как сделать щепорез своими руками по чертежу? Выбор древесной дробилки для производства арболитовой щепы
Арболит как строительный материал был запатентован еще в первой половине XX века. В нашей стране широко применяться он стал в последние годы.
Арболит или деревобетон (щепобетон) выпускается в виде блоков. Используется для возведения малоэтажных строений. Как следует из названия, в качестве наполнителя выступает древесная щепа. В ход идут отходы деревьев хвойных и лиственных пород.
Арболит относится к недорогим строительным материалам, отличающимся высокой экологичностью, малым весом блоков, отличной способностью удерживать тепло. Древесные отходы в составе смеси деревобетона составляют более трех четвертей – от 75 до 90 процентов.
Что это такое?

- топлива для печей – в чистом виде или в виде гранул;
- декора – дизайнеры предлагают его в окрашенном и естественном виде для оформления дачных участков и даже парков;
- составляющей для изготовления и украшения мебели;
- ингредиента, используемого при копчении различных продуктов питания.
В производстве мелкие фракции идут на изготовление других стройматериалов: картона, гипсокартона, ДСП и ДВП.
Из чего делают?
Для производства щепобетона подходит практически любая древесина. И все же предпочтительно использование хвойных пород, к примеру, ели или сосны. Из лиственных более качественная щепа получается из березы. Подходят и другие твердолиственные породы: осина, дуб и тополь.
При выборе древесины для арболита нужно знать ее состав. Так, лиственница не подходит для данного строительного материала из-за высокого содержания веществ, негативно влияющих на цемент. Ядом для цемента являются сахара. Кроме лиственницы, они в большом количестве имеются в древесине бука. Следовательно, отходы этого дерева использовать тоже нельзя.
Очень важный момент – срок рубки леса.
Щепу нельзя делать сразу после вырубки. Материал должен вылежаться в течение трех – четырех месяцев.
- ветки и сучки;
- верхушки деревьев;
- горбыль;
- остатки и обломки;
- вторичные отходы.
Допускается наличие в общей массе древесины для производства щепы хвои и листьев – не более 5%, а коры – не более 10%.
Наиболее часто щепу изготавливают из елей и сосен.
Какой должна быть щепа?
Выделены три основных параметра:
- длина не больше 30 мм;
- ширина не больше 10 мм;
- толщина не больше 5 мм.
Обозначены и оптимальные размеры по ширине и длине:
- длина – 20 мм;
- ширина – 5 мм.
Новые требования появились с принятием ГОСТ 54854-2011. До этого существовал другой ГОСТ с меньшими требованиями. Тогда допускалось использование более длинной щепы – вплоть до 40 мм. В 2018 году «вольности» в размерах наполнителя не допускаются.
Стандарт регламентирует и наличие примесей: коры, листьев, хвои. Материал следует очищать от земли, песка, глины, а в зимнее время – от снега. Наличие плесени и загниваний недопустимо.
Выбор оборудования для изготовления
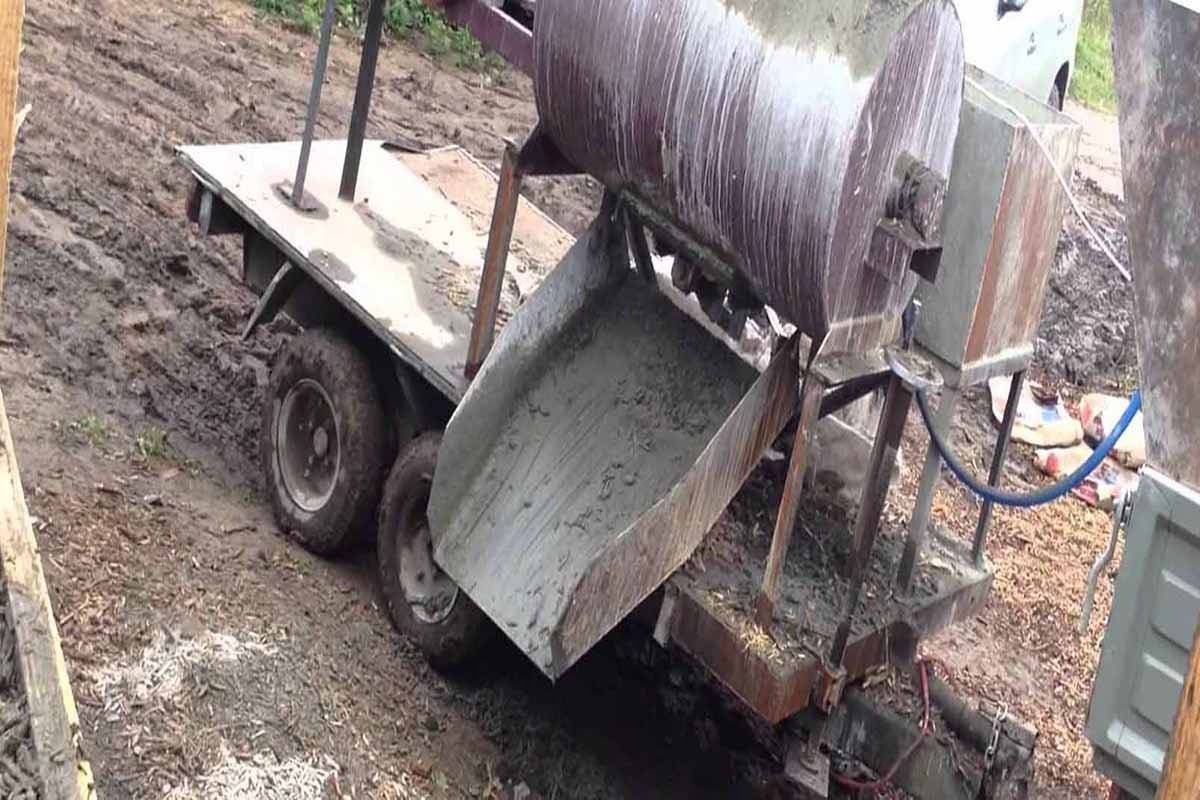
Арболит вполне возможно изготавливать в домашних условиях. Для этого и щепу нужно делать самостоятельно. Измельчителем древесины в условиях подсобного хозяйства становится щеподробильный станок. Щепорезы бывают трех типов.
- Дисковые рубильные машины обрабатывают древесину различной формы. За счет регулировки наклона режущего инструмента можно получать заготовки требуемого размера.
- В барабанных щепорезах измельчают всевозможные отходы: лесозаготовительные, мебельного производства, обрезков после строительства. Сырье загружают в объемный бункер, откуда оно попадает в камеру и разрезается ножами с двусторонними лезвиями.
- Роторные дробилки молоткового типа выпускаются с двумя или одним валом. Основные элементы устройства – молотки и отбойники.
Во всех перечисленных устройствах предусмотрена только ручная загрузка материала.
Принцип производства
Принцип работы щепорезов сводится к нескольким этапам.
Сначала отходы – доски, горбыль, обрезки, сучки и другое сырье – закладываются в загрузочный бункер. Оттуда все это подается в закрытую камеру, где на валу вращается мощный диск. На плоском диске имеются прорези. На нем, кроме того, закреплены несколько ножей. Ножи движутся под углом. За счет этого обрабатываемая древесина разделяется на небольшие пластины с косым резом.
Сквозь дисковые прорези пластины проникают в барабан, где стальные пальцы производят дальнейшее измельчение. Пальцы и пластины крепятся на том же валу, что и диск. Пластины установлены очень близко к барабану. Они перемещают размолотую щепу по внутренней поверхности барабана.
Нижняя часть барабана снабжена сеткой с ячейками, обеспечивающими заданные размеры щепы. Размер ячейки варьируется от 10 до 15 мм в диаметре. Как только готовая к использованию щепа попадает в нижнюю зону в вертикальном направлении, она проходит сквозь сетку в поддон. Оставшиеся частицы проворачиваются, удерживаемые пластинами, еще круг. В это время их положение постоянно меняется. Достигнув низа в нужном направлении, они также оказываются в поддоне.
Щепорезы могут иметь как электрический, так и бензиновый приводы. Мощность двигателя небольшого устройства находится в пределах четырех – шести киловатт, в более солидных доходит до 10-15 кВт. От мощности зависят способности устройства. С ее увеличением растет объем продукции за час работы механизма.
Как сделать щепорез своими руками?
Тем, кто захочет сделать собственный щепорез, потребуется чертеж устройства, материалы, определенные знания и навыки. Чертеж можно найти в интернете, к примеру, тот, что прилагается.
Узлы и детали придется делать и собирать самостоятельно.
Один из основных элементов механизма – диск диаметром порядка 350 мм и толщиной примерно 20 мм. Если ничего подходящего в хозяйстве не имеется, придется вытачивать из листа. Для посадки на вал потребуется сделать хорошо центрированное отверстие с пазом под шпонку. Кроме того, нужно будет выпилить три паза, сквозь которые древесина станет попадать под молотки, и нужное количество монтажных отверстий.
Несколько проще обстоят дела с ножами. Их делают из автомобильных рессор. На ножах просверливаются по два отверстия под крепеж. Кроме сверла, потребуется зенкер. Зенковка позволит утопить потайные головки крепежных деталей. Плотно прикрепить ножи к диску не составит труда любому взрослому мужчине.
Молотки представляют собою обычные стальные пластины, имеющие толщину около 5 мм. Крепятся они на роторе с шагом 24 мм. Купить молотки можно в магазине.
Сито для щепореза – это длинный (около 1100 мм) цилиндр (Д= 350 мм), свернутый и сваренный из листа. Примечательно, что отверстия в сите должны иметь не ровные, а рваные края. Поэтому их не высверливают, а вырубают, к примеру, пробойником с диаметром от 8 до 12 мм.
Все режущие и вращающиеся детали должны закрываться кожухом. Кожух, как и приемный бункер, изготавливают из листовой стали. Отдельные детали вырезают по картонным шаблонам и сваривают в единое целое. Для жесткости конструкции к листам приваривают ребра жесткости из труб или уголков. В корпусе следует предусмотреть все отверстия: для вала, загрузочного бункера и для выхода щепы.
Готовые детали собираются в механизм. На рабочий вал насаживается диск, молотки и подшипники. Вся конструкция закрывается кожухом. Диск ни в коем случае не должен касаться корпуса. Зазор должен составлять порядка 30 мм.
Привод монтируется на заключительном этапе. Самодельный щепорез может работать от электродвигателя напряжением 220 или 380 В. Допускается работа от бензинового или дизельного мотора.
Электродвигатели обладают небольшой мощностью, зато малошумные и более экологичные. Двигатели внутреннего сгорания более производительны, но их работа сопровождается выделением вредных выхлопных газов.
Самодельные щепорезы выгодны при изготовлении арболита для частного строительства.
О том, как сделать щепорез своими руками, смотрите в следующем видео.
как сделать щепорез своими руками по чертежу? Выбор древесной дробилки для производства арболитовой щепы
Арболит как строительный материал был запатентован еще в первой половине XX века. В нашей стране широко применяться он стал в последние годы.
Арболит или деревобетон (щепобетон) выпускается в виде блоков. Используется для возведения малоэтажных строений. Как следует из названия, в качестве наполнителя выступает древесная щепа. В ход идут отходы деревьев хвойных и лиственных пород.
Арболит относится к недорогим строительным материалам, отличающимся высокой экологичностью, малым весом блоков, отличной способностью удерживать тепло. Древесные отходы в составе смеси деревобетона составляют более трех четвертей – от 75 до 90 процентов.
Что это такое?
Отходы деревообработки являются ценным строительным материалом. После измельчения до определенных размеров они становятся наполнителем бетонных смесей. Используется щепа для арболита или как его именуют щепобетона. Арболитовые блоки имеют массу достоинств. Доступная стоимость играет немалую роль. Кроме того, дом, построенный из арболита, практически не требует дополнительного утепления.
Есть у щепы и иные достоинства. Материал пригоден для использования в качестве:
- топлива для печей – в чистом виде или в виде гранул;
- декора – дизайнеры предлагают его в окрашенном и естественном виде для оформления дачных участков и даже парков;
- составляющей для изготовления и украшения мебели;
- ингредиента, используемого при копчении различных продуктов питания.
В производстве мелкие фракции идут на изготовление других стройматериалов: картона, гипсокартона, ДСП и ДВП.
Из чего делают?
Для производства щепобетона подходит практически любая древесина. И все же предпочтительно использование хвойных пород, к примеру, ели или сосны. Из лиственных более качественная щепа получается из березы. Подходят и другие твердолиственные породы: осина, дуб и тополь.
При выборе древесины для арболита нужно знать ее состав. Так, лиственница не подходит для данного строительного материала из-за высокого содержания веществ, негативно влияющих на цемент. Ядом для цемента являются сахара. Кроме лиственницы, они в большом количестве имеются в древесине бука. Следовательно, отходы этого дерева использовать тоже нельзя.
Очень важный момент – срок рубки леса. Щепу нельзя делать сразу после вырубки. Материал должен вылежаться в течение трех – четырех месяцев.
Практически все отходы могут стать исходниками для изготовления щепы.
- ветки и сучки;
- верхушки деревьев;
- горбыль;
- остатки и обломки;
- вторичные отходы.
Допускается наличие в общей массе древесины для производства щепы хвои и листьев – не более 5%, а коры – не более 10%.
Наиболее часто щепу изготавливают из елей и сосен. Выбор в пользу хвои неслучаен. Дело в том, что любая древесина содержит в себе такие вещества, как крахмал, сахара и прочие вещества, способные существенно повлиять на снижение качества арболита. В процессе производства приходится выводить вредные составляющие. Поскольку в хвое их меньше, именно на эти породы приходится меньше усилий, времени и материальных затрат на подготовку щепы.
Какой должна быть щепа?
Древесный наполнитель для арболита имеет свой ГОСТ. На уровне государственного стандарта для щепы установлены жесткие требования.
Выделены три основных параметра:
- длина не больше 30 мм;
- ширина не больше 10 мм;
- толщина не больше 5 мм.
Обозначены и оптимальные размеры по ширине и длине:
- длина – 20 мм;
- ширина – 5 мм.
Новые требования появились с принятием ГОСТ 54854-2011. До этого существовал другой ГОСТ с меньшими требованиями. Тогда допускалось использование более длинной щепы – вплоть до 40 мм. В 2018 году «вольности» в размерах наполнителя не допускаются.
Стандарт регламентирует и наличие примесей: коры, листьев, хвои. Материал следует очищать от земли, песка, глины, а в зимнее время – от снега. Наличие плесени и загниваний недопустимо.
Выбор оборудования для изготовления
Наиболее подходящим оборудованием для получения щепы требуемой формы и размеров является специальный деревообрабатывающий шредер. Однако стоимость станка настолько высока, что вне производства приходится искать другие варианты.
Арболит вполне возможно изготавливать в домашних условиях. Для этого и щепу нужно делать самостоятельно. Измельчителем древесины в условиях подсобного хозяйства становится щеподробильный станок. Щепорезы бывают трех типов.
- Дисковые рубильные машины обрабатывают древесину различной формы. За счет регулировки наклона режущего инструмента можно получать заготовки требуемого размера.
- В барабанных щепорезах измельчают всевозможные отходы: лесозаготовительные, мебельного производства, обрезков после строительства. Сырье загружают в объемный бункер, откуда оно попадает в камеру и разрезается ножами с двусторонними лезвиями.
- Роторные дробилки молоткового типа выпускаются с двумя или одним валом. Основные элементы устройства – молотки и отбойники.
Сначала древесина измельчается ударным способом, затем готовая продукция просеивается сквозь сито. От величины ячеек сита зависит размер получаемой щепы.
Во всех перечисленных устройствах предусмотрена только ручная загрузка материала.
Принцип производства
Принцип работы щепорезов сводится к нескольким этапам.
Сначала отходы – доски, горбыль, обрезки, сучки и другое сырье – закладываются в загрузочный бункер. Оттуда все это подается в закрытую камеру, где на валу вращается мощный диск. На плоском диске имеются прорези. На нем, кроме того, закреплены несколько ножей. Ножи движутся под углом. За счет этого обрабатываемая древесина разделяется на небольшие пластины с косым резом.
Сквозь дисковые прорези пластины проникают в барабан, где стальные пальцы производят дальнейшее измельчение. Пальцы и пластины крепятся на том же валу, что и диск. Пластины установлены очень близко к барабану. Они перемещают размолотую щепу по внутренней поверхности барабана.
Нижняя часть барабана снабжена сеткой с ячейками, обеспечивающими заданные размеры щепы. Размер ячейки варьируется от 10 до 15 мм в диаметре. Как только готовая к использованию щепа попадает в нижнюю зону в вертикальном направлении, она проходит сквозь сетку в поддон. Оставшиеся частицы проворачиваются, удерживаемые пластинами, еще круг. В это время их положение постоянно меняется. Достигнув низа в нужном направлении, они также оказываются в поддоне.
Щепорезы могут иметь как электрический, так и бензиновый приводы. Мощность двигателя небольшого устройства находится в пределах четырех – шести киловатт, в более солидных доходит до 10-15 кВт. От мощности зависят способности устройства. С ее увеличением растет объем продукции за час работы механизма.
Как сделать щепорез своими руками?
Тем, кто захочет сделать собственный щепорез, потребуется чертеж устройства, материалы, определенные знания и навыки. Чертеж можно найти в интернете, к примеру, тот, что прилагается.
Узлы и детали придется делать и собирать самостоятельно.
Один из основных элементов механизма – диск диаметром порядка 350 мм и толщиной примерно 20 мм. Если ничего подходящего в хозяйстве не имеется, придется вытачивать из листа. Для посадки на вал потребуется сделать хорошо центрированное отверстие с пазом под шпонку. Кроме того, нужно будет выпилить три паза, сквозь которые древесина станет попадать под молотки, и нужное количество монтажных отверстий.
Несколько проще обстоят дела с ножами. Их делают из автомобильных рессор. На ножах просверливаются по два отверстия под крепеж. Кроме сверла, потребуется зенкер. Зенковка позволит утопить потайные головки крепежных деталей. Плотно прикрепить ножи к диску не составит труда любому взрослому мужчине.
Молотки представляют собою обычные стальные пластины, имеющие толщину около 5 мм. Крепятся они на роторе с шагом 24 мм. Купить молотки можно в магазине.
Сито для щепореза – это длинный (около 1100 мм) цилиндр (Д= 350 мм), свернутый и сваренный из листа. Примечательно, что отверстия в сите должны иметь не ровные, а рваные края. Поэтому их не высверливают, а вырубают, к примеру, пробойником с диаметром от 8 до 12 мм.
Все режущие и вращающиеся детали должны закрываться кожухом. Кожух, как и приемный бункер, изготавливают из листовой стали. Отдельные детали вырезают по картонным шаблонам и сваривают в единое целое. Для жесткости конструкции к листам приваривают ребра жесткости из труб или уголков. В корпусе следует предусмотреть все отверстия: для вала, загрузочного бункера и для выхода щепы.
Готовые детали собираются в механизм. На рабочий вал насаживается диск, молотки и подшипники. Вся конструкция закрывается кожухом. Диск ни в коем случае не должен касаться корпуса. Зазор должен составлять порядка 30 мм.
Привод монтируется на заключительном этапе. Самодельный щепорез может работать от электродвигателя напряжением 220 или 380 В. Допускается работа от бензинового или дизельного мотора.
Электродвигатели обладают небольшой мощностью, зато малошумные и более экологичные. Двигатели внутреннего сгорания более производительны, но их работа сопровождается выделением вредных выхлопных газов.
Самодельные щепорезы выгодны при изготовлении арболита для частного строительства.
О том, как сделать щепорез своими руками, смотрите в следующем видео.
как сделать щепорез своими руками по чертежу? Выбор древесной дробилки для производства арболитовой щепы
Арболит как строительный материал был запатентован еще в первой половине XX века. В нашей стране широко применяться он стал в последние годы.
Арболит или деревобетон (щепобетон) выпускается в виде блоков. Используется для возведения малоэтажных строений. Как следует из названия, в качестве наполнителя выступает древесная щепа. В ход идут отходы деревьев хвойных и лиственных пород.
Арболит относится к недорогим строительным материалам, отличающимся высокой экологичностью, малым весом блоков, отличной способностью удерживать тепло. Древесные отходы в составе смеси деревобетона составляют более трех четвертей – от 75 до 90 процентов.
Что это такое?
Отходы деревообработки являются ценным строительным материалом. После измельчения до определенных размеров они становятся наполнителем бетонных смесей. Используется щепа для арболита или как его именуют щепобетона. Арболитовые блоки имеют массу достоинств. Доступная стоимость играет немалую роль. Кроме того, дом, построенный из арболита, практически не требует дополнительного утепления.
Есть у щепы и иные достоинства. Материал пригоден для использования в качестве:
- топлива для печей – в чистом виде или в виде гранул;
- декора – дизайнеры предлагают его в окрашенном и естественном виде для оформления дачных участков и даже парков;
- составляющей для изготовления и украшения мебели;
- ингредиента, используемого при копчении различных продуктов питания.
В производстве мелкие фракции идут на изготовление других стройматериалов: картона, гипсокартона, ДСП и ДВП.
Из чего делают?
Для производства щепобетона подходит практически любая древесина. И все же предпочтительно использование хвойных пород, к примеру, ели или сосны. Из лиственных более качественная щепа получается из березы. Подходят и другие твердолиственные породы: осина, дуб и тополь.
При выборе древесины для арболита нужно знать ее состав. Так, лиственница не подходит для данного строительного материала из-за высокого содержания веществ, негативно влияющих на цемент. Ядом для цемента являются сахара. Кроме лиственницы, они в большом количестве имеются в древесине бука. Следовательно, отходы этого дерева использовать тоже нельзя.
Очень важный момент – срок рубки леса. Щепу нельзя делать сразу после вырубки. Материал должен вылежаться в течение трех – четырех месяцев.
Практически все отходы могут стать исходниками для изготовления щепы.
- ветки и сучки;
- верхушки деревьев;
- горбыль;
- остатки и обломки;
- вторичные отходы.
Допускается наличие в общей массе древесины для производства щепы хвои и листьев – не более 5%, а коры – не более 10%.
Наиболее часто щепу изготавливают из елей и сосен. Выбор в пользу хвои неслучаен. Дело в том, что любая древесина содержит в себе такие вещества, как крахмал, сахара и прочие вещества, способные существенно повлиять на снижение качества арболита. В процессе производства приходится выводить вредные составляющие. Поскольку в хвое их меньше, именно на эти породы приходится меньше усилий, времени и материальных затрат на подготовку щепы.
Какой должна быть щепа?
Древесный наполнитель для арболита имеет свой ГОСТ. На уровне государственного стандарта для щепы установлены жесткие требования.
Выделены три основных параметра:
- длина не больше 30 мм;
- ширина не больше 10 мм;
- толщина не больше 5 мм.
Обозначены и оптимальные размеры по ширине и длине:
- длина – 20 мм;
- ширина – 5 мм.
Новые требования появились с принятием ГОСТ 54854-2011. До этого существовал другой ГОСТ с меньшими требованиями. Тогда допускалось использование более длинной щепы – вплоть до 40 мм. В 2018 году «вольности» в размерах наполнителя не допускаются.
Стандарт регламентирует и наличие примесей: коры, листьев, хвои. Материал следует очищать от земли, песка, глины, а в зимнее время – от снега. Наличие плесени и загниваний недопустимо.
Выбор оборудования для изготовления
Наиболее подходящим оборудованием для получения щепы требуемой формы и размеров является специальный деревообрабатывающий шредер. Однако стоимость станка настолько высока, что вне производства приходится искать другие варианты.
Арболит вполне возможно изготавливать в домашних условиях. Для этого и щепу нужно делать самостоятельно. Измельчителем древесины в условиях подсобного хозяйства становится щеподробильный станок. Щепорезы бывают трех типов.
- Дисковые рубильные машины обрабатывают древесину различной формы. За счет регулировки наклона режущего инструмента можно получать заготовки требуемого размера.
- В барабанных щепорезах измельчают всевозможные отходы: лесозаготовительные, мебельного производства, обрезков после строительства. Сырье загружают в объемный бункер, откуда оно попадает в камеру и разрезается ножами с двусторонними лезвиями.
- Роторные дробилки молоткового типа выпускаются с двумя или одним валом. Основные элементы устройства – молотки и отбойники.
Сначала древесина измельчается ударным способом, затем готовая продукция просеивается сквозь сито. От величины ячеек сита зависит размер получаемой щепы.
Во всех перечисленных устройствах предусмотрена только ручная загрузка материала.
Принцип производства
Принцип работы щепорезов сводится к нескольким этапам.
Сначала отходы – доски, горбыль, обрезки, сучки и другое сырье – закладываются в загрузочный бункер. Оттуда все это подается в закрытую камеру, где на валу вращается мощный диск. На плоском диске имеются прорези. На нем, кроме того, закреплены несколько ножей. Ножи движутся под углом. За счет этого обрабатываемая древесина разделяется на небольшие пластины с косым резом.
Сквозь дисковые прорези пластины проникают в барабан, где стальные пальцы производят дальнейшее измельчение. Пальцы и пластины крепятся на том же валу, что и диск. Пластины установлены очень близко к барабану. Они перемещают размолотую щепу по внутренней поверхности барабана.
Нижняя часть барабана снабжена сеткой с ячейками, обеспечивающими заданные размеры щепы. Размер ячейки варьируется от 10 до 15 мм в диаметре. Как только готовая к использованию щепа попадает в нижнюю зону в вертикальном направлении, она проходит сквозь сетку в поддон. Оставшиеся частицы проворачиваются, удерживаемые пластинами, еще круг. В это время их положение постоянно меняется. Достигнув низа в нужном направлении, они также оказываются в поддоне.
Щепорезы могут иметь как электрический, так и бензиновый приводы. Мощность двигателя небольшого устройства находится в пределах четырех – шести киловатт, в более солидных доходит до 10-15 кВт. От мощности зависят способности устройства. С ее увеличением растет объем продукции за час работы механизма.
Как сделать щепорез своими руками?
Тем, кто захочет сделать собственный щепорез, потребуется чертеж устройства, материалы, определенные знания и навыки. Чертеж можно найти в интернете, к примеру, тот, что прилагается.
Узлы и детали придется делать и собирать самостоятельно.
Один из основных элементов механизма – диск диаметром порядка 350 мм и толщиной примерно 20 мм. Если ничего подходящего в хозяйстве не имеется, придется вытачивать из листа. Для посадки на вал потребуется сделать хорошо центрированное отверстие с пазом под шпонку. Кроме того, нужно будет выпилить три паза, сквозь которые древесина станет попадать под молотки, и нужное количество монтажных отверстий.
Несколько проще обстоят дела с ножами. Их делают из автомобильных рессор. На ножах просверливаются по два отверстия под крепеж. Кроме сверла, потребуется зенкер. Зенковка позволит утопить потайные головки крепежных деталей. Плотно прикрепить ножи к диску не составит труда любому взрослому мужчине.
Молотки представляют собою обычные стальные пластины, имеющие толщину около 5 мм. Крепятся они на роторе с шагом 24 мм. Купить молотки можно в магазине.
Сито для щепореза – это длинный (около 1100 мм) цилиндр (Д= 350 мм), свернутый и сваренный из листа. Примечательно, что отверстия в сите должны иметь не ровные, а рваные края. Поэтому их не высверливают, а вырубают, к примеру, пробойником с диаметром от 8 до 12 мм.
Все режущие и вращающиеся детали должны закрываться кожухом. Кожух, как и приемный бункер, изготавливают из листовой стали. Отдельные детали вырезают по картонным шаблонам и сваривают в единое целое. Для жесткости конструкции к листам приваривают ребра жесткости из труб или уголков. В корпусе следует предусмотреть все отверстия: для вала, загрузочного бункера и для выхода щепы.
Готовые детали собираются в механизм. На рабочий вал насаживается диск, молотки и подшипники. Вся конструкция закрывается кожухом. Диск ни в коем случае не должен касаться корпуса. Зазор должен составлять порядка 30 мм.
Привод монтируется на заключительном этапе. Самодельный щепорез может работать от электродвигателя напряжением 220 или 380 В. Допускается работа от бензинового или дизельного мотора.
Электродвигатели обладают небольшой мощностью, зато малошумные и более экологичные. Двигатели внутреннего сгорания более производительны, но их работа сопровождается выделением вредных выхлопных газов.
Самодельные щепорезы выгодны при изготовлении арболита для частного строительства.
О том, как сделать щепорез своими руками, смотрите в следующем видео.
как сделать щепорез своими руками по чертежу? Выбор древесной дробилки для производства арболитовой щепы
Арболит как строительный материал был запатентован еще в первой половине XX века. В нашей стране широко применяться он стал в последние годы.
Арболит или деревобетон (щепобетон) выпускается в виде блоков. Используется для возведения малоэтажных строений. Как следует из названия, в качестве наполнителя выступает древесная щепа. В ход идут отходы деревьев хвойных и лиственных пород.
Арболит относится к недорогим строительным материалам, отличающимся высокой экологичностью, малым весом блоков, отличной способностью удерживать тепло. Древесные отходы в составе смеси деревобетона составляют более трех четвертей – от 75 до 90 процентов.
Что это такое?
Отходы деревообработки являются ценным строительным материалом. После измельчения до определенных размеров они становятся наполнителем бетонных смесей. Используется щепа для арболита или как его именуют щепобетона. Арболитовые блоки имеют массу достоинств. Доступная стоимость играет немалую роль. Кроме того, дом, построенный из арболита, практически не требует дополнительного утепления.
Есть у щепы и иные достоинства. Материал пригоден для использования в качестве:
- топлива для печей – в чистом виде или в виде гранул;
- декора – дизайнеры предлагают его в окрашенном и естественном виде для оформления дачных участков и даже парков;
- составляющей для изготовления и украшения мебели;
- ингредиента, используемого при копчении различных продуктов питания.
В производстве мелкие фракции идут на изготовление других стройматериалов: картона, гипсокартона, ДСП и ДВП.
Из чего делают?
Для производства щепобетона подходит практически любая древесина. И все же предпочтительно использование хвойных пород, к примеру, ели или сосны. Из лиственных более качественная щепа получается из березы. Подходят и другие твердолиственные породы: осина, дуб и тополь.
При выборе древесины для арболита нужно знать ее состав. Так, лиственница не подходит для данного строительного материала из-за высокого содержания веществ, негативно влияющих на цемент. Ядом для цемента являются сахара. Кроме лиственницы, они в большом количестве имеются в древесине бука. Следовательно, отходы этого дерева использовать тоже нельзя.
Очень важный момент – срок рубки леса. Щепу нельзя делать сразу после вырубки. Материал должен вылежаться в течение трех – четырех месяцев.
Практически все отходы могут стать исходниками для изготовления щепы.
- ветки и сучки;
- верхушки деревьев;
- горбыль;
- остатки и обломки;
- вторичные отходы.
Допускается наличие в общей массе древесины для производства щепы хвои и листьев – не более 5%, а коры – не более 10%.
Наиболее часто щепу изготавливают из елей и сосен. Выбор в пользу хвои неслучаен. Дело в том, что любая древесина содержит в себе такие вещества, как крахмал, сахара и прочие вещества, способные существенно повлиять на снижение качества арболита. В процессе производства приходится выводить вредные составляющие. Поскольку в хвое их меньше, именно на эти породы приходится меньше усилий, времени и материальных затрат на подготовку щепы.
Какой должна быть щепа?
Древесный наполнитель для арболита имеет свой ГОСТ. На уровне государственного стандарта для щепы установлены жесткие требования.
Выделены три основных параметра:
- длина не больше 30 мм;
- ширина не больше 10 мм;
- толщина не больше 5 мм.
Обозначены и оптимальные размеры по ширине и длине:
- длина – 20 мм;
- ширина – 5 мм.
Новые требования появились с принятием ГОСТ 54854-2011. До этого существовал другой ГОСТ с меньшими требованиями. Тогда допускалось использование более длинной щепы – вплоть до 40 мм. В 2018 году «вольности» в размерах наполнителя не допускаются.
Стандарт регламентирует и наличие примесей: коры, листьев, хвои. Материал следует очищать от земли, песка, глины, а в зимнее время – от снега. Наличие плесени и загниваний недопустимо.
Выбор оборудования для изготовления
Наиболее подходящим оборудованием для получения щепы требуемой формы и размеров является специальный деревообрабатывающий шредер. Однако стоимость станка настолько высока, что вне производства приходится искать другие варианты.
Арболит вполне возможно изготавливать в домашних условиях. Для этого и щепу нужно делать самостоятельно. Измельчителем древесины в условиях подсобного хозяйства становится щеподробильный станок. Щепорезы бывают трех типов.
- Дисковые рубильные машины обрабатывают древесину различной формы. За счет регулировки наклона режущего инструмента можно получать заготовки требуемого размера.
- В барабанных щепорезах измельчают всевозможные отходы: лесозаготовительные, мебельного производства, обрезков после строительства. Сырье загружают в объемный бункер, откуда оно попадает в камеру и разрезается ножами с двусторонними лезвиями.
- Роторные дробилки молоткового типа выпускаются с двумя или одним валом. Основные элементы устройства – молотки и отбойники. Сначала древесина измельчается ударным способом, затем готовая продукция просеивается сквозь сито. От величины ячеек сита зависит размер получаемой щепы.
Во всех перечисленных устройствах предусмотрена только ручная загрузка материала.
Принцип производства
Принцип работы щепорезов сводится к нескольким этапам.
Сначала отходы – доски, горбыль, обрезки, сучки и другое сырье – закладываются в загрузочный бункер. Оттуда все это подается в закрытую камеру, где на валу вращается мощный диск. На плоском диске имеются прорези. На нем, кроме того, закреплены несколько ножей. Ножи движутся под углом. За счет этого обрабатываемая древесина разделяется на небольшие пластины с косым резом.
Сквозь дисковые прорези пластины проникают в барабан, где стальные пальцы производят дальнейшее измельчение. Пальцы и пластины крепятся на том же валу, что и диск. Пластины установлены очень близко к барабану. Они перемещают размолотую щепу по внутренней поверхности барабана.
Нижняя часть барабана снабжена сеткой с ячейками, обеспечивающими заданные размеры щепы. Размер ячейки варьируется от 10 до 15 мм в диаметре. Как только готовая к использованию щепа попадает в нижнюю зону в вертикальном направлении, она проходит сквозь сетку в поддон. Оставшиеся частицы проворачиваются, удерживаемые пластинами, еще круг. В это время их положение постоянно меняется. Достигнув низа в нужном направлении, они также оказываются в поддоне.
Щепорезы могут иметь как электрический, так и бензиновый приводы. Мощность двигателя небольшого устройства находится в пределах четырех – шести киловатт, в более солидных доходит до 10-15 кВт. От мощности зависят способности устройства. С ее увеличением растет объем продукции за час работы механизма.
Как сделать щепорез своими руками?
Тем, кто захочет сделать собственный щепорез, потребуется чертеж устройства, материалы, определенные знания и навыки. Чертеж можно найти в интернете, к примеру, тот, что прилагается.
Узлы и детали придется делать и собирать самостоятельно.
Один из основных элементов механизма – диск диаметром порядка 350 мм и толщиной примерно 20 мм. Если ничего подходящего в хозяйстве не имеется, придется вытачивать из листа. Для посадки на вал потребуется сделать хорошо центрированное отверстие с пазом под шпонку. Кроме того, нужно будет выпилить три паза, сквозь которые древесина станет попадать под молотки, и нужное количество монтажных отверстий.
Несколько проще обстоят дела с ножами. Их делают из автомобильных рессор. На ножах просверливаются по два отверстия под крепеж. Кроме сверла, потребуется зенкер. Зенковка позволит утопить потайные головки крепежных деталей. Плотно прикрепить ножи к диску не составит труда любому взрослому мужчине.
Молотки представляют собою обычные стальные пластины, имеющие толщину около 5 мм. Крепятся они на роторе с шагом 24 мм. Купить молотки можно в магазине.
Сито для щепореза – это длинный (около 1100 мм) цилиндр (Д= 350 мм), свернутый и сваренный из листа. Примечательно, что отверстия в сите должны иметь не ровные, а рваные края. Поэтому их не высверливают, а вырубают, к примеру, пробойником с диаметром от 8 до 12 мм.
Все режущие и вращающиеся детали должны закрываться кожухом. Кожух, как и приемный бункер, изготавливают из листовой стали. Отдельные детали вырезают по картонным шаблонам и сваривают в единое целое. Для жесткости конструкции к листам приваривают ребра жесткости из труб или уголков. В корпусе следует предусмотреть все отверстия: для вала, загрузочного бункера и для выхода щепы.
Готовые детали собираются в механизм. На рабочий вал насаживается диск, молотки и подшипники. Вся конструкция закрывается кожухом. Диск ни в коем случае не должен касаться корпуса. Зазор должен составлять порядка 30 мм.
Привод монтируется на заключительном этапе. Самодельный щепорез может работать от электродвигателя напряжением 220 или 380 В. Допускается работа от бензинового или дизельного мотора.
Электродвигатели обладают небольшой мощностью, зато малошумные и более экологичные. Двигатели внутреннего сгорания более производительны, но их работа сопровождается выделением вредных выхлопных газов.
Самодельные щепорезы выгодны при изготовлении арболита для частного строительства.
О том, как сделать щепорез своими руками, смотрите в следующем видео.
дробилка для арболита своими руками
Щепорез для арболита. Можно ли сделать своими …
2021-7-25 Корпус дробилки для арболита Для изготовления подойдет листовое железо 8–12 мм толщиной. Его разрезают и сваривают в необходимую конструкцию. Кожух может быть как съемным, так и откидным.
Как сделать щепорез для арболита своими руками …
2017-7-15 Дробилка для арболита, изготовленная своими руками по желанию может иметь питание в 220–380 В и состоит из следующих узлов:
Дробилка (щепорез) ВМ-Торнадо-Арболит
2021-8-8 Щепа для арболита своими руками — реально При производстве арболитобетона основной проблемой является подготовка качественного сырья — древесной щепы.
Измельчитель древесины для производства …
2021-7-18 Сделанная «своими руками» дробилка в Кировской области. Результат работы Основной состав щепы – мелкие опилки, также имеются включения
Щепорез для арболита своими руками: чертеж …
2021-8-11 Щепорез для изготовления арболита: принцип работы Прежде, чем начать делать щепорез для арболита своими руками, следует тщательно изучить чертежи, рассмотреть конструкцию, отыскать все необходимые детали и только …
Щепорез для арболита своими руками: подробное …
Дробилка для арболита, изготовленная своими руками по желанию может иметь питание в 220–380 В и состоит из следующих узлов: Металлический корпус со
Правильная щепа для арболита — KBLOK
2021-7-13 Перед тем, как сделать щепу для арболита своими руками, необходимо подготовить дерево. Древесина берется сырая, после рубки должно пройти от двух до четырех месяцев.
Щепа для арболита: как сделать щепорез своими …
2018-11-13 Щепа для арболита: как сделать щепорез своими руками по чертежу? Выбор древесной дробилки для производства арболитовой щепы Главная
Как Сделать Щепу для Арболита Своими Руками с …
2020-12-3 Щепа для арболита своими руками Как только вы решите построить дом из арболита, перед вами сразу встанет вопрос — где купить арболит? или где купить то, из чего можно сделать арболит? И если с первым вопросом все просто …
Щепа для арболита: как сделать щепорез своими …
Самодельные щепорезы выгодны при изготовлении арболита для частного строительства. О том, как сделать щепорез своими руками, смотрите в следующем видео.
Дробилка (щепорез) ВМ-Торнадо-Арболит
2021-8-8 Щепа для арболита своими руками — реально При производстве арболитобетона основной проблемой является подготовка качественного сырья — древесной щепы.
молотковая дробилка арболит опилки своими …
» дробилка щековая щдс-п-2,5х4,0 строммашина » аренда дробильные машины для утилизации бетона » промышленная щековая дробилка цены » мини-дробилки для строительных отходов
Правильная щепа для арболита — KBLOK
2021-7-13 Перед тем, как сделать щепу для арболита своими руками, необходимо подготовить дерево. Древесина берется сырая, после рубки должно пройти от двух до четырех месяцев.
Щепа для арболита: изготовление своими руками
Щепорез для арболита своими руками: чертежи, схемы, узлы сборки Если вы планируете заниматься строительством дома из самостоятельно изготовленных арболитовых блоков или монолитного арболита, то вам понадобиться …
Щепа для арболита: как сделать щепорез своими …
2018-11-13 Щепа для арболита: как сделать щепорез своими руками по чертежу? Выбор древесной дробилки для производства арболитовой щепы Главная
Как Сделать Щепу для Арболита Своими Руками с …
2020-12-3 Щепа для арболита своими руками Как только вы решите построить дом из арболита, перед вами сразу встанет вопрос — где купить арболит? или где купить то, из чего можно сделать арболит? И если с первым вопросом все просто …
Дробилки для щепы своими руками: чертежи, фото …
2021-8-21 Узнаем, как делать дробилки для щепы своими руками, и какие использовать ножи для щеподробилок. В статье чертежи, фото, видео, а также пошаговая инструкция по производству самодельных станков-измельчителей древесины …
Арболит своими руками — состав и пропорции для …
2021-8-21 Арболит своими руками Вот теперь дошли именно до практической части. Одно дело, когда производство выдержано для массового производства, а другое дело, когда все делается для
Щепорез для арболита своими руками: подробное …
2019-6-28 Как сделать щепорез для арболита своими руками: чертежи и схемы Если вы планируете заниматься строительством дома из самостоятельно изготовленных арболитовых блоков или монолитного арболита, то вам
Щепорез для арболита своими руками: подробное …
2021-7-6 Пошаговая инструкция изготовления щепореза для арболита своими руками: конструкция станка, узлы и детали, сборка и проверка работы Как собрать корпус Из листа стали вырезается два блина диаметром 50-100 см (или более) в …
Дробилка (щепорез) ВМ-Торнадо-Арболит
2021-8-8 Щепа для арболита своими руками — реально При производстве арболитобетона основной проблемой является подготовка качественного сырья — древесной щепы.
Дробилка для костей своими руками чертежи
2021-3-5 Если помимо измельчения садовых веток вы преследуете другие цели (подготовка сырья для производства арболитовых плит), то ваша дробилка для дерева своими руками непременно потребует запаса мощности.
Щепа для арболита: как сделать щепорез своими …
2018-11-13 Щепа для арболита: как сделать щепорез своими руками по чертежу? Выбор древесной дробилки для производства арболитовой щепы Главная
Правильная щепа для арболита — KBLOK
2021-7-13 Перед тем, как сделать щепу для арболита своими руками, необходимо подготовить дерево. Древесина берется сырая, после рубки должно пройти от двух до четырех месяцев.
Щепорез для арболита своими руками: подробное …
2021-7-6 Пошаговая инструкция изготовления щепореза для арболита своими руками: конструкция станка, узлы и детали, сборка и проверка работы Как собрать корпус Из листа стали вырезается два блина диаметром 50-100 см (или более) в …
Щепа для арболита: изготовление своими руками
Щепорез для арболита своими руками: чертежи, схемы, узлы сборки Если вы планируете заниматься строительством дома из самостоятельно изготовленных арболитовых блоков или монолитного арболита, то вам понадобиться …
Как Сделать Щепу для Арболита Своими Руками с …
2020-12-3 Щепа для арболита своими руками Как только вы решите построить дом из арболита, перед вами сразу встанет вопрос — где купить арболит? или где купить то, из чего можно сделать арболит? И если с первым вопросом все просто …
Щепорез для арболита своими руками: подробное …
2019-6-28 Как сделать щепорез для арболита своими руками: чертежи и схемы Если вы планируете заниматься строительством дома из самостоятельно изготовленных арболитовых блоков или монолитного арболита, то вам понадобиться …
ПрКакую дробилку выбрать для арболита
Почему нужна дробилка для производства арболита и какую выбрать Основной компонент для арболита – это древесная щепа, которая может составлять 90% всего объема.
Щековая дробилка для дерева: виды, принцип …
2020-10-29 Щековая дробилка для дерева: виды, принцип действия и способ изготовления своими руками – Дробилки для дерева б/у и новые
состав, пропорции по ГОСТ, изготовление своими руками
Арболитовые блоки все чаще стали использовать при возведении одноэтажных домов, внутренних перегородок в них, гаражей, хозяйственных построек. Впервые о них как о строительном материале для изготовления временного и постоянного жилья заговорили в середине 20 века.
Оглавление:
- Состав арболита
- Пропорции
- Как сделать своими руками?
Несмотря на то, что основным компонентом является дерево, по многим характеристикам арболит не уступает традиционным материалам, он сохраняет тепло и комфортабельную обстановку в построенных из него помещениях.
Из чего состоят блоки?
Компонентный состав арболита рассчитан так, что он способствует сохранению его прочности, огнестойкости и долговечности. В него входят: вода, наполнители, цемент, химические добавки.
1. Наполнители. Применяются отходы переработки сельскохозяйственных культур (чаще костры льна) и деревообработки (щепа).
- Древесная щепа – самый распространенный компонент. При производстве блоков из арболита берется щепа длиной до 15 см и шириной не более 2 см, без присутствия листьев и примесей. Вместе со щепой можно добавить опилки или стружку в соотношении 1:1. Используются в основном хвойные породы древесины, намного реже – лиственные.
- Костры льна. Являются полноценным материалом для арболита. Используются в том виде, в каком они были на предприятии: их не надо дополнительно измельчать. При длине частиц льна 15-20 см и ширине до 5 см качество получаемых блоков высокое.
2. Все наполнители содержат в составе сахара и смоляные кислоты, препятствующие адгезии цемента с их частичками. Для уменьшения их количества и минерализации щепы (костр льна) применяются: сернистый глинозем, хлорид кальция, жидкое стекло, известь. Эти компоненты повышают биологическую устойчивость, снижают водопроницаемость, увеличивают срок эксплуатации блоков. Их можно использовать как самостоятельно, так и сочетать между собой: хлорид кальция и сернокислый глинозем (1:1), жидкое стекло и гашеную известь (1:1). Каждую добавку перед применением необходимо растворить в воде.
3. Вода – берется обычная техническая.
4. Цемент – используется с маркой 400 или 500 (можно выше).
Пропорции компонентов
При изготовлении арболита следует строго соблюдать соотношение всех ингредиентов между собой. Расход материалов в процентном содержании:
- соотношение наполнителей составляет 80-90%;
- примерный объем цемента в общей массе – 10-15%;
- объем воды – 60-70%;
- химические добавки – 2-4%.
Для производства 1 м3 материала берутся следующие пропорции компонентов в арболитовых блоках: по 300 кг наполнителя и цемента, 400 л воды.
При обработке наполнителей используется чаще всего известковый раствор. Он готовится в пропорции: 2,5 кг извести, 150-200 л воды на 1 м3 древесной щепы (костр льна). Чтобы ускорить затвердевание и улучшить свойства материала, добавляются хлористый алюминий, жидкое стекло, хлористый кальций в соотношении: на 1 м3 арболита – до 10 кг. Такой состав смеси является классическим, а изменение пропорции компонентов может негативно сказаться на качестве.
Изготовление арболита
Сделать блоки из арболита можно самому, а не приобретать готовые. При этом нет необходимости вкладывать большие финансовые средства на покупку дорогого спецоборудования и сырья.
Перед тем как сделать арболитовые блоки своими руками необходимо приготовить:
- лоток для замешивания смеси или бетономешалку;
- разъемные формы;
- лопату;
- крупное сито;
- поддон металлический.
Предварительно следует позаботиться о формах для выработки блоков из арболита. Их можно приобрести или сделать своими руками. Для изготовления используются доски до 2 см толщиной, скрепленные по требуемым размерам. С внешней стороны их отделывают пленкой (фанерой).
Перед тем как делать блоки из арболита, наполнитель выдерживается около 40 дней на улице. Это очищает его состав от сахаров и смоляных кислот. В течении всего времени его следует переворачивать и «тормошить» до 4 раз в день, чтобы дать возможность воздуху свободно проникать в нижний слой. Для достижения максимального эффекта и ускорения процесса распада сахаров и кислот наполнители рекомендуется поливать 15% раствором извести. Она же является прекрасным антисептиком. Затем отлежавшийся состав просеивается ситом с крупными ячейками, что избавляет его от остатков земли и постороннего органического мусора.
Вся работа выполняется в такой последовательности:
1. Очищенный наполнитель замачивается в воде. В этот состав добавляется жидкое стекло и перемешивается бетономешалкой или вручную (при небольшом объеме).
Смесь для изготовления арболитовых блоков готовится в пропорции: 6:2:1, это означает, что на 6 мешков наполнителя потребуется 2 просеянного песка и 1 цемента. При замешивании не надо все компоненты сразу загружать в бетономешалку. Их лучше закладывать порциями, не выключая агрегат. Частями заливается и вода. Такой способ даст возможность избежать образования комков и повысит конечное качество материала.
2. Подготовить формы для заливки. Для этого их внутренняя сторона обмазывается известковым молочком. Чтобы не было прилипания массы к стенкам, их можно обшить линолеумом.
3. Арболитовая смесь заливается в формы. Чтобы не допустить образования завоздушленных участков, после заполнения вся масса взбалтывается, стенки простукиваются.
4. Смесь уплотняется электрической (пневматической) трамбовкой, можно использовать вибропресс. Выдерживается около суток.
Формы ставятся в затененное место, укрываются пленкой и выдерживаются около трех недель на воздухе при температуре не меньше 15 С. Изготавливая блоки своими руками, специалисты советуют первую партию сделать небольшой, чтобы проверить качество и правильность взятых пропорций всех компонентов.
Блоки из арболита готовы к возведению строения после того, когда достаточно хорошо схватятся. Главное условие – это обязательная внешняя отделка.
Строительство дома из опилок — Зеленые дома
Статья о строительстве дома из опилок и о том, как этот дом сохранился тридцать лет спустя.
Тридцать лет назад — сразу после Второй мировой войны, когда так много интересных вещей человеческого масштаба все еще делалось на стольких полях — парень из Айдахо построил дом из опилок и бетона. И Popular Mechanics , среди других публикаций, сообщил о строительстве этого дома. Подходит для Popular Mechanics .
Беда только в том. . . С тех пор мы ждали следующего отчета, который расскажет нам, насколько хорошо это необычное здание выдержало испытание временем. И — поскольку не похоже, что кто-то еще заинтересован в этом продолжении, МАТЬ взялась за проект.
Итак, вот оригинальная история Popular Mechanics , написанная 30 лет назад. . . и новости MOTHER о доме Уэйт Фриберг из опилок / бетона, как он выглядит и работает сегодня.
Перепечатано с разрешения Popular Mechanics , авторское право © 1948, H.Х. Виндзор.
Любой, кто переживает возрождение старого желания использовать опилки и стружку вместо песка и гравия, чтобы получить более легкий и дешевый бетон, должен познакомиться с крошечной диатомовой водорослью — чудо-природным растением — и с тем, как Уолт Фриберг использовал ее для сокращения затрат. в своем новом доме в Москве, штат Айдахо.
Стены, полы и крыша дома выполнены из опилочного бетона. Объединив древесные отходы и диатомитовую землю, каждый кубический дюйм которой содержит миллионы микроскопических чудесных растений, Фриберг вдвое сократил стоимость этих частей своего дома и получил превосходную изоляцию.
Когда он вернулся на факультет сельскохозяйственной инженерии Университета Айдахо, Фриберг, ветеран армейских инженеров, стал искать дом.
Он видел опилки и стружку, сжигаемые как отходы на мельницах в его местности. Он понял, что строительство дома из древесных отходов было давней мечтой. Большинство инженеров давно оставили надежды получить удовлетворительный древесный бетон. Когда смесь была бедной, чтобы использовать дешевые древесные отходы, полученный бетон не был прочным и горел почти так же быстро, как дерево.Когда смесь была достаточно густой, чтобы быть огнестойкой, дополнительный использованный цемент уничтожил большую часть экономии на песке и гравии, а также разрушил большую часть изоляционных свойств древесины.
Но во время войны Фриберг узнал кое-что о диатомовых водорослях, что придало ему смелости снова открыть старый вопрос. Кизельгур использовался в промышленности как изолятор и огнезащитный состав. Он видел, как волшебный материал, добавленный к бетонной смеси при строительстве гигантских мелиоративных дамб в Калифорнии, значительно повысил ее работоспособность.Возможно, диатомовая земля решит проблему опилок и бетона. Эта догадка оправдалась, и сегодня диатомовые водоросли находятся в центре внимания зданий.
Отложения диатомовых водорослей широко распространены в США. Некоторые из крупнейших месторождений находятся в Орегоне, Калифорнии, Неваде и Вашингтоне. Из-за его стратегического значения во время войны велись интенсивные поиски новых месторождений. Были найдены многие. Хотя большинство новых слишком малы или недостаточно чисты для промышленного использования, они подходят для бетона из опилок и стружки.
Во времена дедов диатомовая водоросль была просто интересным маленьким растением, на которое можно было смотреть в микроскоп. Школьные учителя поразили своих учеников чудесами природы, подняв небольшую щепотку диатомовой земли и сказав им, что она содержит тысячи и тысячи крошечных раковин.
Однако за последнее десятилетие диатомовые водоросли заняли ведущее место в промышленности. Он используется в зубной пасте, лаке для серебра и лаке для ногтей, в очищающих фильтрах на сахарных заводах, в качестве изоляторов в высоковольтных двигателях и электрическом оборудовании, а также в качестве наполнителя в красках.Кизельгур имеет более сотни промышленных применений, в основном в химической, пищевой и фармацевтической областях.
Фриберг обнаружил, что когда небольшая часть цемента была заменена некоторым количеством диатомовой земли и добавлена немного обычной глины, в результате получился недорогой, обладающий высокими изоляционными свойствами, огнестойкий и легкий бетон. Стоимость, примерно половина стоимости обычного бетона, варьируется в зависимости от местности, в зависимости от наличия древесных отходов и расстояния от месторождения диатомитовой земли.
Бетон Фриберга не выдерживает больших нагрузок.Но поскольку один дюйм этого материала имеет изоляционную ценность от 12 до 14 дюймов обычного бетона, он отлично подходит для полов и стен, где требуется высокая изоляция и нагрузка может нести облицовка из кирпича или досок. Опилки-бетон можно распиливать, сверлить и забивать гвоздями, как и по дереву, и они обладают удивительной огнестойкостью. Вот смесь, которую он использовал: одна часть цемента, одна часть диатомитовой земли, три части опилок, три части стружки и одна часть глины. . . все измерения объема. Поскольку бетон из опилок имеет более высокую степень абсорбции, чем прямой бетон, Фриберг добавил в смесь одну часть глины.
Сначала в бетономешалку загружается глина. Если она комковатая, перед использованием ее следует замочить на ночь. Затем засыпается диатомит, затем цемент. После тщательного перемешивания добавляют опилки и стружку.
В своем доме Фриберг использовал опилки заводской обработки, которые постарели около года. В ходе экспериментов он обнаружил, что новые опилки нежелательны. Также нет опилок, которые стояли так долго, что они белые. По его словам, годичный срок старения — это правильно.При стружке возраст не важен. Он использовал их зеленые, возрастом от года и старше. Все они работали хорошо.
В доме использовалась смесь опилок и стружки сосны, лиственницы и пихты. В отходах была кора. Фриберг не нашел возражений против этого, но он обнаружил, что кедровые и твердые древесные отходы не подходят.
Для использования диатомовых водорослей в домашних условиях не требуется специального оборудования. Литые блоки и кирпич Friberg на промышленном оборудовании для производства сборного железобетона.Он также отливал маленькие и большие плиты, используя простые формы, подобные тем, которые используются при строительстве домов из сырца. Поскольку бетон такой легкий, он вылил пол и крышу своего дома одной плитой.
Для испытания бетонных опилок компания Friberg отлила плиты размером 32 на 48 дюймов и толщиной один дюйм. Ближе к краю этих плит он забивал гвозди за восемь пенсов и просверливал ряды отверстий с помощью дрели. Расщепления не было. Потом пил пилой порезал полосы шириной в дюйм. С помощью шлифовальной машины он создал гладкую поверхность, которую можно было красить.Он проверил плиту на изоляционные свойства и обнаружил, что она равна футу или более бетону.
Фриберг считает, что плита размером 3-5 / 8 на 32 на 48 дюймов, которую можно собирать и отверждать в свободное время, будет полезна в хозяйственных постройках. Этот размер будет охватывать две стойки или балки пола или может быть распилен, чтобы поместиться между стойками. Фермеры Северо-Запада уже проявляют интерес к его использованию для молочных коровников и птичников, где существует большая потребность в недорогом материале, обладающем высокой изоляционной способностью.
Когда-нибудь будет найден способ гидроизоляции бетона.До тех пор Фриберг рекомендует использовать его только в помещении. Есть еще одно ограничение. Обладая прочностью нагрузки от одной четверти до одной трети, чем у обычного бетона, он не может использоваться на тротуарах или проездах, а также для полов и стен, которые несут большие нагрузки.
Но даже если эти ограничения никогда не будут полностью преодолены, Фриберг видит огромное поле для крошечной диатомовой водоросли, кучи опилок и стружки. Пол в его гостиной, например, представляет собой сплошной блок из недорогого материала.Прямо на него крепятся ковролин и линолеум. Крыша также представляет собой цельный блок, покрытый рубероидом и измельченной пемзой. В стенах его дома основную нагрузку несет слой обычных бетонных кирпичей. Утеплитель обеспечивают опилочно-бетонные кирпичи двойной толщины.
Поскольку месторождения диатомита были исследованы во время войны, государственные геологические департаменты и шахтные школы имеют информацию об их местонахождении. Итак, если потенциальный строитель может найти удобную кучу опилок и стружки сосны, лиственницы или пихты и недалеко от месторождения диатомовой земли, Фриберг нашел способ собрать их вместе, чтобы произвести новый вид недорогого стройматериала.
Дом Фрибергов 30 лет спустя
Недавно сотрудники MOTHER Мартин Фокс и Трэвис Брок отправились в Москву, штат Айдахо, чтобы найти дом из древесного волокна / диатомита / бетона, о котором сообщал Popular Mechanics 30 лет назад (см. Предыдущий рассказ). Наши бесстрашные сотрудники хотели узнать: сохранилось ли первоначальное здание? Бетонная смесь осела, потрескалась или распалась? Как сооружение выдержало тридцать лет холодных зим в Айдахо?
Ответы на эти вопросы — Мартин и Трэвис быстро усвоили — были «да», «нет» и «очень хорошо, спасибо».
Оказывается, пара по имени Рэй и Барбара Харрисон 23 года назад купила необычный дом из опилок у строителя-новатора дома — Уэйта Фриберга. Рэй и его жена, которые вырастили семерых детей в особенном доме, утверждают, что дом на протяжении многих лет служил им хорошей службой. Основная структура по-прежнему в хорошем состоянии и не имеет признаков разрушения.
Что касается тех «холодных зим в Айдахо», Рэй Харрисон говорит, что — отчасти благодаря отличным изоляционным свойствам опилок — бетонных стен — счета за отопление его семьи обычно составляют на 30-40 долларов в месяц меньше, чем у их соседей, которые живут в однотипные дома обычной постройки.Рэй, однако, быстро добавляет, что, по крайней мере, часть этой экономии тепла может быть отнесена на счет «пассивных» конструктивных особенностей солнечного тепла, которые Уолт Фриберг внедрил в дом.
Например, северная сторона дома выстроена на склоне, а большие окна закрывают большую часть южной стороны дома. Более того, прямо над окнами, выходящими на южную сторону, находится серия алюминиевых отражателей, которые направляют в жилище даже больше энергии зимнего солнца, чем обычно проникает внутрь.(Те же самые отражатели несколько затемняют окна и помогают защищать от нежелательной жары летом). Ночью, семья Харрисонов; «закрыть» солнечное тепло в здании, натянув прочно изолированные шторы за окнами, выходящими на юг.
Если вы до сих пор следили за этой историей, вам может быть интересно [1], были ли когда-либо построены какие-либо другие конструкции с использованием «древесно-волокнистого и диатомитового» бетона, разработанного Вальтером Фрибергом, и [2] что с этим случилось? во всяком случае, умный парень Фриберг.Что ж, Уолт — за эти годы — построил или помог построить около 30-40 зданий из опилок в северном Айдахо / восточном районе Вашингтона. . . и он все еще работает с материалом. Уолт говорит, что он считает, что с точки зрения стоимости материалов и энергии его необычная бетонная смесь сегодня даже более привлекательна, чем 30 лет назад.
Первоначально опубликовано: январь / февраль 1978 г.
Деревянные блоки — виды, состав, особенности изготовления | Своими руками
Безопасные недорогие материалы, существенно сокращающие сроки строительства, на рынке малоэтажного домостроения всегда актуальны.
Что ожидать дачнику, не имея большой суммы на строительство дома?
Доступная по цене и удовлетворяющая всем требованиям безопасности (пожарной, физической, химической и биологической) группа материалов, получившая условное название «арболит ».
Древесная щепа разного размера (щепа, опилки, щепа) служит в этих материалах наполнителем, связующим. В качестве связующего используется бетон. Изначально сырье измельчается в крошку и обрабатывается минерализующим составом (сульфат кальция, хлорид кальция, сульфат алюминия, жидкое стекло и др.)), который действует как антисептик и усиливает адгезию связующего вещества к дереву. Затем «глазированные» минерализующие добавки, древесная стружка и цемент замешиваются в массу, из которой формируются материалы в виде пластин или блоков.
Совет
Весь арболит легко обрабатывается. Их можно резать, сверлить, соединять гвоздями и т. Д. Уникальная текстура поверхности улучшает адгезию к штукатурке и бетону.
Масса достоинств
Благодаря объемной минерализации изделия из щебеночного бетона не гниют, геометрически устойчивы, устойчивы к влаге, не поддерживают горение, не выделяют вредных летучих веществ.
Материалы обладают высокими теплоизоляционными свойствами, способны поддерживать тепловой комфорт в помещениях на уровне современных требований к теплоизоляции, поглощают шум. Биологическая стабильность материалов этой группы также заслуживает похвалы: они не подвержены воздействию насекомых, древоточцев или грызунов.
Опилки + бетон
Самый известный материал этой группы — цементно-стружечные плиты (ЦСП). Материалом для их производства служат опилки мелкой и средней фракций и цемент.
В процессе производства все компоненты укладываются послойно (с мелкими опилками во внешнем слое и более крупными внутри) и запрессовываются в плиты плотностью 1100/1400 кг / м3. Толщина пластин варьируется от 8 до 36 мм.
В зависимости от толщины и плотности такие изделия используются в самых разных местах: в качестве наружной обшивки каркасных конструкций, для устройства перегородок внутри сухих и влажных помещений, для устройства оснований под перекрытиями и мансардными перекрытиями, в помещениях. украшение подоконников и т. д.Находят свое применение плиты ДСП при опалубке, как съемной, так и несъемной. Чтобы закрепить цементно-стружечные плиты гвоздями, необходимо предварительно просверлить отверстия.
Арболит: щепа + бетон
Другая группа арболитов состоит из материалов, образованных из крупной крошки хвойных деревьев и портландцемента. Небольшие воздушные полости между крупными стружками обеспечивают этим материалам высокие тепло- и звукоизоляционные характеристики. Пористая структура позволяет им «дышать».
Один из материалов этой группы — арболит — известен на отечественном рынке еще с советских времен.Фактически, это разновидность легкого бетона, и стружка имеет длину 2–20 мм, ширину 2–5 мм и толщину 5 мм. В качестве вяжущего используется обыкновенный портландцемент марки не ниже М400.
Арболит делится на теплоизоляционный (плотность — до 450 кг / м 3 ), конструкционный и теплоизоляционный (450-600 кг / м 3 ) и конструкционный (600-800 кг / м 3 ). ). Последний используется в виде крупноформатных блоков, из которых возводятся малоэтажные малоэтажные дома.
Смотрите также: Блоки из арболита своими руками (+ видео)
Примечание
К недостаткам арболита можно отнести недостаточную влагостойкость и высокую влагопроницаемость. Стены из арболита нуждаются в защитно-отделочном слое. Фундамент следует гидроизолировать. как здесь виден дом с арболты
Технология «Велокс»
Основным элементом строительной системы «Велокс» являются стружечно-цементные плиты размером 2000 х 500 мм и толщиной 25, 35, 50 и 75 мм, используемые в качестве несъемной опалубки.При комплектации опалубочной системы изнутри плит, из которых будет собираться внешняя стена, приклеивается теплоизоляционная вставка из пенополистирола. Таким образом, обеспечиваются высокие тепловые характеристики ограждающих конструкций.
Монтаж первого ряда опалубки Velox производится по разметке на фундаменте. Монтаж плит начинается с углов. В местах стыковки стен опалубку фиксируют саморезами. Одновременно со сборкой первого ряда монтируют арматурный каркас и прокладывают скрытые инженерные коммуникации.
Второй и последующие ряды опалубки собирают с зачисткой швов. Для заливки нераздельных секций плиты разрезают стационарной дисковой пилой или «болгаркой».
Блоки «Дюрисол»
Упростить и ускорить процесс возведения несъемной опалубки позволяет технология Durisol. При этом используются стружкоцементные блоки длиной 500 мм и высотой 250 мм, их толщина в зависимости от назначения составляет 150, 220, 250, 300 и 375 мм. Типовые серии включают стандартные, рядные, универсальные и дополнительные блоки для возведения внешних и внутренних несущих стен и межкомнатных перегородок.
Из универсальных блоков выкладываем углы, перемычки, торцы, обрамление оконных и дверных проемов. В комплект поставки также входят утеплители из пенополистирола или минеральной ваты (по желанию клиента) толщиной 70-175 мм.
После каждых четырех рядов кладки внутренняя полость опалубки заполняется бетонной смесью (вручную или с помощью бетононасоса). Как только бетон застынет, продолжайте сборку блоков. Чтобы уменьшить технологические перерывы, используйте подпорную конструкцию, которая позволяет возводить и бетонировать стену до высоты одного этажа.
Наш совет
Установка опалубки
Durisol и последующее бетонирование проводят поэтапно — каждые четыре ряда на один квадратный метр стены уходит восемь стандартных блоков.
См. Также: Арболит и другие строительные материалы на его основе (арболит, опилки, фибробетон и др.)
Фибролит
При производстве фибролита (еще называемого фибробетоном) используйте специальную стружку — длинную и тонкую (длиной 250-500 мм и шириной 1-4 мм).Это древесное волокно обрабатывают жидким стеклом и смешивают с бетоном, и из полученной смеси методом прессования формуют плиты толщиной 30-150 мм. Плиты обладают недостаточной прочностью на изгиб, но являются хорошими тепло- и звукоизоляторами.
В зависимости от плотности материал делится на тепло- и звукоизоляционный (плотность 250-300 кг / м 3 ) и конструкционный (более 450 кг / м 3 ). Последняя используется в качестве несъемной опалубки и обшивки каркасных стен.
Не так давно компания Трауллит приступила к производству полноразмерных монолитных стеновых панелей из стеклопластика. В панелях оставляют вертикальные полости и горизонтальные пазы, которые являются опалубкой для железобетонного каркаса, принимающего на себя основную силовую нагрузку конструкции.
Полезное видео — дом из кварталов Дюрисол: изучаем арболит
ИНСТРУМЕНТЫ ДЛЯ МАСТЕРОВ И МАСТЕРОВ И ТОВАРЫ ДЛЯ ДОМА ОЧЕНЬ ДЕШЕВЫЕ. БЕСПЛАТНАЯ ДОСТАВКА. ЕСТЬ ОТЗЫВЫ.Ниже другие записи по теме «Как сделать своими руками — домохозяину!»
Подписывайтесь на обновления в наших группах и делитесь.
Давай дружить!
Дизайн внутреннего дворика: понимание древесной щепы
Из щепы можно сделать неформальный внутренний дворик, но это не продлится долго. Подобно структуре большинства конструкций внутреннего дворика, вы должны начать с раскапывания участка, затем уложить постель из нижележащих слоев с последующим размещением щепы на поверхности.Эти патио экологически чистые и представляют собой чрезвычайно привлекательную альтернативу патио из камня или кирпича.
Древесная щепа
Проверьте древесную щепу на Amazon.
Древесная щепа является побочным продуктом лесной промышленности. Ветки, которые слишком малы для использования в качестве древесины, пропускаются через рубильные машины. Большая часть этой колотой древесины идет на обогрев больших зданий или электростанций. На лесопильных заводах также используется древесина, которая больше не имеет промышленного значения, например старые деревянные поддоны.Некоторые из этих древесных стружек используются в садоводстве и садоводстве.
Вы почти всегда можете найти их в мешках, чтобы использовать их для укладки клумб или для создания неформального патио. Несмотря на то, что древесная щепа недолговечна в саду, поскольку она разрушается и разлагается, она может стать очень привлекательным элементом в саду, и она экологически безопасна.
Использование древесной стружки
Чтобы использовать древесную щепу для создания патио, начните с закладывания фундамента. Это особенно важно, так как площадь должна быть хорошо осушена.При создании фундамента вам потребуется вдвое больше заполнителей поверх слоя песка, чтобы обеспечить хороший дренаж. Если дренаж плохой, щепа очень быстро гниет.
На краю планируемой площади дворика нужно разместить бревна, крупные камни или кирпичи. Этот край будет содержать древесную стружку. В противном случае щепа разлетится по всей территории. Помня о площади сада, всегда ставьте во главу угла размер сада.Бесполезно создавать крошечный участок в большом саду. Он будет полностью потерян. Точно так же нельзя покрывать всю территорию щепой.
Пропорции в озеленении очень важны. То, что вы пытаетесь сделать, должно вписаться в сад. Когда вы работаете с древесной стружкой, постарайтесь сохранить дизайн дерева. Лучше удерживать щепки рядом вертикальных небольших бревен, погруженных в землю чуть выше уровня щепок, чем использовать что-то, что не соответствует окружающему пространству, например кирпич.
Лучше использовать деревянную тему, чем смешивать и сочетать материалы в дизайне вашего патио.
Дизайн
Поскольку древесная щепа не является официальным ресурсом для обустройства, важно помнить об этой особенности при проектировании внутреннего дворика. Держите это свободно и не в формальной договоренности. Это смешивается с самим продуктом. Это неформальный элемент, поэтому вам не нужен квадратный или круглый внутренний дворик. Лучшая дизайнерская идея — это пространство произвольной формы, которое удерживается только ограничениями кромки, которую вы предоставили для своей щепы.
Когда вы совершаете покупки по ссылкам на нашем сайте, мы можем получать комиссионные бесплатно для вас.
Как сделать подъездную дорогу из щепы | Руководства по дому
Грязная подъездная дорога без покрытия — это, в лучшем случае, большой пылеобразователь, а в худшем — риск затопления и эрозии. Материалы, не относящиеся к дорожному покрытию, включают гравий, резиновую мульчу и органическую мульчу, в том числе древесную стружку. Из этих трех только древесную щепу можно получить бесплатно — или почти бесплатно, если речь идет о стоимости доставки или аренде оборудования.Они образуют привлекательное, устойчивое дорожное основание, которое удерживает почву на месте и уплотняется в земле, создавая твердую дорожную поверхность. Создание подъездной дороги из древесной щепы — это постоянная работа, потому что эта органическая поверхность со временем подвергается биологическому разложению и требует периодического добавления новой щепы.
Подготовка
Грязная подъездная дорога в приличном состоянии редко требует большой доработки перед укладкой древесной щепы. Сами по себе древесная щепа помогает исправить мелкие проблемы, такие как гребни или небольшое повреждение стока, потому что они замедляют будущий сток воды и собирают почву, которую она несла.Более серьезные проблемы, такие как глубокие порезы эрозии или дорожное полотно, которое более чем на дюйм или два ниже окружающего ландшафта, должны быть отремонтированы перед укладкой стружки. Когда для ремонта используется тяжелое оборудование, следует перемещать ровно столько грязи, сколько необходимо для выполнения работы. Ветер и вода наилучшим образом справляются с эрозией почвы, которая была нарушена. Почва, вносимая для поднятия дорожного полотна, должна содержать смесь частиц разного размера.
Получение древесной щепы
Древесная щепа доступна в рамках различных муниципальных программ переработки и измельчения или может быть произведена на месте из обрезков деревьев домовладельца, строительных проектов и очистки щетками.Домовладельцы, которым приходится расчищать кусты или упавшие деревья на своей собственности, могут убить двух зайцев одним выстрелом, взяв в аренду или одолжив измельчитель, чтобы расчистить свою собственность и одновременно выровнять подъездную дорожку. Розничные источники древесной щепы включают компании, производящие товары для озеленения, компании по производству материалов и компании по вывозу деревьев. Древесная щепа обычно продается кубическими ярдами.
Укладка древесной стружки
Укладка древесной стружки заключается в простом ее равномерном распределении по поверхности проезжей части.Подъездная дорожка должна быть покрыта на глубину не менее 2 дюймов, но может потребоваться более толстое покрытие, если поверхность проезжей части находится ниже уровня окружающей почвы. Почва, которая особенно рыхлая в дождливую погоду или ниже уровня земли, требует более толстого слоя — до 6 дюймов вполне достаточно. Некоторые стружки вдавливаются в почву, когда она влажная. Когда материал доставляется грузовиком, груз можно сбросить прямо на подъездную дорожку, предпочтительно в самой высокой точке, если подъездная дорога поднимается по склону, и распределить ее широкими граблями для экономии рабочей силы.Лопата для снега также хорошо работает для перемещения щепы.
Техническое обслуживание
Во время первого сезона дождей дорога из щепы, вероятно, потребует дополнительной щепы. Древесная щепа в некоторых местах вдавливается в почву, а часть выскакивает из дорожного полотна из-за автомобильных покрышек. Щепа также может частично засыпаться почвой. Эти изменения положительны; они означают, что стружка смешивается с почвой, заполняя низкие места и обеспечивая более прочную поверхность для движения круглый год. Подъездную дорожку необходимо поддерживать граблями, которые выталкивают стружку, выпадающую на проезжую часть, обратно в привод.Также может потребоваться добавление стружки каждую пружину, чтобы поддерживать желаемую глубину.
Ссылки
Ресурсы
Биография писателя
Билли Джо Джаннен — обозреватель политики и образа жизни в сельском округе Сан-Диего и старший редактор журнала Demand Media. Ее писательская и редакционная карьера длится 23 года, и она специализируется на пограничных и экологических вопросах. Эклектическое образование Яннен включает инженерное дело и садоводство, и она представляет Лигу сельских экономических действий в планировании регионального экономического развития.
Тенденции декоративного бетона: 4 метода создания имитации имитации дерева
Бретт Клайн, генеральный директор, Specialty Flooring
Одна из самых популярных тенденций в области напольных покрытий сегодня — имитация искусственного дерева. Просто прогуляйтесь по своему местному строительному магазину и посмотрите, какие деревянные плитки доступны. Креативные приложения также размещены на сайтах социальных сетей.
В течение многих лет единственным способом добиться текстуры дерева в бетоне была штамповка.Хотя эта практика все еще используется сегодня, есть несколько новых способов добиться более аутентичной деревянной отделки. Ознакомьтесь с четырьмя популярными техниками и приложениями:
- Метод штамповки бетона (в основном снаружи)
Как уже упоминалось, штамповка бетона существует уже много лет. Этот традиционный метод по-прежнему отлично подходит для больших площадей, требующих интенсивного движения и хорошей тяги.
Техника: Вы можете залить новый бетон или нанести цементный слой и штамповать рисунок дерева с помощью резиновых штампов.Могут быть использованы различные методы окраски, наиболее популярными из которых являются окраска всего пола основным цветом, а затем — античным или акцентным — вторым и третьим цветами.
- Обработка щеткой / шпателем (внутри / снаружи)
Этот метод имитации дерева оставляет менее агрессивную текстуру, чем метод штамповки. Конечный продукт выглядит ближе к натуральному дереву (по сравнению с штамповкой) и требует меньше материала. Техника окраски в целом такая же.
Техника:
- Начните с нанесения Super-Krete Bond-Kote с помощью ракеля для достижения гладкой однородной поверхности.
- Затем нанесите ленту с пропиткой волокнами (1/4 дюйма или 1/2 дюйма) по желаемому рисунку деревянной доски.
- Нанесите еще один слой Super-Krete Bond-Kote с помощью ракеля и сразу же протащите по нему бетонную чистовую щетку.
- Сразу после обработки щеткой проведите шпателем по влажному продукту в том же направлении.Это создаст эффект всасывания, который оставит текстуру древесины.
- После высыхания потяните за ленту и нанесите пятно, как при любом другом нанесении штампованного бетона.
- Метод легкой щеткой / шпателем (внутри)
Этот метод очень похож на традиционный метод метла / шпатель. Двумя основными отличиями являются интенсивность текстуры и нанесение окраски. Поскольку вы не можете полностью полагаться на текстуру, чтобы придать вам вид древесины, окраска становится критически важной при использовании этого метода.
Техника:
- Нанесите ракель Super-Krete Bond-Kote с помощью ракеля для получения гладкой однородной поверхности.
- Во-вторых, нанесите ленту с пропитанным волокном (1/4 дюйма или 1/2 дюйма) по желаемому рисунку.
- Нанесите Bond-Kote или Micro-Bond и легкими движениями проведите по влажному продукту метлой или щеткой для стружки. Идея состоит в том, чтобы свести текстуру к минимуму.
- Когда материал начнет схватываться, можно слегка сбить текстуру шпателем.
- После высыхания продукта можно удалить ленту и начать окрашивание. Чтобы добиться максимально аутентичного вида, подрядчики окрашивают каждую доску индивидуально. Этот метод окрашивания трудоемок и требует некоторого художественного мастерства.
- Метод цементированной текстуры метлы (внутренняя часть)
Кто угодно — от опытных профессионалов до новичков в бетоне — может добиться наиболее аутентичной отделки из искусственного дерева с помощью метода затирки. Готовый пол — самый гладкий из всех методов, к тому же его легче воссоздать для будущих работ.
Техника:
- Нанесите резиновый слой Super-Krete Bond-Kote. Однако на этот раз вам нужно будет полностью окрасить это покрытие желаемым цветом затирки.
- После высыхания заклейте рисунок деревянной доски лентой с пропиткой волокнами (1/4 дюйма или 1/2 дюйма).
- Нанесите еще один слой Bond-Kote, полностью окрашенный так, как должна выглядеть текстура древесины.
- Пока еще влажный, щеткой протяните шпателем по направлению к доскам.
- И вот здесь происходит волшебство: после высыхания нанесите Super-Krete Micro-Bond волшебным шпателем на текстуру древесины. Это покрытие должно действовать как затирка.
- После затвердевания слегка отшлифуйте пол, чтобы обнажить выступы цветной текстуры.
- Последний шаг — покрасить пол. Распылите краску для бетона по всему полу.
Деревянный каркас, бетон из опилок, здание в стиле вуфати (форум вофати и земляных валов в Перми)
https: // www.motherearthnews.com/green-homes/building-a-sawdust-concrete-home-zmaz78jfzgoe«Вот смесь, которую он использовал: одна часть цемента, одна часть диатомитовой земли, три части опилок, три части стружки и одна часть глины … все измерения объема. Так как бетон из опилок имеет более высокое поглощение по сравнению с прямым бетоном, Фриберг добавил в смесь одну часть глины ».
Я хочу построить дом. Я действительно люблю вофати, но у меня нет тяжелого оборудования или группы помощников.У меня есть лес, который нужно прореживать, и соседи с лесопилками. Итак, я пришел к этой смеси идей. Я могу получить помощь в расчистке леса и установке рамы. Надеясь, что я смогу установить каркас между столбами и залить цемент из опилок, затем переместить его и сделать еще один слой, вроде того, как вы строите из булыжника. Но просто делаю доску с каждой стороны и наращиваю слои, как могу. Я не совсем уверен, что это имеет смысл, поэтому попробую нарисовать картинку.
~ Кладочный цемент 75 # мешок за 10 долларов
~ Диатомовая земля 40 # $?
~ возможно без опилок
~ глинистый грунт, свободный
~ повторно использованный брезент для рекламных щитов 14 x 23 футов 30 долларов США плюс доставка
Думаю, я посмотрю, смогу ли я сколотить кирпичную форму с деревянным ломом.У меня есть немного DE, я мог бы попробовать смешать его и посмотреть, как это получится. Я всегда найду применение кирпичам!
Что касается здания … Я еще не уверен, насколько оно будет большим. Может быть, крохотный дом размером с дом. Было бы здорово быть достаточно большим, чтобы я мог более или менее жить в нем.
~ Посты в
~ Каркас фальшпола, засыпать гравий и отшлифовать
~ Каркасная крыша, бетон на опилках
~ Пол из опилочного бетона
~ Каркасная основа стен, первый слой бетонных опилок
~ Если установлено удаление кадра, установите кадр сразу над первым слоем и добавьте второй слой.Если у меня есть что-то вроде досок 2×6 для каркаса, в который можно залить бетон, тогда слои должны образоваться довольно быстро.
~ Продолжить наслоение стен, оставляя двери и окна в рамах.
~ Теперь, когда стены и крыша покрыты брезентом.
Вот где мне нужно уйти от обычной идеи wofati. У меня нет техники и нет насыпной грязи. У меня есть .. Опилки. Мусорное сено (заплесневелое и т. Д.). Ветки (прореживание леса). Щепа (рубка ухода за древесиной). Уборка сарая (я и сосед).Поэтому я думаю, что как только я накрою его брезентом, я смогу добавить столько, сколько смогу, чтобы заполнить с течением времени. В первый год я старался как можно больше прикрыть его. Со временем он примет более закрытый вид холма хоббитов.
Это просачивается, но не слишком долго, поэтому не стесняйтесь указывать на возможные проблемы! Особенно более знающие и опытные строители. Спасибо!
Стройте лучше, живите лучше DIY — Как делать асфальтоукладчики с Тимом Везиной
Хорошо, вот сценарий, у вас отличная передняя веранда, но вы следите за пеплом в доме.Один из способов предотвратить это — построить цементную брусчатку. Посмотрите эпизод «Асфальтоукладчики» на сайте Build Better with HPM, чтобы получить пошаговые инструкции.
Первое, что вам нужно сделать, прежде чем отправиться в HPM за расходными материалами, — это измерить пространство, чтобы определить, сколько пакетов Quickrete вам понадобится. В этом примере мы собираемся построить (6) брусчатку размером 20 x 20 дюймов. Чтобы определить, сколько цемента вам нужно будет купить, просто следуйте приведенной ниже формуле или, чтобы упростить задачу, просто спросите сотрудника HPM, и он поможет вам определить правильное количество.
ПОШАГОВОЕ ВИДЕО
Вот список необходимых материалов:
- Бетонная смесь
- Доска обрезная 2 × 4
- Сетчатая проволока
- Ковши
- Deck Nails
И список инструментов, которые нужно иметь под рукой для завершения работы:
- Пила
- Сверло
- уровень
- Инструменты для копания
- Кусачки для проволоки
- Измерительные инструменты
- Силовой миксер или колесная бочка
- Теперь, когда у вас есть список запасов, отправляйтесь в HPM и возьмите то, чего у вас сейчас нет под рукой.
Чтобы сделать брусчатку размером 20 x 20 дюймов, вам необходимо построить каждую коробку со сторонами (2) 20 дюймов и (2) шириной 23 дюйма — это даст вам идеально квадратную коробку. Мы рекомендуем использовать винты, чтобы облегчить снятие (таким образом вы не ударите молотком и не повредите бетон).
ШАГ 2. Разложите брусчатку, чтобы увидеть, где копать, и выровняйте землю
Мы рекомендуем сначала разложить их, чтобы вы знали, какую площадь выровнять.Используйте садовую мотыгу или лопату, чтобы очертить область. Обязательно выровняйте землю перпендикулярно дому с небольшим наклоном вниз по высоте от дома, чтобы обеспечить надлежащий дренаж. Лучше всего устанавливать формы винтами наружу, чтобы сверло могло их легко открутить.
ШАГ 3: Замешивание бетона и заливка
Есть несколько способов замешивать бетон. Один — с электродрелью, лопастью и несколькими ведрами, а другой — старомодным способом с лопатой / садовой мотыгой и тачкой.Вы заметите стрелку на пакетах Quikrete — именно там вы разорвете пакет. Цель состоит в том, чтобы создать влажную смесь, которая сама по себе может стоять примерно на 1/2 дюйма. Помните: всегда лучше иметь больше воды, чем ее не хватать. Когда смесь будет готова, положите сетку и начните заливку бетона. Обязательно отрегулируйте металлическую проводку так, чтобы она располагалась в середине влажного бетона. Чтобы выпустить часть воды и воздуха из смеси, несколько раз постучите граблями по деревянному бордюру.
ШАГ 4: Дать высохнуть
Дайте цементу высохнуть не менее 12-24 часов. Для восточной части острова мы рекомендуем не менее 24 часов из-за большого количества влаги в воздухе.
ШАГ 5: Снимите формы
Постучите по формам молотком, чтобы помочь освободить формы от бетона. Затем открутите бока и поднимите формы. Вы можете потереть молотком края цемента, чтобы они не были такими острыми и рваными.
ШАГ 6: засыпать гравием, декоративным камнем или щепой
Поздравляю, вы только что построили брусчатку … Больше не нужно загонять эти надоедливые угли в дом.Чтобы узнать больше о проектах DIY от HPM, подпишитесь на нашу рассылку новостей НАЖМИТЕ ЗДЕСЬ
.