МДФ: плотность, характеристики, применение, советы
Совсем недавно древесноволокнистая плита отметила свое 50-летие. За это время стало понятно, что с качеством МДФ не идут ни в какое сравнение облицовки другими материалами. За полвека производители успели усовершенствовать этот материал. Сегодня он выпускается в виде панелей и листов. Из них можно сделать мебельные стенки, двери, и облицевать любую поверхность.
Плотность материала
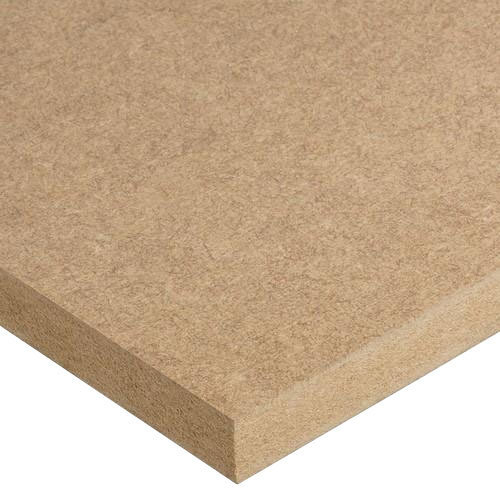
Древесноволокнистая плита изготавливается из мелких опилок. Плиты выполняются из круглого леса и его отходов. На этапе производства сырье перемалывается и претерпевает обработку паром под высоким давлением. Перетертое сырье высушивается и отправляется на склейку и прессование.
Плотность МДФ кг на м3 составляет в среднем от 600 до 850. Эти значения могут быть больше или меньше. Перед приобретением материала обязательно необходимо определиться с этой характеристикой. Качество зависит от этого показателя, тогда как порода древесины не играет особой роли. Понятие плотности — это скалярная физическая величина, определяемая отношением массы к объему. Плотность МДФ-плиты может быть разной, поэтому данный материал подразделяется на категории и обозначается аббревиатурами LDF и HDF.
Первую маркировку следует понимать как «древесно-стружечная древесноволокнистая плита низкой плотности». Этот показатель варьируется от 200 до 600 кг/м3. 2-ая из упомянутых разновидностей — это плита с высокой плотностью. Данный показатель здесь может превышать 800 кг/м3. Высокой и почти всегда одинаковой твердость обладают верхние слои материала, толщина которых составляет 1 мм. Глубже плотность падает в два раза.
Если осуществлять фрезерование по пласту и вскрыть материал изнутри, то можно убедиться: с уменьшением плотности волокна слабее соединяются друг с другом. При обработке плит, которые приближены к ЛДФ, на достаточной глубине отслаиваются слабо скрепленные между собой волокна. Из-за этого на отделке появляются неровности. Для исправления ситуации проводится дополнительная обработка шлифованием и термопрокатом. Это может повлечь дополнительные расходы и увеличение стоимости МДФ.
Характеристики и применение материала средней плотности
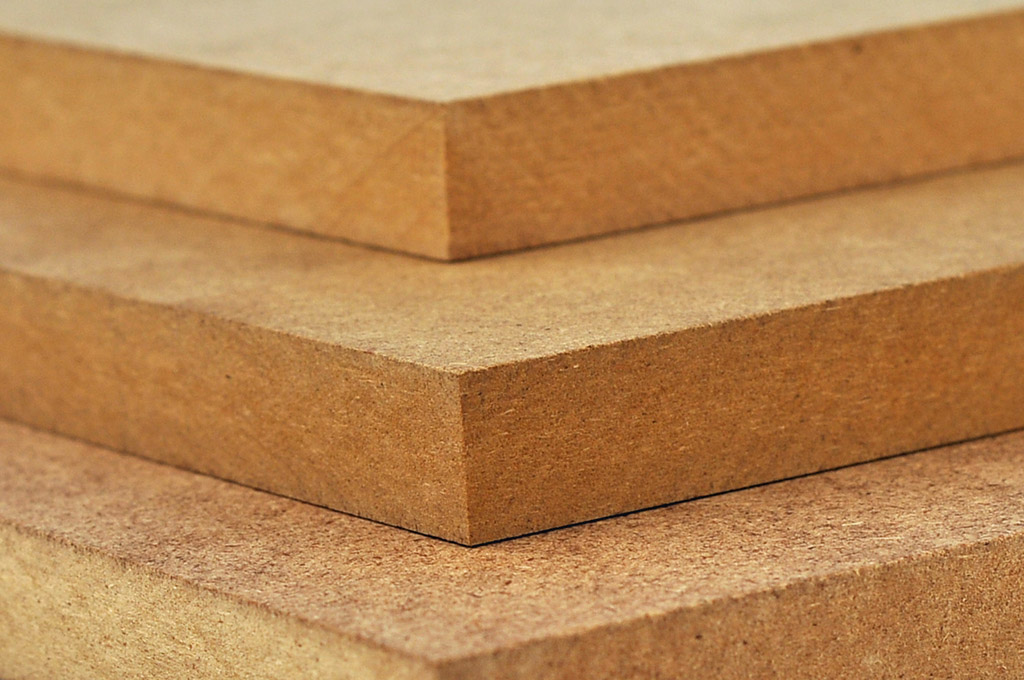
Плотность МДФ варьируется от 600 до 1000 кг/м3. Связующим элементом здесь выступают карбамидные смолы, модифицированные меламином. Это гарантирует низкую эмиссию формальдегида, которую можно сравнить с эмиссией натуральной древесины. Класс эмиссии формальдегида — Е1.
В процессе производства сырью придаются специальные свойства, а именно:
- водостойкость;
- биостойкость;
- огнестойкость.
МДФ средней плотности используется при производстве мебели, а также при отделке помещений. В последнем случае речь идет о создании экономпанелей и стеновых панелей, а также укладке ламинированного напольного покрытия. МДФ подходит для изготовления корпусов акустических систем, ведь материал имеет однородную структуру и хорошо поглощает звук. Он легко обрабатывается и может использоваться при изготовлении шкафов, в частности фасадов с элементами резьбы.
Обрабатывать материал легко, он не теряет стружку, поэтому считается идеальным для создания криволинейных отверстий, форм и фрезерования плоскостей разной глубины. МДФ широко используется при изготовлении коробок и тары для подарков.
Материал с высокой плотностью и его применение
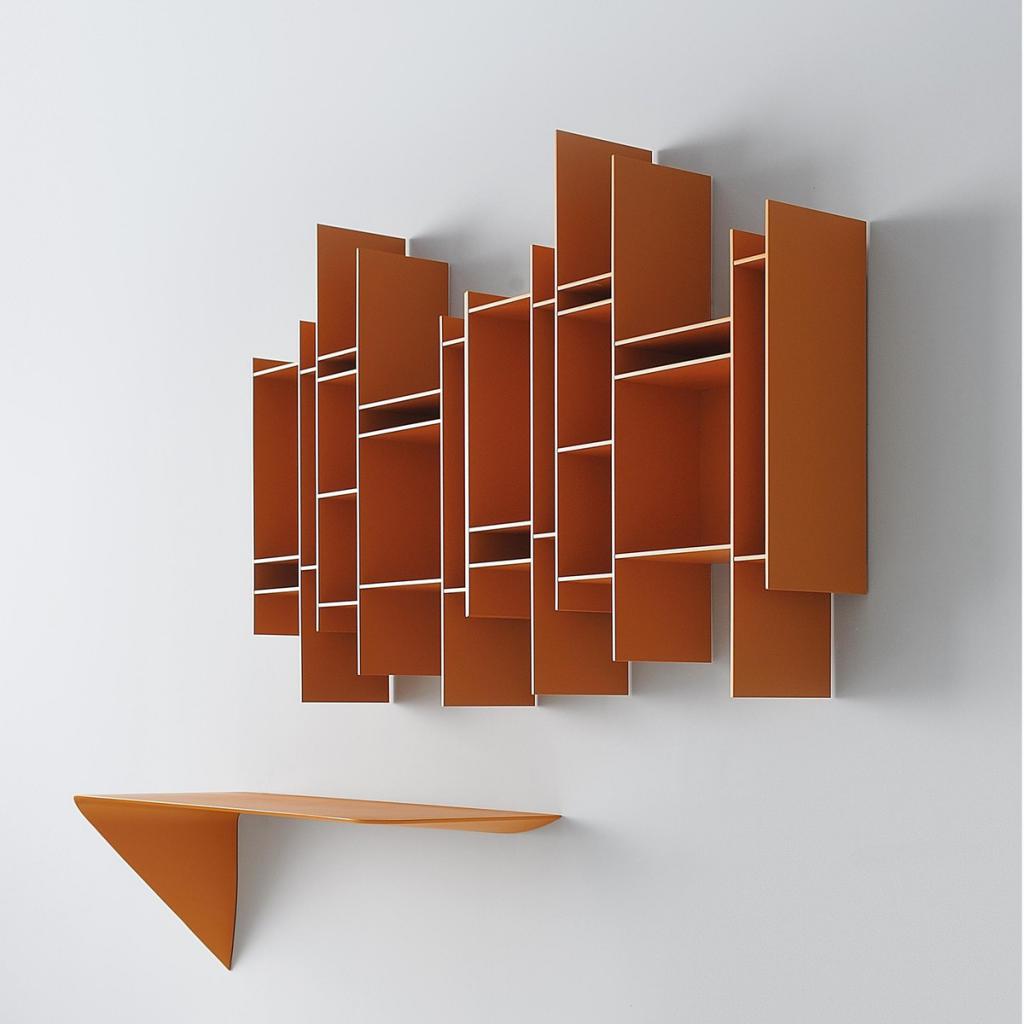
МДФ высокой плотности схож с аналогами низкой и средней плотности. Этот материал имеет высокую прочность, поэтому более надежен. Стандартная толщина составляет 4 миллиметра. Используются такие плиты для достижения следующих целей:
- выравнивания стен;
- покрытия пола;
- изготовления межкомнатных дверей;
- вагоностроения;
- при облицовке салона машины;
- изготовления торгово-выставочного оборудования;
- при необходимости скрыть коммуникации.
Технические характеристики
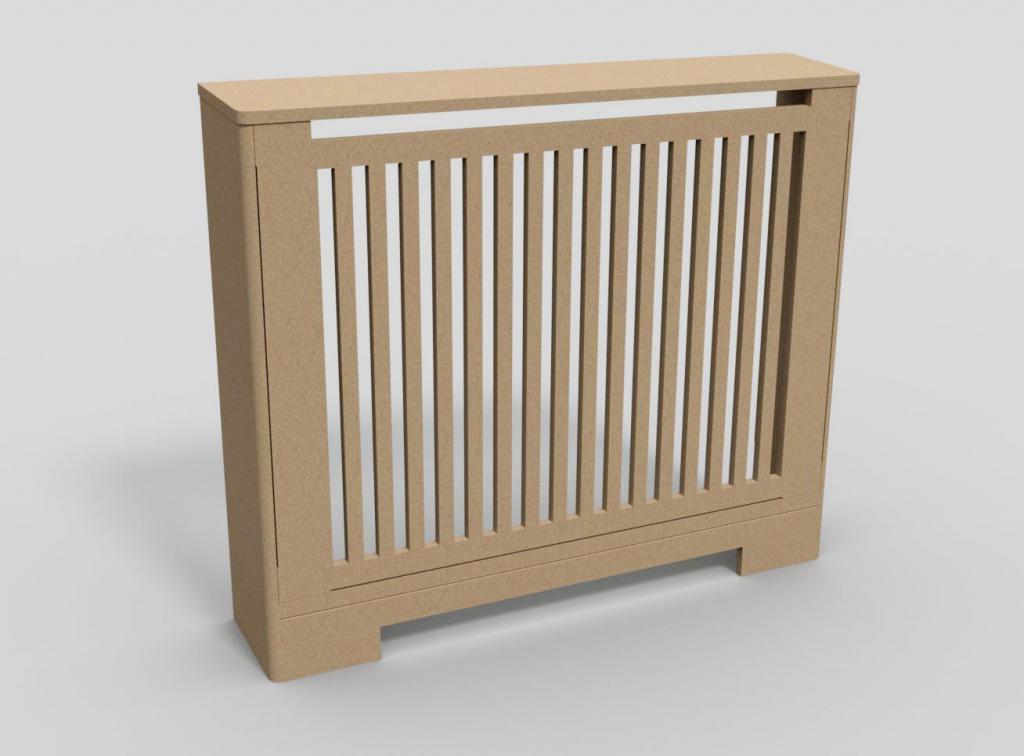
Плотность МДФ 16 мм составляет 780 кг/м3. Но эта характеристика не единственная, о которой вам следует знать. Например, важной особенностью является способность претерпевать давление больше 15 МПа у плит со средней жесткостью. Еще одним достоинством является устойчивость к микроорганизмам и микробам. Вас может заинтересовать еще и влажность материала, которая изменяется от 3 до 10 %. Модуль упругости составляет 1700 МПа. Предел прочности равен 17-23 МПа.
Содержание формальдегида может быть меньше или равно 8. Эти показатели зависят от толщины и размеров листов, также их состава. Плотность МДФ 19 мм составляет 750 кг/м3. Это верно для материала марки Kronopol. Толщина листов может варьироваться от 5 до 25 мм. Если они имеют панельное исполнение, то могут быть:
- листовыми;
- наборными;
- реечными.
Последние представляют собой 10-сантиметровые доски, ширина которых варьируется от 11 до 29 сантиметров. Длина при этом составляет 4 м. Минимальное значение длины равно 2 м. МДФ повышенной плотности может быть представлена наборными квадратными панелями, размеры которых варьируются от 29 до 95 см. Такой вид материала подходит для создания мозаичного рисунка на поверхности.
Что касается листового исполнения, то такая МДФ может иметь размеры от 1,2 до 2,5 м. Узнать толщину материала вы сможете, взглянув на маркировку. Плотность МДФ не менее важна, чем состав материала, в котором может быть больше 90 % опилок. Остальные 10 % приходятся на формальдегиды и смолы. Материал имеет высокую вероятность разлома. Это обусловлено тем, что панели изготавливаются не из цельной древесины. Внутри не содержится опасных для жизни человека веществ.
Советы по раскрою
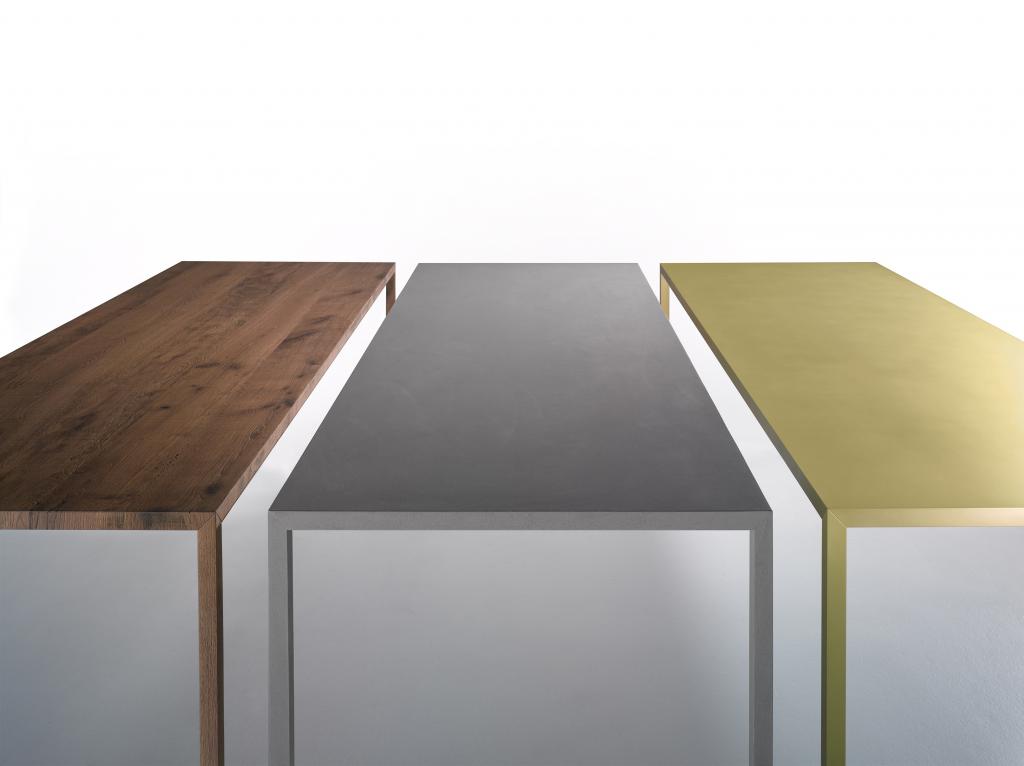
Когда плотность МДФ вам уже известна, можете изучить советы по распилу материала. Лучше всего приобретать изделия со стандартными размерами и с заводской обработкой. Если есть необходимость осуществить распиловку, лучше доверить это специалистам. При этом используются специальные форматно-раскроечные станки.
Мастерам известно, что заготовки укладываются тыльной стороной наверх, если раскрой осуществляется на станке. При запуске пилы движение плит должно быть поступательным и плавным. Зубья погружаются на 1 мм. Правильный раскрой позволяет получить точные заготовки по нужным размерам. Этот процесс является трудоемким, но позволяет получить детали для изготовления мебели и дверей.
Особенности применения МДФ
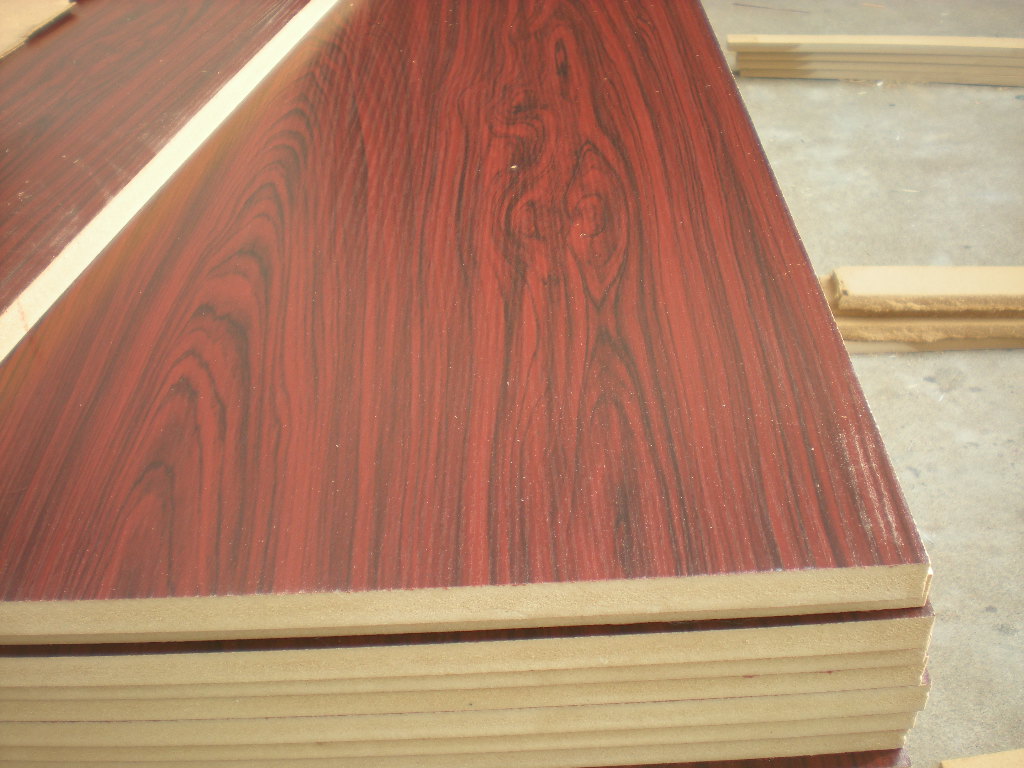
МДФ отлично подходит для установки на разные поверхности. Для проведения работ следует подготовить:
- карандаш;
- строительный уровень;
- уголок для разметки прямого угла;
- ножовку по металлу;
- шуруповерт;
- перфоратор;
- молоток;
- шурупы;
- дюбели.
Приступать к работам необходимо с очистки поверхности, куда будет осуществляться крепление. Основание очищается от грязи и пыли. Нужно произвести тщательный осмотр материала на предмет плесени и грибка. Если планируется сделать потолок из МДФ, понадобятся направляющие профили, деревянные бруски и подвесы. Бруски будут выполнять функцию поперечных деталей каркаса.
А вот если вы планируете крепить панели к стене, будет достаточно брусков из дерева или пластиковой обрешетки. Для того чтобы процесс крепления был проще, следует использовать кляймеры. Это позволит осуществить фиксацию на обрешетке части покрытия, облегчив задачу. Основная сложность заключается в проведении точной разметки под обрешетку, которая позволит закрепить элементы.
Советы по самостоятельному окрашиванию
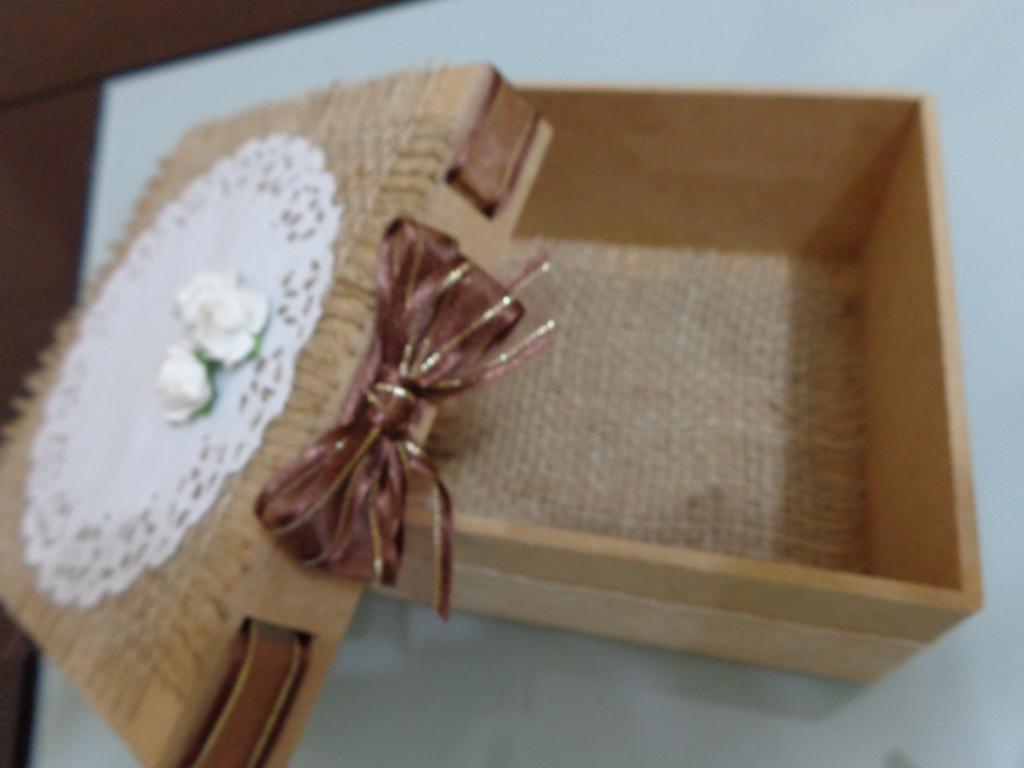
Плиты МДФ хорошо подходят для кухонной мебели и используются в качестве альтернативы пластику. Вы можете приобрести кухню из МДФ с фотопечатью, но если финансы не позволяют, то можно окрасить поверхность плиты в тот цвет, который вам более предпочтителен. В этом случае нужно придерживаться определенного алгоритма действий. На первом этапе поверхность хорошо очищается, моется и ошкуривается.
Затем необходимо протереть ее растворителем. Грунтовка на следующем этапе наносится в 2 слоя с перерывом на высыхание. С помощью кисти или баллона слой краски наносится на поверхность. Можно воспользоваться краскопультом, стоить это будет дороже, но результат получится лучше. После высыхания краски можно нанести поверх слой лака, который придаст изделию блеск и будет выполнять защитную функцию.
Рекомендации по выбору материала
Что касается используемых при обработке МДФ материалов, то в качестве грунтовки лучше выбрать смесь на полиуретановой основе, в состав которой входит вода. Так вы сможете скрыть структуру плиты. Лучше если состав будет в баллончике. Для окрашивания лучше всего применить акриловую краску или полиуретановую эмаль для МДФ. Одним из основных плюсов 2-го варианта является отсутствие запаха. Для финишного покрытия рекомендуется использовать полиуретановый лак. Можно выбрать матовую или глянцевую его разновидность.
В заключение
Плотность МДФ является одним из основных показателей этого материала. Ее следует выбирать в зависимости от поставленных задач. Обращаться в процессе монтажа с материалом необходимо аккуратно, так как он имеет свойство разламываться. Это обусловлено тем, что в основе лежит древесная стружка. Она может быть спрессована с разной плотностью в разных слоях материала. Это следует учитывать при распиливании, ведь в противном случае материал может обрести неровную кромку, раскрошиться и потерять внешний вид. Кроме того, через необработанный край на плиту может воздействовать влага.
МДФ vs ЛДФ: что выбрать для плинтусов и декоративных планок | Интересно
Должен остаться только один
Тысячи статей и сводок о том, какой материал лучше: МДФ или ЛДФ. У каждого свои смотрения на этот счет, поскольку материалы настолько близки по своему составу, что отличия заметны лишь при длительной практике и работе с материалом. Наша редакция решила провести справедливую и независимую оценку битве этих двух популярных материалов. Мы дадим ответы на популярные вопросы, выясним, подходят ли МДФ и ЛДФ для плинтусов и декораций, проведем черту между «цена-качество» и многое другое.
Итак… поехали
С чего все началось
МДФ и ЛДФ – это однотипные по структуре материалы, используемые для изготовления различных элементов декора (плинтуса, молдинги, подоконники), столешниц, мебели и других изделий. Основное их отличие, с технической точки зрения, это плотность (ЛДФ – плита низкой плотности, МДФ средней). Готовый продукт с окрашенной поверхностью невозможно отличить, поэтому у профессионалов возникают споры по теме целесообразности использования MDF и LDF.
А теперь предметно и по порядку.
МДФ. «Ясен красен»
МДФ (Medium Density Fiberboard)
Существенным недостатком МДФ считают его второсортный состав, а это может быть даже переработанная бумага, кора дерева. Чтобы структура плиты была максимально однородной, в ее состав добавляют много формальдегидных смол, что сказывается на экологических параметрах конечных изделий. Также нужно отметить, что из-за своей плотности МДФ имеет умеренный вес, а это не всегда хорошо для изготовления декоративных планок, которые крепятся на легкие клеевые составы.
ЛДФ. Для тех, кто еще не знает
ЛДФ (Light Density Fiberboard) материал, который встречается реже и далеко не во всех случаях. Древесноволокнистая плита низкой плотности изготовляется из отходов обработки сосновых пород дерева, в частности Radiata (использование этого дерева, выращенного не на контролируемых плантациях, строго запрещено). Для придания материалу формы используются прессы высокого давления и специальные клюющие составы на основе натуральных смол (лигнин). Для улучшения влагостойких качеств в ЛДФ добавляют парафин.
Готовые изделия из ЛДФ покрываются специальным грунтом, пропиткой, а также вскрываются несколькими слоями краски. Это придает поверхности роскошного внешнего вида, неотличимого от натуральных и дорогих аналогов. Недостатком ЛДФ можно назвать его малую прочность. Использование такой мягкой формы недопустимо для отделки фасадов, напольных покрытий и торцов.
Ставим оценки
Самое главное отличие четко выражено в технических характеристиках этих двух материалов.
- Данные из таблицы взяты средние для толщины плиты от 10 до 22 мм. Если использоваться материал другой толщины, то параметры характеристик могут меняться.
Технические характеристики материалов — в цифрах | ||
Характеристики | МДФ (MDF) | ЛДФ (LDF) |
Плотность | от 650 кг/м³ до 850 кг/м³ | от 450 кг/м³ до 650 кг/м³ |
Предел прочности при изгибе | 18 – 22 МПа | 16 – 20 МПа |
Модуль упругости на изгибе | 2100 – 2500 МПа | 1600 – 1900 МПа |
Предел прочности при разрыве | 0,55 — 0,6 МПа | 0,5 — 0,55 МПа |
Отрыв поверхности | 0,7 – 0,8 МПа | 0,5 – 0,6 МПа |
Содержание формальдегида | стандарт Е-1 (класс 8) | стандарт Е-1 (класс 8) |
Разбухание по толщине за 24 часа | 10 – 15 % | 17 – 22 % |
Влажность | 3 – 10 % | 3 – 10 % |
Несмотря на полное или частичное содержание формальдегидов, МДФ и ЛДФ относятся к стандарту E-1 (класс 8), который определяет оба материала как экологически чистый и безопасный для человеческого здоровья.
Судя табличным данным, МДФ и ЛДФ практически одинаковы по своим характеристикам, но существенная разница все же есть:
- Прочность. В показателях прочности ЛДФ поступается практически на 20-25%. Это хорошо видно по табличным цифрам из показателей упругости и прочности. Все дело в повышенной прочности МДФ плиты, которая способна лучше выдерживать физические нагрузки.
- Долговечность. Если взять одинаковые условия эксплуатации, отделку или покраску плиты, то МДФ прослужит больше, так как процент разбухания почти на 10% ниже, нежели у ЛДФ. Это говорит о том, что второй раскиснет быстрее при высокой влажности или попадания воды на поверхности. Такими обстоятельствами нельзя пренебрегать при выборе материала.
- Цена. Стоимость МДФ или ЛДФ практически одинакова, все зависит от качества и типа финишной отделки материала.
- Практичность. Здесь ЛДФ забирает лидерство без всяких сомнений. Этот материал с меньшим весом идеально подходит для создания декоративных планок типа молдинга, потолочных плинтусов и других подобных изделий.
- Безопасность. ЛДФ все же является более экологически чистым с натуральным составом, где меньшее количество вредных формальдегидов (за счет меньшей плотности) и второсортных отходов.
Итог
С небольшим отрывом в битве материалов побеждает МДФ, так как является более надежным и долговечным материалом, а на это делают ставку большинство потребителей. Специалисты нашего производства убеждены, что правильная технология изготовления, качественная материальная база и тщательный контроль способны обеспечить превосходные эксплуатационные качества любому из вышеописанных материалов.
Если у вас остались вопросы, звоните по номеру +7 (495) 411-10-61. Квалифицированные сотрудники нашей компании предоставят всю необходимую информацию по материалам и условиям производства.
Автор: «ПрофиЛь» — фабрика декора
МДФ. История создания МДФ
MDF – Medium Density Fiberboard, что в переводе с английского означает «среднеплотное волокнистое покрытие». МДФ — плитный материал, изготавливаемый методом сухого прессования мелкодисперсной древесной стружки при высоком давлении и температуре.
Прототип древесноволокнистой плиты впервые был получен Уильямом Генри Мейсоном, изобретательным инженером из США. В 1924 году он упорно занимался созданием технологии производства картона или, хотя бы, фанеры из отходов лесопильных предприятий – опилок, стружки и щепы. Первая задача – разделение бросовых фрагментов древесины на волокна – более-менее успешно ему удалась. Мейсон создал «паровую пушку», позже названную его именем – труба из стального сплава, с одного торца полностью заварена, с другого имеющая сдвижную крышку, снять которую можно было удаленно. Работала пушка Уильяма Мейсона так – после закладки мелкой щепы и стружек внутрь, залива нескольких литров воды, свободное отверстие плотно затворялось крышкой. Ближе к «заваренному» концу трубы изобретатель размещал газовую горелку – пламя нагревало воду, превращая ее в пар. Выждав, пока давление не достигнет определенного значения, Мейсон тянул за ручку и сдвигал крышку – стремясь уровнять давление, пар вместе с частицами древесины мощным потоком выбрасывало из ствола «пушки» на предварительно выставленный напротив приемный бункер. В результате значительная часть стружек и пр. разделялась на волокна.
Воодушевленный успехом, Мейсон принялся работать над производством бумаги. Однако ни бумаги, ни даже картона из древесных волокон создать не удалось – даже в расслоенном состоянии древесные частицы были чрезмерно крупны. Не привыкший сдаваться просто так, Уильям Мейсон переориентировался на получение древесной плиты, которую можно было приспособить под стройматериал. Арендовав паровой пресс старой модели, американский изобретатель поместил древесные волокна на его нижнюю плиту, аккуратно распределив их в форме ковра. Поскольку эксперимент проводился из волокон, полученных при помощи «пушки» с утра, их укладку Мейсон планировал к обеду. Он рассчитывал запустить пресс на полтора-два часа, не более, но голод вынудил его оставить эксперимент и отправиться домой на обед. И если бы не две ошибки, допущенные в тот день Уильямом Мейсоном, то древесноволокнистые плиты были бы созданы значительно позже – инженер не проверил все узлы старого пресса на исправность (паровой клапан на верхней прижимной плите протекал) и позабыл отключить пресс перед тем, как направиться к обеденному столу. А путь от лесопилки, где проводились исследования, до дома инженера был не близок…
Древесноволокнистый ковер находился в прессе под воздействием давления и пара длительный срок. После плотного обеда Мейсон вернулся на лесопилку и заметил, что паровой пресс по-прежнему работает, что из щели между плитами выходит пар, но то, что он увидел после отключения прибора и подъема ползуна (верхней, подвижной плиты), привело изобретателя в восторг. Под воздействием раскаленного пара и давления древесный лигнин склеил волокна в достаточно плотную плиту, не разрушающуюся при подъеме за один из краев. Вскоре Уильям Мейсон запатентовал «масонит», как он назвал изготовленную древесноволокнистую плиту. Кстати, масонит производится по сей день – в России такие плиты, с одной стороны гладкие, а с другой шероховатые, называются оргалит (ДВП).
До середины XX века потребности в плитах из древесных волокон не существовало, хотя их технологические компоненты – тот же масонит Мейсона и первая фенолформальдегидная смола «бакелит» химика Лео Бакеланда – были уже известны промышленникам. Серийный выпуск плит MDF стартовал в США ближе к концу 60-х, причем одновременно на нескольких предприятиях, принадлежавших различным компаниям. Все производители использовали в те годы схожую технологию выпуска древесноволокнистых плит, с уверенностью назвать среди них первую компанию-изготовителя не представляется возможным.
В Советском Союзе «толстые» плиты из древесных волокон не производились – считалось, что древесно-стружечных плит (ДСП) более чем достаточно. С ориентацией на российскую мебельную промышленность первое производство отечественных древесноволокнистых плит стартовало в поселке Шексна (Волгоградская обл.) в 1997 году. С начала XXI века Китай – мировой лидер в производстве плит MDF, а также мебели и прочих изделий из этого материала.
Технология производства МДФ плит
Первый и повсеместный метод изготовления плит из древесных волокон был «мокрым» и мало чем отличался от техники выпуска картонных листов. Впоследствии была разработана технология, позволяющая обходиться без воды – именно ее используют производители MDF сегодня. Рассмотрим этапы «сухого» выпуска древесноволокнистых плит средней прочности.
Заготовка щепы. Породы древесных стволов, поступающих на производство МДФ плит, могут быть различными – в составе одной и той же плиты, как правило, волокна нескольких деревьев. Лес-кругляк помещают в станки барабанного типа, в процессе вращения которых встроенные ножи полностью срезают и удаляют кору. Далее, в дезинтеграционных машинах, оснащенных массивными рубящими ножами, окоренный кругляк становится щепой. Помимо разделки древесины на щепу, рубка снижает связи между волокнами, которые обеспечивает древесный полимер лигнин. Нарубленная щепа поступает на конвейерную ленту и следует под несколькими электромагнитами, извлекающими из нее частицы металлов. Следом щепу сортируют в виброситах – излишне крупная вновь идет на рубку, чрезмерно мелкая щепа поступает в бункер-накопитель отходов и затем будет сожжена в печах котельной. Древесные частицы необходимого диапазона размеров направляется на мойку в циклоны вертикальной установки – в них из щепы устраняется мусор и примеси минералов. Подготовленная к следующей операции – обработке паром – щепа следует в бункер, где прогревается до температуры в 100°С с доведением степени ее влажности до 80% по всему объему.
Получение древесного волокна. Горячая и влажная щепа загружается в специальную установку – дефибратор (второе название – рефинатор) — размалывающий аппарат дискового типа. Шнек питателя прогоняет частицы древесины через каскад лопаток дисковой и конической формы, разделяя их на волокна. Операция деления повторяется два-три раза, для этого необходимое число установок-дефибраторов выставляются друг за другом в единый каскад. Для более эффективной разбивки щепы на волокна в емкость дефибраторов закладываются фенолформальдегидные смолы, парафин, связующие материалы и отвердители.
Полученные в дефибраторах древесные волокна направляются в сушилку, в процессе следования они постоянно обрабатываются паром. Внутри сушилки на волокна воздействует уже не пар, а сухой воздух, имеющий температуру в диапазоне от 170 до 240°С – срок сушки короток, не превышает 5 секунд. Осушенные волокна древесины (влажность не более 9%) загружаются в циклон, задача которого – вывести из массы волокон избыточный объем воздуха. Волокна, готовые к производству древесноволокнистых плит, накапливаются в бункере.
Образование ковра и прессование плит МДФ. При движении по конвейеру древесным волокнам придается форма непрерывного ковра, для чего поток волокон прикатывается роликами (см. фото).
Первичное прессование волокнистого ковра проводится при помощи обычного пресса и преследует одну цель – полностью устранить из будущей MDF плиты воздух. По окончании этой операции выполняется основное прессование (горячее), проходящее в три этапа:
придание плите поверхностной жесткости. Под давлением около 350 МПа, развиваемым плитой-ползуном и при температуре в 200-230°С древесноволокнистый ковер приобретает первичные свойства плиты МДФ;
упрочнение внутреннего слоя плиты. Давление в прессе снижается до 50-120 МПа, температура нагрева – до 190-210°С, в результате связующие компоненты в составе уплотненного ковра из древесных волокон формируют прочные связи внутри изделия;
калибровка древесноволокнистой плиты. Сформированную плиту необходимо довести до требуемой толщины, для чего ее опрессовывают под давлением в 60-150 МПа без нагрева.
Готовая плита МДФ непрерывной полосой выходит из-под калибровочного пресса, далее ее нарезают на блоки заданных размеров циркулярными пилами. Разрезанные плиты укладываются на стеллажи для охлаждения, на эту операцию уходит порядка 25 минут. Несмотря на серию прессовочных работ плиты MDF все же имеют некоторые поверхностные изъяны и небольшой, в несколько миллиметров, перепад по толщине. Их устраняют на плоскошлифовальных станках. Готовая продукция маркируется и помещается на склад, либо следует в цех, где поверхностям плит придается декоративная отделка.
Характеристики МДФ
Госстандарта России на древесноволокнистые плиты средней плотности не существует, производители МДФ либо разрабатывают собственные технические условия, либо выпускают плиты по европейскому стандарту ANSI A208.2. Производятся плиты МДФ первого и второго сорта, толщиной от 6 до 24 мм. Cклеивание древесных волокон осуществляется при помощи карбамидоформальдегидных смол и древесного лигнина. Многими производителями в качестве связующего элемента заявляется только лигнин: мол, никаких экологически вредных компонентов не присутствует — это неправда, МДФ панелей и плит, созданных только при помощи лигнина, в действительности не существует. Стандартные размеры панелей МДФ: 1650 на 1650 мм, 2800 на 1650 мм, 2750 на 1650 мм, 2 250 на 1650 мм и 2440 на 1650 мм. Также производятся панели «дополнительных» размеров — 3660 на 1650 мм, 3050 на 1650 мм, 2100 на 1650 мм и 1850 на 1650 мм. Поверхности панелей МДФ I сорта не имеют ровным счетом никаких дефектов — они идеально ровные, без сколов, царапин и каких-либо пятен. Плиты II сорта могут иметь царапины глубиной не более 0,3 мм и не длиннее 20 мм, небольшие сколы на кромках, небольшие по площади дефекты шлифовки. МДФ III-го сорта подходит только лишь для строительных нужд, т.к. имеет множественный сколы и дефекты поверхностей. Плотность выпускаемых плит МДФ лежит в пределах от 600 до 1200 кг/м3. Класс эмиссии (выделение свободного формальдегида со 100 г массы) для любого сорта МДФ — E1, т.е. не превышает 10 мг. Любая панель МДФ обладает высокой влагостойкостью и чем толщина панели больше, тем более высока ее влагостойкость — максимальное разбухание для плит толщиной 6-8 мм не превышает 17% от исходного объема МДФ. В процессе производства плитам МДФ могут быть приданы более высокие качественные свойства по водостойкости, огнестойкости и биостойкости, чем у серийных плит.
Применение МДФ
МДФ — очень плотный и однородный материал, что делает его устойчивым к влаге и горячему пару, грибкам и микроорганизмам. Именно поэтому плиты МДФ широко используются при изготовлении кухонной мебели, ведь они очень хорошо переносят воздействие кухонного пара, не разбухают, не коробятся. Разработанная техника гнутья конструкционных элементов из склеенного древесного волокна позволила создавать из этого материала кресла и стулья, изящные спинки кроватей. Как правило, вся мебель для помещений с высокой атмосферной влажностью (санузлов, кухонь) выполняется из шпонированного или ламинированного МДФ. Плиты из МДФ также могут применяться для устройства межкомнатных перегородок, но для настила полов они не пригодны вследствие их механической уязвимости. Панели из этого материала широко используются в декоративном оформлении интерьеров — в отделке потолков и построении воздуховодов. МДФ используют для изготовления дверных блоков вместе с коробами и наличниками из того же материала. Из МДФ изготавливают ламинированные наличники и накладки на входные двери. В строительстве популярны тавровые балки из МДФ, применяемые в качестве сердечника балок межэтажных перекрытий при монолитном строительстве. Водостойкое МДФ используется для обрешетки крыш — элементы такой обрешетки окрашиваются для более долгой службы масляной краской.
Достоинства МДФ
К достоинствам МДФ относится способность сохранять долгое время геометрические параметры, что позволяет говорить о длительном сроке службы. Изделия из МДФ допускается использовать в помещениях с высокой влажностью воздуха – пропитки сохраняют плиты от развития плесени и грибка, от деятельности насекомых. Тем не менее, панели МДФ не рекомендуются к установке в помещения с постоянно высоким уровнем влажности воздуха, за исключением их водостойких модификаций. МДФ – хороший утеплитель и звуковой изолятор. Можно усилить эти свойства, уложив под него изолирующий материал. Самый большой плюс МДФ — благоприятное соотношение между толщиной и твердостью. Это материал имеет однородную, плотную, ровную, гладкую поверхность, что делает обработку плит быстрой и легкой. Плотность материала составляет от 600 кг/м³ до 800 кг/м³, что немало. Прочность МДФ в 1,8-2 раза выше прочности древесностружечных плит. Благодаря гладкой и твердой поверхности плиты МДФ прекрасно подходят для отделки прогрессивными методами ламинирования, каширования, для фанерования тонким шпоном, имитационной печати, покрытия лаками и эмалями. При наличии необходимых инструментов можно выпилить в панели любые узоры, украсить декоративной вырезкой. При этом исключаются известные недостатки массивной древесины: анизотропность свойств в зависимости от направления древесных волокон, склонность к растрескиванию при изменении температурно-влажностных условий эксплуатации и т. д. МДФ прекрасно раскраивается твердосплавными пилами. При сверлении МДФ используются те же инструменты, которые применяются для фанеры и ДСП. Достигаются отличные результаты при фрезеровании кромок и поверхностей. Структура МДФ гарантирует исключительно высокое качество при высоких скоростях обработки. Для склеивания МДФ подходят все имеющиеся марки клеящих веществ древесины. В процессе производства МДФ можно придавать специальные свойства: огнестойкость, биостойкость, водостойкость. Также стоит отметить относительно невысокую стоимость МДФ. Панели МДФ требуют минимального и простого ухода – достаточно изредка протирать плиты влажной салфеткой или одним из специальных средств, которые сегодня в избытке продаются в магазинах.
Недостатки МДФ
К недостаткам плит МДФ относится их легкая воспламеняемость при контакте с открытым огнем. Также стоит отметить не очень высокую устойчивость к механическим повреждениям: случайное падение тяжелого предмета на поверхность МДФ может оставить вмятину. Что касается работы с МДФ, следует заметить, что вбить гвоздь или вкрутить шуруп в МДФ будет практически невозможно, требуется предварительное высверливание отверстия под крепление. Во время обработки и фрезеровке плит образуется много пыли — обязательно использование респиратора. МДФ плиты имеют на порядок больший вес по сравнению с деревянными плитами такого же размера. Несмотря на заявляемую некоторыми производителями экологичность, это не совсем так. Да, класс эмиссии МДФ низок и практически равен природной древесине, но выделение формальдегида все же присутствует. То есть, хотя МДФ плиты и сравниваются с деревом, но они не настолько экологичные.
МДФ в России
Сегодня на российском рынке листовых строительно-отделочных материалов представлены древесно-волокнистые плиты средней плотности как отечественных, так и зарубежных производителей. Наибольшее распространение получила продукция таких брендов, как: Kronospan (Россия, г. Егорьевск), Kronostar (Россия, г. Шарья), Шекнинский КДП (Россия, Вологодская обл.), Glunz AG (Германия), EGGER (Австрия), Коростеньский завод МДФ (Украина).
Что такое мебельный МДФ
Наиболее универсальный материал, максимально широко используемый в изготовлении предметов мебели и не менее активно применяемый в строительной отрасли, МДФ характеризуется широкой цветовой гаммой, отличными техническими параметрами и довольно доступной стоимостью. Производители, принимая во внимание, две наиболее обширные сферы использования, предлагают этот материал в форме листов и панелей. Оба варианта имеют отличные качества и длительный срок службы.
Что такое МДФ в мебели?
Данный материал представляет собой древесно-волокнистую плиту средней плотности. Ее производят из мельчайших древесных опилок. Отметим, что используемые для изготовления МДФ опилки более мелкие, чем для производства ДСП.
Плиты отличаются ровностью, однородностью, гладкой поверхностью и высокой плотностью. Их легко обрабатывать и облицовывать, просто фрезеровать. Без проблем делаются отверстия любой глубины и формы. Во время сверления плита не крошится, не сыпется стружка. Легко наносится даже сложный узор. К природному материалу она очень близка, но стоимость значительно ниже цельного дерева.
Такой материал имеет высокий уровень влагостойкости, выдерживает до 80% влажности. Примечательно, что прочие древесные материалы выдерживают лишь 60%. По этой причине данное сырье отлично подходит для изготовления предметов мебели, которые будут эксплуатироваться в условиях высокой влажности, к примеру, в ванне или на кухне. Плита прекрасно держит крепежные материалы. Невзирая на высокую прочность, МДФ характеризуется и гибкостью. Из нее получаются предметы округлой формы.
Существует несколько методов отделки этого материала:
- шпонирование – плита покрывается листом шпона натуральной древесины. После этого она становится схожа с древесиной не только по внешним показателям, но и по качеству
- облицовка пластиком
- нанесение ПВХ-пленки. В том случае, если на фасад нужно будет наносить рисунок, то сначала фрезеруется поверхность, после чего покрывают пленкой, проникающей во все углубления узора
- окраска особыми видами эмали.
Стоимость МДФ плиты зависит от способа декорирования. Например, крашенное сырье имеет более высокую стоимость, чем с ПВХ-пленкой. Если вы хотите сделать красивую и функциональную мебель с привлекательным рисунком и древесной базой, смело покупайте древесно-волокнистые плиты.
Мебельный материал МДФ
Мебельный МДФ имеет высокую популярность вследствие таких показателей:
- высокий уровень влаго — и термостойкости
- небольшой вес
- высокая прочность, и, следовательно, сопротивляемость механическому действию и износу
- существенный уровень шумопоглощения, звукоизоляции
- стойкость к поражению микроорганизмами
- меньшая стоимость в сравнении с цельным массивом.
Высокие эстетические свойства плиты, которая изготовлена по «зеленой технологии», являются широким простором для дизайнерских решений. Натуральный плотный материал используется почти во всех промышленно-бытовых сферах, которые используют натуральную древесину, существенно подвинув своего дорогого «конкурента» более доступной стоимостью.
Самые распространенные области использования МДФ:
- изготовление различных видов мебели, к примеру, кухонные гарнитуры, спальни, столы
- столярные изделия и их элементы, перегородки, оборудование для выставок, интерьерная и акустическая атрибутика, подвесные потолочные системы, отделка стен
- основа под ламинированные полы
- черновой пол
- выравнивание стен
- складская упаковка, тара многоразового применения
- фасады, рекламные вывески, наружные конструкторские решения.
Материал для мебели МДФ
В результате однородной плотности и простоты механической обработки, МДФ шлифованная используется в большинстве промышленно-бытовых отраслей. К примеру, данный конструкционный материал толщиной 6-8 мм используется для отделки стен, изготовления потолочных конструкций элементов. Из плит толщиной 16-30 мм производят фасады для различной мебели, профилированные столешницы.
В процессе изготовления столярных изделий, перегородок и главных конструкционных составляющих мебели применяют шлифованную МДФ от 30 до 60 мм, которая показывает прекрасные физические свойства во время сверления, фрезерования, создания пазов.
Технические характеристики МДФ
Определенные характеристики МДФ позволяют ставить его выше древесины. К примеру, плиту МДФ можно согнуть под любым углом, для создания мебели. Стоит отметить, что древесноволокнистая плита средней жесткости может выдерживать давление более 15 МПа. Еще одним огромным достоинством МДФ является невосприимчивость к грибкам и прочим вредителям.
Компании, которые выпускают этот материал, обязаны придерживаться установленных государственных стандартов. А в них прописано, что средний уровень плотности МДФ должен составлять от 720 до 980 кг/м3.
Маркируются плиты двумя аббревиатурами:
- LDF – плита, имеющая низкую плотность, в среднем от 200 кг/м3 до 600 кг/м3
- HDF – плита, имеющая плотность более 800 кг/м3.
Уровень плотности характеризует не только качество мебели МДФ, но его стоимость.
МДФ панели
Бывают:
- ламинированные. Такой материал пользуется наибольшей популярностью. Чтобы получить ЛМДФ на плиту наносят пленку ПВХ, которая может имитировать структуру цельной древесины. Кроме этого, она отталкивает пыль и повышает устойчивость панели к механическому воздействию
- крашенные панели получают путем окрашивания плит высококачественными покрытиями, которые характеризуются устойчивостью к химическим реагентам. Поверхность после окраски приятно блестит и становится более защищенной
- шпонированные панели – отделаны шпоном дорогостоящих сортов лесоматериалов. Таким изделиям можно придавать различные оттенки.
Изготовление плит МДФ сегодня представляет собой высокотехничный и современный процесс. Применение в изготовлении натурального сырья говорит о том, что конечный продукт относится к ряду экологически безопасных, в то время как процесс его производства не является трудоемким.