.
- Возрастание финансовых затрат в строительстве многоэтажных зданий из-за прибавления цемента. Дом из опилкобетона, который набрал природную прочность, будет качественнее, чем из бетона обычного.
- Большая вероятность усадки затрудняет работы по отделке.
Какой расход и пропорции?
Название | Опилки | Песок | Цемент | Известь или глина | Пропорции (цемент, песок, опилки, известь) |
М5 | 80 | 3 | 4,5 | 14 | 1:0:2:1 |
М10 | 80 | 12 | 9,5 | 10,5 | 1:2,2:6,5:1,5 |
М15 | 80 | 21 | 13,5 | 7 | 1,2:3:7,8:0,8 |
М25 | 80 | 30 | 18 | 35 | 1:2,8:6,4:0,8 |
Как готовить раствор?
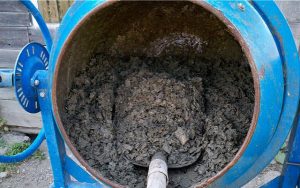
Для строительства жилых зданий и хозяйственных построек несложно изготовить опилкобетон своими руками. Используют 2 способа присоединения компонентов:
- Разводят в цемент в воде, а потом добавляют остальные ингредиенты.
- Смешивают сухие вещества и разбавляют водой.
Нет преимущества выбора варианта приготовления. Важно, чтобы образовалась однородная структура, в состав которой входят песок и цемент, образующие цементный камень. При самостоятельном изготовлении бетономешалка не понадобится, так как ручной способ — удобный, хотя и трудоемкий процесс. Сжатая в кулаке правильно приготовленная смесь не выделяет капель воды.
как сделать, состав, рецепт смеси
К категории легких бетонов относятся блоки из опилкобетона, которые, при соблюдении рецептуры замешивания раствора и технологии изготовления, можно приготовить самостоятельно. В качестве основного компонента, входящего в состав изделия, используются опилки. Именно они придают изделию индивидуальные качества, за которые так ценится этот материал. Опилкобетонные блочные элементы имеют свои плюсы и минусы, с которыми важно ознакомиться перед тем, как начать их использовать.
Характеристики и свойства
Физико-технические характеристики, условия эксплуатации, параметры, правила применения опилкобетонных блоков контролирует ГОСТ 6133–99. Этот материал относится к категории легких бетонов, из него можно возвести не только дом, гараж, хозпостройку, но и обустроить прочный фундамент и цоколь. Стройматериал обладает высочайшими санитарно-техническими качествами, благодаря чему его часто используют в виде основного сырья для возведения медицинских и детских учреждений.
Посмотреть «ГОСТ 6133–99» или cкачать в PDF (2.4 MB)
С характеристиками опилкоблоков можно ознакомиться, изучив таблицу:
Показатель | Среднее значение |
Прочность, МПа | 0,5—3,5 |
Плотность, кг/м3 | 550—850 |
Теплопроводность | 0,08—0,17 |
Морозостойкость, циклы | 20—50 |
Влагопоглощение, % | 40—85 |
Огнеупорность, ч | 0,75—1,5 |
Разновидности
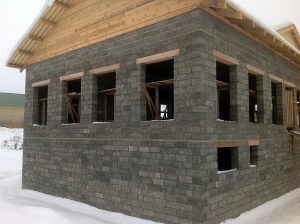
В зависимости от предназначения, опилкоблоки бывают таких разновидностей:
- теплоизоляционные;
- конструкционные.
По плотности материал делится по классам М5, 10, 15, 20. Самый плотный блок марки М5. Именно он используется в качестве основного материала для возведения домов из опилкобетона. Ремонт стеновых поверхностей осуществляется с использованием изделий класса М10, а вот для облицовки и обустройства межкомнатных перегородок больше подойдут блоки М15 и 20.
Плюсы и минусы
Прежде чем начать изготовление опилкобетона в домашних условиях, следует детально знакомиться с достоинствами и недостатками этого стройматериала. Из плюсов выделяют такие:
- малый вес;
- повышенная степень шумоизоляции;
- абсолютная экологическая безопасность;
- доступность по цене;
- простота кладки и легкость обработки;
- надежность, долговечность.
Главные недостатки изделия такие:
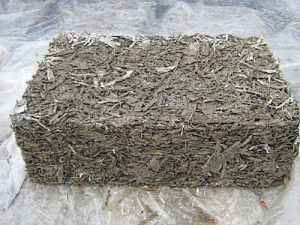
- длительный цикл приобретения заявленных эксплуатационных характеристик;
- высокий коэффициент влагопоглощения;
- возможность использования опилок только определенных пород древесины.
Состав опилкоблоков
Чтобы сделать опилкобетонные блоки своими руками, сначала полезно изучить состав материала, после чего запастись качественным сырьем. Смесь для изготовления блочных элементов состоит из таких компонентов:
- портландцемент;
- песок;
- древесная щепа;
- глина или гашеная известь;
- вода.
Опилки для изготовления стройматериала берутся только из определенных пород древесины. Чтобы изделие получилось качественным и устойчивым к гниению и размножению микроорганизмов, рекомендуется использовать щепу, полученную после обработки таких хвойных пород деревьев:
- сосна;
- пихта;
- ель.
Но допустимо использовать и опилки, оставшиеся после распила таких деревьев:
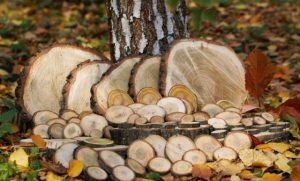
- тополь;
- граб;
- бук;
- дуб;
- ясень;
- береза.
Как сделать своими руками?
Рецепт смеси
Пропорции опилкобетона определяют коэффициент плотности и прочности готового материала. Чтобы приготовить бетон повышенной плотности, потребуются компоненты в таких количествах:
- щепа — 1 т;
- цемент — 1 т;
- песок — 2,5 т;
- известь 250 кг.
Помимо соблюдения указанных пропорций, немаловажно придерживаться порядка перемешивания компонентов. Сначала необходимо соединить требуемое количество песка с цементом, тщательно перемешать. После добавляются опилки и известь, опять смешивается. В конце понемногу доливается вода, до получения требуемой консистенции. Чтобы бетонное тесто получилось однородным, рекомендуется готовить его в бетоносмесителе.
Правильно приготовленный раствор эластичен, после сжатия остается в той же форме, не рассыпается и не деформируется.
Опалубка и формы
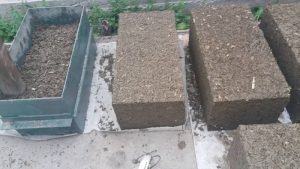
Чтобы блоки вышли одинакового размера, рекомендуется приобрести или сделать самостоятельно формы для заливки. Опалубка изготавливается из деревянных досок, рекомендуется делать разборные формы, чтобы можно их было быстро собрать, а потом разобрать. Смесь укладывается в формы, тщательно трамбуется. За 3—4 часа раствор схватывается, однако изделие должно вылежаться 5—7 дней. Сушку опилкоблоков проводят в хорошо проветриваемом помещении. Затем блоки выкладываются в невысокие столбы, где и достигается наибольшая плотность.
Применение
Производство опилкобетонных блоков приобретает все большую популярность, потому что этот материал активно используется для возведения конструкций различного предназначения. Многие строительные компании предлагают проекты частных домов из опилкобетона. Кроме этого, используя такой стройматериал, получится соорудить коттедж, гараж, хозпостройку и даже забор. Опилкоблоки применяются для обустройства прочного и надежного фундамента, который после заливки еще долго не будет нуждаться в реставрации.
расчет пропорций материалов и компонентов для изготовления бетонно-стружечных плит, строительство домов из блоков из стружки и бетона

Постоянный рост стоимости традиционных стройматериалов нередко вынуждает искать менее дорогую альтернативу, обладающую хорошими эксплуатационными данными.
Такой альтернативой может стать стружкобетон – один из видов легких бетонов, в котором помимо цемента и песка присутствует древесная стружка.
В этой статье мы расскажем об:
- отличиях стружкобетона от арболита и опилкобетона;
- преимуществах и недостатках этого материала;
- наиболее частых ошибках, которые приводят к ухудшению его эксплуатационных качеств;
- правильных пропорциях компонентов;
- особенностях изготовления и применения.
Отличия от арболита и опилкобетона
Несмотря на то, что в основе каждого материала лежат отходы обработки древесины, их свойства сильно отличаются.
Арболит – легкий, но не очень прочный материал, который подходит либо для утепления, либо для создания одноэтажных домов. К тому же он дает очень сильную усадку, поэтому с ним тяжело работать.
Опилкобетон – более прочный и тяжелый материал, поэтому подходит для возведения даже двухэтажных домов. Благодаря добавлению песка он более стабилен в плане усадки, поэтому его можно использовать не только для создания деревянных бетонных плит, но и для монолитной заливки стен.
Его минус — недостаточная прочность на изгиб из-за отсутствия нормального армирования. Если же в блок или стену из опилкобетона вставляют арматуру, то она резко снижает теплоизоляционные свойства материала.
Стружкобетон во многом схож с опилкобетоном, но обладает более высокой прочностью на изгиб, ведь стружка длинней опилки, поэтому и лучше связывает бетон даже без применения арматуры.
Как и предыдущие материалы, стружкобетон можно использовать для утепления и создания несущих малоэтажных конструкций.
При соблюдении технологии и правильных пропорциях прочность стружкобетона может достигать значения М20, что недоступно арболиту и теоретически достаточно для возведения двухэтажного дома с деревянным перекрытием.
При этом все три материала подпадают под действие ГОСТ Р 54854— 2011 «Бетоны легкие на органических заполнителях растительного происхождения», с которым вы можете ознакомиться тут.
Есть еще один документ, который распространяется на бетоны, содержащие древесные отходы. Это ГОСТ 25192-2012 «Бетоны. Классификация и общие технические требования», который вы найдете тут. По этому документу к нормальным бетонам относят лишь арболит, ведь в нем роль заполнителя играет древесная стружка, не обеспечивающая достаточной прочности.
Поэтому опилкобетон и стружкбетон являются попыткой совместить преимущества традиционного бетона и древесины.
Однако, как и всякий гибрид, эти материалы взяли не только положительные, но и отрицательные качества.
Поэтому их использование оправдано лишь в том случае, если есть доступ к бесплатной стружке.
В этом случае вы получаете посредственный по несущей способности материал и заметно экономите на заполнителе. Если же стружку приходится покупать хотя бы по цене песка, то дешевле возвести стены из традиционного бетона и утеплить пенопластом.
Применение бетонно-стружечных плит
Из-за невысокой прочности на сдавливание этот материал не применяют для создания несущих стен многоэтажных домов. Даже двухэтажное строительство допустимо лишь с деревянными перекрытиями, да и то, материал будет обладать низкими теплоизоляционными свойствами.
Тем не менее, этот материал применяют для:
- создания стен малоэтажных зданий с малой нагрузкой;
- утепления;
- заполнения пространства между железобетонными несущими колоннами.
Создание стен малоэтажных зданий
Несмотря на то, что ГОСТ Р 54854— 2011 не допускает использования стружкобетона для строительства жилых зданий, дома из него стоят уже много десятилетий, а для строительства хозпостроек его применяют с середины прошлого века.
Такого срока достаточно, чтобы сделать вывод о том, что при:
- правильном подборе компонентов;
- грамотном составлении проекта;
- правильно подобранной отделке;
- соблюдении технологии,
дома высотой 1–2 этажа получаются довольно прочными и теплыми.
Однако такие дома желательно ставить лишь в регионах со:
- стабильным климатом;
- небольшим количеством осадков;
- небольшими перепадами суточных температур.
Нарушение любого из этих пунктов сокращает срок службы стен. Нестабильный климат, равно как и обильные осадки означают резкие перепады влажности воздуха, а значит и влажности древесины в составе стружкобетона.
Изменение размеров стружки, вызванное изменением влажности, приводит к изменению размеров древесных отходов. Когда древесина наполняется водой и увеличивается в размерах, она легко разрушает цементный камень, что приводит к ослаблению стружкобетона.
Тем не менее, даже в регионах, не соответствующих этим требованиям, дома из стружкобетона показали себя довольно хорошо. Однако это было достигнуто ценой падения паропроницаемости.
Для этого в состав бетона добавляют жидкое стекло и другие гидрофобные присадки, препятствующие впитыванию воды древесиной, благодаря чему сокращается амплитуда изменений, вызванная влажностным набуханием и усушкой древесины.
Утепление
Для утепления используют материал с минимальным содержанием цемента и песка, кроме того, он не испытывает тех нагрузок, которые переносят блоки из деревянной стружки и бетона в несущих стенах.
Поэтому небольшое снижение прочности, вызванное разбуханием и усушкой стружки, не влияет на теплоизоляционную способность.
Такой утеплитель нельзя оставлять открытым, потому что он сильно впитывает влагу не только от дождей, но и из воздуха.
Добавление жидкого стекла не влияет на теплоизоляционные свойства, но снижает способность стружкобетона транспортировать влагу от стен к атмосфере, низводя его по этому параметру до уровня глиняного кирпича.
Для утепления стен стружкобетоном используют те же методы, что применимы для утеплителей на основе опилок, поэтому мы рекомендуем внимательно прочитать эту статью. Добавление в готовый к заливке бетон небольшого количества глины делает застывший утеплитель менее чувствительным к изменению влажности стружки.
Заполнение пространства между железобетонными колоннами
В каркасных домах с железобетонными колоннами для зашивки пространства между колоннами используют разные виды легких бетонов, в том числе стружкобетон. По теплоизолирующим способностям при равной плотности его превосходит только полистиролбетон, а остальные виды легких бетонов аналогичны или уступают стружкобетону.
При плотности 500–700 кг/м3 прочности стружкобетона достаточно для заполнения пространства между несущими колоннами и создания ненесущих стен.
Однако даже в теплых регионах такие дома нуждаются в утеплении, ведь теплопроводность железобетона очень высока, поэтому без утепления на месте несущих колонн появятся мосты холода.
Расчет необходимых материалов для приготовления блоков из стружки и бетона
Для получения качественного бетона важно соблюсти не только пропорции исходных компонентов, но и весь порядок действий, в противном случае прочность материала окажется ниже ожидаемой. Также нарушение порядка действий приведет к увеличению способности впитывать воду, из-за чего сократится срок службы бетонной конструкции.
Вот порядок действий, который применим для приготовления стружкобетона любого назначения:
- Подготовить формы для заливки блоков. Мы рассказывали о том, как это сделать, в этой статье.
- Растворить в воде свежегашеную известь (1 кг на 20 л воды) и замочить в этом молоке стружку. Мелкую стружку (толщина 0,1 мм и меньше) замачивать сутки, среднюю (толщина свыше 0,2 мм) — 48 часов, крупную (толщина 0,4 и больше) — 72 часа.
- В бетономешалке смешать цемент, песок и негашеную известь в нужных пропорциях.
- Стружку выловить из емкости с известковым молоком и дать стечь 10–15 минут, после чего высыпать нужное количество в бетономешалку и тщательно перемешать.
- Подготовить воду, для этого добавить в нее суперпластификатор в количестве ¼ от рекомендованного в инструкции к нему. Также нужно добавить гидрофобные присадки, например, Силоксил (инструкция по использованию на упаковке). Если вы делаете утепляющий бетон, то добавьте также пену древесной омыленной смолы или другую воздухововлекающую присадку (потребуется пеногенератор). При этом действуйте строго по инструкции на упаковке с реагентом.
- Добавить нужное количество воды (учитывайте влажность песка и известковое молоко в стружке, поэтому сократите количество воды на 2–5%) и тщательно перемешайте.
- Распределите бетон по формам.
- Если не успели выработать весь бетон за 5 минут, то перемешайте еще раз.
Вот расчет материалов для изготовления бетонно-стружечных плит различного назначения:
Количество компонентов в кг (для воды в литрах) | |||||
Назначение | Цемент | Песок | Известь | Стружка | Вода |
Утепляющий | 10 (М400) | 2 | 8 | 100 | 3 |
Утепляющий и для ненесущих стен нежилых строений | 10 (М400) | 10 | 10 | 100 | 3 |
Несущие стены нежилых конструкций или ненесущие стены жилых | 20 (М500) | 50 | 20 | 100 | 9,5 |
Несущие стены жилых одноэтажных домов | 40 (М500) | 100 | 50 | 100 | 20 |
Несущие стены двухэтажных домов | 40 (М500) | 100 | 50 | 50 | 19 |
Частые ошибки при изготовлении
Негативные отзывы о стружкобетоне, которые можно встретить в интернете, чаще всего связаны с ошибками, допущенными во время приготовления или использования этого материала.
Далее расскажем о наиболее частых из них.
Игнорирование суперпластификаторов и гидрофобных присадок
Достаточно часто пользователи игнорируют и не используют суперпластификаторы.
Эти вещества снижают количество воды, необходимое для создания раствора нужной вязкости, благодаря чему возрастает прочность застывшего бетона.
Добавление суперпластификаторов желательно при заливке блоков, ведь это увеличивает их прочность, и необходимо при монолитной заливке стен.
Бетон с этой присадкой более пластичный и легче заполняет опалубку при том же количестве воды.
Из-за игнорирования гидрофобных присадок увеличивается количество влаги, которая поступает к древесине, поэтому даже заполнение пор минералами не может сократить впитывание воды до безопасного уровня. Часто от присадок отказываются, потому что боятся снижения паропроницаемости, но они не влияют на этот параметр.
Пар движется по частицам цементного камня с очень маленькой скоростью, поэтому паропроницаемость стружкобетона всегда ниже этого параметра древесины и находится на одном уровне с кирпичом или бетоном. Добавление гидрофобных присадок снижает паропроницаемость на 2–5%, поэтому никакого серьезного влияния не оказывает.
Выбор стружки и пренебрежение ее замачиванием
Распространенным упущением также является неправильный выбор вида стружки. Ошибочно использование стружки «сладких» пород древесины. К таким породам относят березу, клен, иву, ольху, плодовые деревья.
Древесина этих пород пропитана различными сахарами и глюкозой, которые нарушают химическую реакцию, приводящую к образованию цементного камня.
Известь частично нейтрализует негативное воздействие сахаров, но в сладких породах глюкозы слишком много. Зато в хвойных породах сахаров мало и известь почти полностью блокирует этот негативный эффект.
Кроме того, стружку предварительно не замачивают в известковом молоке. Эту операцию выполняют не для обеззараживания древесных отходов, ее цель – заполнение пор минералами, благодаря чему снижается способность древесины впитывать воду, а значит, возрастает:
- прочность бетона;
- несущая способность;
- срок службы.
Песок и вода
Ошибкой также является использование гладкого мелкого песка. Чем крупней песок и неровней форма каждой песчинки, тем тяжелей с ним работать, но и тем выше прочность бетона.
Ведь с гладкого песка цементное молоко быстро сползает, тогда как на неровной поверхности оно задерживается до застывания.
А увеличение количества воды делает бетон более удобным в работе, но ослабляет цементный камень, в результате чего падает прочность блока или стены.
Пренебрежение пеной на основе древесной омыленной смолы
Для утепляющих плит снижение теплопроводности цементного камня важней некоторой потери прочности из-за превращения цементного камня в аналог губки, ведь эти плиты не используют в качестве несущих элементов.
Добавление пены и других реагентов увеличивает теплоизоляционные свойства плиты на 5–15%, что приближает ее по теплоэффективности к минеральной вате и пенопласту.
Некачественная наружная отделка
Очень важно не забывать о качественной внешней отделке стружкобетона. Добавление гидрофобных присадок и заполнение каналов минералами снижает чувствительность древесины к водяному пару, однако контакт с водой дает слишком много влаги, которая пропитывает бетон и вызывает расширение древесных отходов.
Особенно опасна такая ситуация поздней осенью, ведь стружка не успевает отдать избыток влаги до наступления морозов, в результате чего к расширению от воды прибавляется и расширение от замерзания.
При переходе из жидкого в твердое состояние объем воды увеличивается на 11%, поэтому чем выше влажность перед наступлением морозов, тем сильней будет удар по цементному камню во время замерзания воды внутри древесины.
Другие варианты бетонных панелей
Помимо традиционного бетона на цементном вяжущем, из стружки делают и другие виды бетонов:
- гипсовый;
- глиняный;
- известковый.
Однако их несущая способность гораздо ниже той, которую обеспечивает использование цемента. Поэтому альтернативные виды стружкобетона применяют только в качестве утепляющего материала. Еще одно их отличие в отсутствии песка, ведь песок увеличивает прочность цементного камня, но мало влияет на остальные типы вяжущих веществ.
Кроме того, альтернативные виды стружкобетона отличаются высокой чувствительностью к влаге и воде, поэтому их можно применять либо внутри помещений (утепление полов и потолков), либо закрывать очень качественной отделкой, максимально защищающей от осадков.
Вывод
Стружкобетон – хороший материал для малоэтажного строительства и возведения подсобных помещений, ведь он сочетает в себе неплохую несущую способность и высокие теплоизоляционные свойства.
Если есть все необходимое оборудование и доступ к бесплатным опилкам, то стружкобетон обходится дешевле других видов легкого бетона. Однако при его изготовлении и применении очень важно соблюдать не только пропорции основных компонентов, но порядок действий.
Одно из важнейших преимуществ этого материала в том, что для его изготовления применяют отходы обработки древесины, на которые не всегда можно найти покупателя. Поэтому изготовление стружкобетона избавляет деревообрабатывающее предприятие от скопившихся отходов и обеспечивает хорошим строительным материалом.
Вконтакте
Google+
Одноклассники
технология изготовления (фото и видео)
Изготовление блоков из опилок и цемента позволит сэкономить семейный бюджет и сделать экологически чистый строительный материал своими руками. Но перед началом работы необходимо обзавестись всем необходимым и тщательно изучить технологию производства, которая имеет свои нюансы.

Разновидности строительных блоков.
Подготовка материала для арболитовых блоков
Строительные арболитовые блоки изготавливают на основе щепы и опилок хвойных пород древесины, которые соединяют с цементом и водой, подмешивают различные органические наполнители и химические реагенты. Перед тем как начать изготавливать блоки своими руками, необходимо подготовить сырье. Древесные щепы и опилки берут поровну или в соотношении 1:2.
Хвойные породы содержат сахар, от которого необходимо избавиться, иначе древесина может загнить, что приведет к вздуванию готовых блоков.

Характеристики арболитовых блоков.
Для того чтобы получить хороший строительный материал, необходимо использовать только качественное сырье, например, портландцемент марки М-400. Не менее важно хорошо перемешать массу для изготовления блоков, вручную это вряд ли удастся, поэтому без портативной бетономешалки вам не обойтись. В качестве добавок нередко используют гашеную известь, сернокислый алюминий, жидкое стекло, сернокислый и хлористый кальций. Количество добавок в составе смеси колеблется от 2 до 4% от массы цемента, превышать эти пропорции не рекомендуется, так как это повлияет на качество готового изделия.
Вернуться к оглавлению
Как изготовить опилкобетонные блоки своими руками?
Понадобятся:
- деревянные доски для формы;
- древесная щепа и опилки;
- строительное сито;
- портландцемент;
- жидкое стекло.
Перед тем как приступить к изготовлению блоков, необходимо смастерить отливочную форму. Для этой цели используют деревянные брусья, форма состоит из прямоугольной рамы и поддона. Сначала сбивают некое подобие ящика, ширина которого равняется 30 см, длина — 60 см, высота — 24 см. Углы закрепляют при помощи специальных уголков и саморезов, форма должна быть устойчивой и прочной, не перекашиваться и не шататься во время заполнения раствора. По бокам необходимо прибить бруски, которые будут использоваться в качестве ручек. Для изготовления поддона сбивают раму из брусков, набивают на нее ровные доски.
Для того чтобы предотвратить налипание раствора на стенки формы, необходимо обклеить раму и поддон линолеумом.

Схема формы для арболитовых блоков.
Для изготовления арболитовых блоков используют щепки следующей фракции: длиной — от 3 до 15 см, шириной — от 5 мм до 2 см. Для получения сырья на мелких производствах используют различную технику.
Сначала щепки пропускают через рубильную машину, после чего получившееся сырье обрабатывают на молотковой дробилке, далее применяют грохот для сортировки щепы и отсеивания пыли, коры, земли, которые не должны попасть в состав готовых блоков.
Но далеко не у всех имеется такая техника в хозяйстве, поэтому необходимо заранее позаботиться о приобретении готового сырья, например, договориться о покупке опилок на лесопилке. Иногда к опилкам подмешивают льняные и конопляные волокна, оставшиеся от переработки этих материалов на производстве.
Сырье поливают окисью кальция, выдерживают на улице 3-4 дня, перелопачивая время от времени. После чего стружку и опилки пропускают через строительное сито, избавляясь таким образом от ненужных примесей. Перед тем как начать производство блоков, сырье замачивают в воде с добавлением жидкого стекла и других добавок. Для придания дополнительной твердости используют хлористый кальций, гашеная известь выступает в роли дезинфицирующего материала.
Подготовленную смесь смешивают с портландцементом, для перемешивания в домашних условиях используют портативную бетономешалку. Пропорции раствора зависят от того, какую прочность планируется придать готовому изделию. Специалисты рекомендуют на 1 часть цемента брать 6 частей древесной щепы и опилок, 2 части песка. Некоторые мастера для удешевления материала часть цемента заменяют глиной и известью. Допускается наличие сосновой хвои и коры, но их состав не должен превышать 5% от общей массы сырья.
Перед началом заливки форму смазывают солидолом или промышленным маслом: это предотвратит налипание раствора и поможет беспрепятственно извлечь готовый блок. Раствор заливают в форму, встряхивают ее, затем тщательно утрамбовывают. В качестве трамбовки используют доску, обитую железом. При ручном производстве рекомендуется послойная трамбовка, при которой форма заполняется раствором постепенно. На предприятиях для данной цели используют вибропресс, пневматические или электрические трамбовки.
Блоки оставляют в форме на 24 часа, после чего их извлекают, накрывают полиэтиленовой пленкой, отправляют на доводку под навес. Для того чтобы не допустить пересыхания материала, время от времени блоки увлажняют водой. Сохнет арболит в течение 10-14 дней (при условии плюсовой температуры). Используя рекомендации специалистов, изложенные выше, вы с легкостью сможете изготовить арболитовые блоки своими руками.